Properties and Applications of Thermoset Plastics
1.Phenol-Formaldehyde (PF)
Polics are thermosetting resins which are typically stiff and brittle. Phenolic resins were first tigated in the 1880s by Otto Bayer. In 1909, Dr. Bakeland produced the first commercial phenolic ing compound. But it was Harry H Dent founder general Plastics, who in 1921 developed the first nuous process for making phenolic moulding pounds. Phenolic resins are manufactured by plining phenol and formaldehyde. Two types of polic resin namely resols and novolaks are manuactured. Resol refers to a phenolic resin made acting 1.2 to 1.5 moles of formaldehyde with one of phenol in basic medium. Novolak is the resin the by reacting 0.8 mole of formaldehyde with one of phenol in acidic medium. The approximate tures of resols and novolaks are shown below:
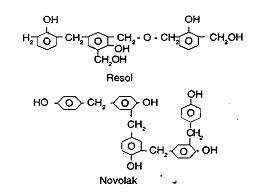
Characteristics
- Hard, stiff & brittle
- Notch sensitive
- Good retention of properties at elevated temperatures
- Impact strength reduces with increase in rigidity
- Excellent creep resistance
- Good ageing properties
- Excellent flexural fatigue resistance
- Heat resistant
- Good dimensional stability
- Does not melt or soften on exposure to heat
- Very good shear strength
- Unaffected by hydrocarbons, oils, salt water, soap and detergent solutions
- Good resistance to staining
- Good insulation properties
- Attacked by strong mineral acids & bases
- Easy to mould
- Excellent ability to be moulded to close tolerances.
Properties |
Values |
Specific gravity |
1.40 |
Tensile strength, MPa |
48.3 |
Tensile modulus, MPa |
8276 |
Flexural modulus, MPa |
7042 |
Elongation at break, % |
1 |
Impact strength, izod, notched, J/m |
16.5 |
Hardness |
E85 |
Deflection temperature under load (1.82 MPa),°C |
150 |
Coefficient of linear expansion mm/mm/°C |
39 x 10-6 |
Water absorption, 24 hours, % |
0.50 |
Dielectric strength, KV/mm |
8.87 |
Dielectric constant, 106Hz |
5.5 |
Power factor |
0.06 |
Volume resistivity, Ohm.m |
109 - 1013 |
Phenolic resins are available in the following grades:
- General-purpose grade
- Heat resistant grade
- Impact modified grade
- Glass filled grade
- Mineral filled grade
- Cellulose filled grade
Phenolic resins can be processed by the following techniques:
- Compression moulding
- Transfer moulding
- Thermoset injection moulding
Manufacturers/Suppliers |
Trade Names |
Fiberite Corpn. |
Fiberite |
Union carbide |
Bakelite |
Toshiba |
Tecolite |
Sterling |
Sternite |
Allied Chemical |
Plaskon |
BP Chemical |
Cellobond |
General Electric |
GE-Genal |
Monsanto |
Resinox |
Synthetic resins |
Uraver |
Dynamit Nobel |
Trolitan |
Budd Chemical |
Polychem |
Plastic Engineering |
Plenco |
Tipco Polymers Pvt. Ltd. |
Tipcolite |
Bakelite Hylam Ltd. |
Bakelite |
Indian Plastics Ltd. |
Florite |
Applications
Appliances: Iron-handles, domestic utensils, heat proof buttons, bottle closures, novelty items, mixie bases, cooking range parts, tube bases, boiler and panels, steam irons, coffee pot bases & handles, knobs, washing machine agitators, toaster ends, phonograph records, coatings for metal cans, refrigerator controls, window tracks, particle boards, glues, laminating wood and water outlets.
Miscellaneous: Bathroom fixtures, toilet seats, dinner wares, cooking range parts, rubber tackifer, butyl rubber curative, fibre glass & paper impregnation, foundry hot box, textile impregnations and X-ray shields.
Automotive: Auto coil tops, disk brake pistons, disconnect boxes, propellers, break linings, shell modelling, brake liners, gear, clutch disks, push buttons, lamp sockets, ignition parts, castor wheels, thrust washers, spacers, converter reactors, car instrument panels, speedometer housings, solenoid covers, commutators for window lights, bus bar supports, engine blocks and intake manifolds.
Electrical/Electronics: Fuse boxes, holders, connectors, lamp sockets, heat resistant lamp holders, fan regulator covers, rotary switches, circuit breakers, HRC fuses, telephone handsets, cyclostyling drums, relay base covers, power transmission components, insulators, pumps, automatic transmission reactors, dielectric housings, power train components and terminal blocks. Industrial/Mechanical: Water pumps, pulleys, calibration in circuit breakers, propellers, grinding wheels, bobbins and sleeves, rice rollers, carbonless copy paper, adhesive paints, tool handles, industrial items, textile components, textile drums, welding torches and picker bushes.
2. Amino Plastics
Urea-formaldehyde (UF) and Melamine-formaldehyde (MF) are called as amino plastics. These resins are derived from ammonia and hence they are referred as amino plastics. Urea formaldehyde was first produced in 1920s by Kurt Ripper & Firtz Pollac in Germany. Urea formaldehyde was commercialised in the year 1932 in America by the American Cyanamid Co. Melamine formaldehyde was commercialised in 1939 at American Cyanamid Co. When Urea or melamine is reacted with formaldehyde a clear thermosetting resin of urea formaldehyde or melamine formal dehyde is produced.
Characteristics
- Stiff & brittle in nature
- Hardest of all plastic materials
- High modulus of elasticity
- High mechanical strength and wear resistance
- Free from taste and odours (compatible with foodstuffs)
- Good electrical properties
- No tendency to yellowing
- Can withstand low temperatures without embrittlement
- Good impact strength
- Continuous use temperature for urea is 77°C and for melamine it is 99°C
- UF & MF retain their properties even at 100°C and 130°C respectively.
- Provides good surface durability and hardness
- Good torque retention
- Break resistant and chip resistant
- Possesses good rigidity and load bearing strength
- Resistant to organic solvents, oils, greases and fluorinated hydrocarbons
- Melamine possesses good stain resistance and freedom from yellowing
- Long-term oxidation resistance is poor
- Very hard and scratch resistant
- Melamine is waterproof in nature
- Self extinguishing
- Good colourability
- Translucent to opaque in nature
- Resistant to gasoline, acetone and detergents
- Melamines are resistant to acids and alkalies and can withstand boiling water
- Attacked by strong acids and bases
<td colspan='2' align='center'>Values
Properties |
|
UF |
MF |
Specific gravity |
1.5 - 1.6 |
1.5 - 1.55 |
Tensile strength, MPa |
52 - 80 |
55 - 83 |
Tensile modulus, MPa |
9000 - 11000 |
11000 - 16500 |
Flexural modulus,Kg/cm2 x 102 |
105.06 |
77.52 |
Elongation at break, % |
[1 |
1.6 - 2.4 |
Impact strength, izod, notched, Kg/cm/cm |
1.36 - 2.18 |
1.31 - 7.62 |
Hardness |
M 110 - 120 |
M 115 - 125 |
Deflection temperature under load (1.82 MPa),°C |
125 - 145 |
175 - 200 |
Coefficient of linear expansion, mm/mm/°C |
2.5 x 10-5 |
4 x 10-5 |
Refractive index |
1.54 - 1.6 |
1.58 - 1.6 |
Dielectric strength, KV/mm |
14 |
12 |
Dielectric constant, 60 Hz |
7 - 9.5 |
7.9 - 9.5 |
Power factor |
0.035 - 0.043 |
0.03 - 0.083 |
Volume resistivity, ohm.cm |
1-2 x 1012 |
1012 - 1013 |
MF is available in the following grades:
- Moulding grade
- Filled grade (cotton fibre and wood flour)
- Glass filled grade
- Alpha cellulose filled grade
- Coating grade
- Adhesive and bonding grade
- Laminating grade
UF is available in limited grades than MF:
- Moulding grade
- Filled grade (cotton fibre and wood flour)
- Alpha cellulose filled grade
Both UF and MF can be processed by the following techniques:
- Compression moulding
- Transfer moulding
- Injection moulding
Manufacturers/Suppliers |
Trade Names |
Urea Formadehyde |
|
Allied chemicals |
Plaskon |
BASF |
Basoper |
BIP |
Beetle, Mouldlite |
Monsanto |
Resimene |
Sterling |
Sternite |
Nuchem Plastics Ltd. |
Presrite |
Melamine Formaldehyde |
|
Allied chemicals |
Plaskon |
American cyanamid |
Cymel |
BIP |
Melamex |
Dynamit Nobel |
Ultrapas |
Monsanto |
Resirnene |
Plastics Engineering |
Plenco |
Indian Plastics Ltd. |
Florite |
Applications
Melamine Formaldehyde
Adhesives: Plywood bonding agents, laminating resins, paper resins and surface coatings.
Household: Dinner wares, cutlery handles, large serving utensils, bowls, trays, dispensers, ash trays, buttons, soap dispensers, vertical wall surfaces, furniture, bathroom wash basins, toilet seats, shower housings, door knobs, appliance components, coffee makers and flooring seats.
Electrical: Electrical parts, switch gears, welding rod holders, terminal strips, watt meter blocks, connector plug inserts, electrical panels & parts and printed circuit boards.
Miscellaneous: Boat hulls, powder bowls, school desk tops and flame boards.
Urea Formaldehyde
Electrical: Wiring devices, circuit breakers, wall plates, electric blanket control housings, plugs, sockets, holders and bed switches.
Miscellaneous: Closures, receptacles, toothpaste tube inserts, buttons, toilet seats, knobs, adhesives & bonding agents, flooring, furniture, binders for foundry cores, coated abrasive papers, foams, orthopedic casts and bandages.
Appliances: Hair dryers, food mixers, coffee percolators, table mats, telephone sets and cookware handles.
3. Epoxy Resins
Chemically, the term "epoxy" means a three membered ring containing one oxygen and two carbon atoms.
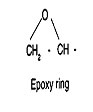
The molecules of 'epoxy resins are low in molecular weight and when cured they are joined together to form large cross linked structures. These final products are thermosets. Epoxy resins were first developed in 1930s in Germany. But the material was commercialised in 1946. Epoxy resins are manufactured by reacting polyhydric alcohols with epichlorohydrin. The largest produced epoxy resin called Diglycidyl Ether of Bisphenol-A (DGEBA) is produced by reacting bisphenol-A with epichlorohydrin.
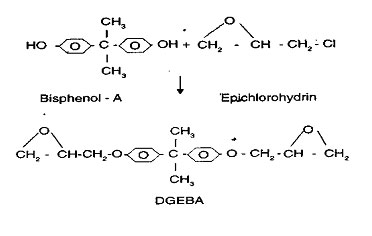
Epoxy resins are cured with different curing agents like amines, amides, acids, acid anhydrides and amine aducts. Also, they are catalytically cured using tertiary amines. By selecting a suitable resin and a curing agent we can get a range of properties for different applications.
Characteristics
- Good mechanical strength and dimensional stability
- Good heat and chemical resistance
- High dielectric strength
- High strength and modulus
- High volume resistivity
- Good wear resistance
- Excellent adhesion to wide range of materials
- Excellent weatherability
- High temperature resistance
- Good Hardness, toughness and rigidity
- Excellent corrosion resistance
- Low curing shrinkage
- Resistant to solvents
- High heat distortion temperature
- Low dissipation factor
- Outstanding arc and tracking resistance
- Flame retardant
- Resins are highly viscous
- Low potlife and shelf life
- Poor oxidative stability
- High cost
- Susceptible to U V radiation
Properties |
Values of DGEBA |
[/td Colspan=3 align=center]Cured with |
|
Aliphatic polyamines |
Aromatic polyamines |
Polyamides |
Tensile strength, MPa |
40-70 |
83 |
35-55 |
Flexural strength, MPa |
104-124 |
152 |
48-62 |
Compressive strength, MPa |
138-227 |
207 |
62-76 |
Dielectric constant at 50 Hz and 25°C |
4-5 |
4-5 |
3.2-3.6 |
Volume resistivity at 25°C, Ohm.cm |
1016 |
1016 |
1016 |
Some of the commercially Important epoxy grades are:
- Diglycidyl ether of bisphenol-A resins
- Epoxy - Novolac resins
- Cycloaliphatic epoxies
- Halogenated resins
- Flexibilising diepoxides.
Epoxy resins can be processed by the following techniques:
- Hand lay up and spray up techniques
- Casting
- Filament winding
- Pultrusion
- Impregnation and
- Lamination
Applications
Adhesives: Metal to metal, non metallic surfaces, binders for industrial, seamless thin-set terrace flooring, concrete repair, ground water proofing membranes, decorative walls, light metal window & door frames, metal letter boxes, sheet metal laminates, pipe and hose coupling.
Automotive: Doors, seats, luggage carriers, wall linings for railway coaches, buses & ships, defrosting equipment for aircraft, fuel tanks, partition walls and body parts.
Casting: Battery casings, centrifugal pumps, pipes for liquids, flange coupling, closings, lab equipments and dye baths.
Electrical/Electronics: Low current applications, telephone & high frequency applications, x-ray apparatus electrical measuring instruments, transformers, rotors, circuit breakers, cable closing sleeves, cable and stoppers, inserts for switches, slot keys and encapsulation of pace makers.
Household: Coatings for drums, cans, washing machines and refrigerators, floors and repair kits.
Industrial: Lamination for drill jigs, router jigs, cutting, wrapping & welding fixtures, model core boxes, casings, coatings for metal sheet industry, machinery, containers pipes exposed to highly corrosive environments, chemical resistant pumps, pipes and impellers.
Roads and Highways: Test strips, sealing membranes, high friction surfaces, cast traffic reflectors, bonding new concrete to old concrete, reflection strips and traffic bars.
Sports: Skis, high jump poles, fishing rods, hockey sticks and drum sticks
Miscellaneous: Pottery moulds, press and vacuum forming tools, core boxes, moulds for RIM, laminates for aircraft and automobile components, laboratory bench tops, floorings, road surfacing, radiator supporters and transmission supporters.
4. Unsaturated Polyester Resins
Unsaturated polyesters are very versatile materials. They can be rigid, resilent, flexible, corrosion resistant and weather resistant. These resins were first synthesised in the year 1936 by Carleton Ellis and commercialised in 1941.
Unsaturated polyesters are usually manufactured by batch process. They are the condensation products of unsaturated dibasic acids (usually maleic anhydride), saturated dibasic acids and glycols. The glycols used may be ethylene glycol, propylene glycol or diethylene glycol. Important saturated acids used are phthalic anhydride and m-phthalic acid. The most common cross linking monomer used is styrene but vinyl toluene, methyl methacrylate and diallyl phthalate can also be used. Structure of Isophthalic acid polyester resin is given below:
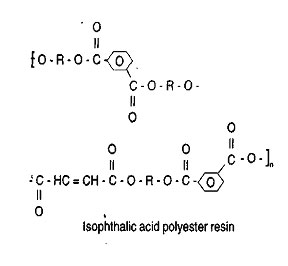
Characteristics
- Can be made rigid, resistant, soft or flexible
- Can be made flame retardant, weather resistant and corrosion resistant
- Cured resins are rigid and do not flow on heating
- Resistant to yellowing on exposure to UV light
- Attacked by alkalies
- Good resistance to burning and ignition
- Good heat resistance
- High stiffness and impact strength
- Low tooling costs
- Poor abrasion resistance
- Weak solvent resistance
- Poor fatique resistance for flexible cast polyester resins
- Laminates, SMCs and DMCs are very good in strength
Typical values of polyester hand lay up laminates
Manufacturers/suppliers |
Trade Names |
Allied Chem |
Epiall, Plaskon |
Union Carbide |
Bakelite |
Dowchem |
DEN; DER |
Epoxylite |
Epoxylite |
Fiberite |
Fiberite |
General Electric |
Arnox |
Shell |
Epikote |
Bayer |
Lekutherm |
Tufnol |
Tufnol |
SIP Resins |
Epoxite |
Ciba-Geigy India Ltd. |
Araldite |
Unsaturated Polyester resins are available in the following grades:
- General purpose grade
- Flexible grade
- Low shrinkage grade
- Weather resistant grade
- Chemical resistant grade
- Fire resistant grade
- Filled grade
Unsaturated polyesters can be processed by the following techniques:
- Hand lay up and spray up techniques
- Preform moulding
- Centrifugal casting
- Pultrusion and filament winding
- Matched metal die moulding
- Injection moulding and
- Compression moulding for SMCs and DMCs
Properties | Values |
Tensile strength, MPa |
8 - 17 |
Flexural strength, MPa |
10 - 20 |
Flexural modulus, MPa |
3440 |
Power factor 106Hz |
0.02 - 0.08 |
Dielectric constant 106Hz |
3.2 - 4.5 |
Water absorption, % |
0.2 - 0.8 |
Manufacturers/Suppliers | Trade Names |
Armco |
Armco |
BASF |
Palatal |
BIP |
Beetle |
Bayer |
Legural |
Freeman chemicals |
Freflow, Flomat |
Good year |
Vituf |
ICI |
Melinex, Atlac |
Rohm & Haas |
Peraplex |
Shell |
Epocryl |
Applications
Building & Construction: Building panels, cultured marbles, beams, water tanks, skylights, outdoor structural panels, fume hoods, play ground equipments, room dividers, roofing, siding, tanks, pipes and corrugated paneling.
Automotive: Automobile structural parts, auto body putty, aircrafts, safety helmets, guards, gelcoats, automobile springs, truck cabs, truck feners, recreational vehicles, automobile exterior parts and auto patching compounds.
Electrical/Electronic: Switch gear parts, fuse holders, street light housings and electrical components.
Household: Bathtubs, laundry tubs, septic tanks, trays, shower stalls, picture frames, appliances, buttons, furniture and tool boxes.
Industrial: Reaction vessels, tanks, large diameter pipes, mine bolts and castings.
Sports: Golf club shafts, archery bows, bowling balls and swimming pools.
Miscellaneous: Fishing rods, train interior components, boats, flag poles, glass fibre reinforced cycle parts and park benches.
5. Polyurethane
Polyurethanes are a wide variety of polymers with quite different compositions and correspondingly different properties. The characteristic structural element of almost all of these polymers is the urethane group formed in the course of polyaddition. In 1937, Otto Bayer and co-workers discovered the diisocynates addition polymerization that resulted in the preparation of many different types of polyurethanes. Although such polymers can be formed by a number of different chemistries, the most common method is by the reaction of a polyisocyanate with an organic polyhydroxy material (Polyol).
Polyurethanes are the most important class of polymers playing a vital role in many industries from ship building to footwear; construction of cars. They appear in an astonishing variety of forms. The various types of unsaturated polyurethanes are foams (Low density flexible foams, low density rigid foams, high density rigid foams), solid polyurethanes, adhesive, binders, coatings and paints. Plastics as such are harmless and environmental friendly. Among the various waste management options, plastics recycling is more ecofriendly and energy saving. Mechanical recycling is widely adopted in India ever since the manufacturing of plastic raw materials. Due to economic reasons recycled plastic materials find various applications from small gem clips to large pallets.
In general, polyurethanes are addition polymers manufactured by the reaction of di-or poly-isocyanates with polyols.
The reaction is exothermic. The rate of the polymeriation reaction depends upon isocyanate and the polyol.
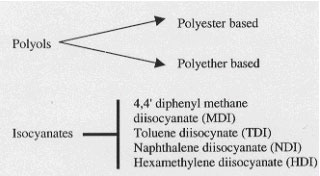
In addition to isocyanates and polyols a wide range of chemicals may be added to control and modify both the polyurethane reaction and the properties of the final polymer. They include:
- Catalyst
- Chain extenders
- Crosslinking agents
- Surface active materials
- Flame retardants
- Colourants and
- Fillers
Characteristics
Polyurethanes have found wide application in virtually every industry because of their characteristic general properties, the most important of which are :
- High elasticity over the entire hardness range
- Flexibility over a wide temperature range
- Good weather resistance
- Good resistance to oil, grease and many solvents
- Excellent wear resistance
- High Young's modulus compared with rubbers of a similar hardness
- Performance above its Tg
- Ability to stretch and retract instantly
- Negligible crystallinity
- Change in length in response to constant stress at variable temperatures
Properties | Values |
Tensile strength, Psi |
10,000 - 11,000 |
Elongation, % |
3 - 6 |
Flexural yield strength, Psi |
19,000 |
Hardness, Rockwell |
30-35 |
Flexural elastic modulus, Psi x 106 |
6.1 |
Heat deflection temperature, °F |
190-200 |
Dielectric constant, 60 cyc |
3.4 - 3.5 |
Dissipation factor |
0.008 |
Themoset polyurethanes are available in the following grades:
- Foam grade
- Elastomer grade
- Coating grade
Themoset polyurethanes can be processed by the following techniques:
- Casting
- Reaction injection moulding (RIM)
- Reinforced reaction injection moulding (RRIM)
- Foam moulding
Manufacturers / Suppliers | Trade Names |
Stainffer Chemical Co. |
Everlon |
Accessible Products Co. |
Acoustzip |
Freeman Chemical Corporation |
Chempol |
American Cyanamide Co. |
Adaphah |
Urethane Products Canada Ltd. |
Flexi-cast |
Eagle picher Industries, Inc. |
Chem-Thane |
N.L. Industries, Inc. |
Alfa |
Upjohn Co. |
Castethane |
Arveta, S.A. |
Avetone |
Mobay Chemical Corporation |
Desmocoll |
Bee Chemical Co |
Beethane |
PPG Industries |
Durathane |
North American Urethanes, Inc. |
Elastolur |
Pan Chemical Corporation |
Fawthane |
Texaco Inc. |
J. Thane |
Applications
Construction: Wall panels and roof tops, wall insulation, insulation of pipes and tanks, foam in place fox holes, soft hammers, pump housing, linings, friction drives and belts, pipe seals, spray protective layers and sealants.
Sports: Shoe heels & soles, handles for tennis rackets & golf clubs, golf balls, foot ball studs and shock-absorbing pads.
Automotive: Seating, interior padding, exterior body panels, complex soft front ends, components mounted in the engine space and accessories, cast tires, suspension systems, spring matting, bumpers, fenders, cushion and steering wheels.
Furniture: Cushion, mattresses, refrigeration insulation, refrigerated trucks and trailers insulation.
Miscellaneous: Engine parts & electronic tubes packaging, radios, wing tips in aircraft, fuselage insulation, blood oxygenator equipment, adhesive, coating metals, gaskets, bushings and switches.
6. Silicones
Silicones may be defined as synthetic compounds containing alternating silicon-oxygen backbone. This inorganic backbone is chemically modified with pendant organic groups to add flexibility and reactivity. Modern developments in silicone chemistry have sprung from Kipping's researches.
Silicon is manufactured by the reduction of silicon dioxide in electric furnaces. The elemental silicon is reacted with gaseous methyl chloride in the presence of copper catalyst to provide methyl chlorosilanes which are fractionated and the resultant dichlorodimethyl silane is hydrolysed with water to form linear and cyclic poly siloxanes.

Polyorganosiloxanes are normally referred to as 'silicones' and are polymeric substances with the structure given above. A wide variety of silicone resins are available commercially. The properties of the individual types differ somewhat depending upon the use for which they are designed. Silicones form the basis of a wide range of industrial products which may commercially be classified as fluids, resins and elastomers or rubbers.
Silicone forms
Silicone Fluids
A large number of silicone fluids have been synthesised and studied. Dimethyl silicone fluids and other silicone fluids belong to this category.
Silicone Resins
They are highly branched polymers that cure to solids
.
Silicone Elastomers
These are based on linear polymers of very high molecular weight which are analogous to the silicone fluids. Mechanical strength is imparted by the addition of suitable inorganic fillers and elastic properties are obtained as a result of intermolecular cross linking in the presence of an oxidising curing agent.
Silicone elastomers are manufactured in several forms: heat-cured rubber, liquid injection moulding elastomers, one-component room temperature vulcanizing sealants (RTV), two component RTV products and speciality fluorosilicones.
Characteristics
Silicone fluids
- Transparent to visible light and UV radiation
- Low pour point
- High temperature stability
- High compressibility
- General inertness
- Relatively constant viscosity over temperature
- Unstable towards concentrated mineral acids
Silicone Resins
- They resemble glass but are somewhat softer and usually soluble in solvent until cured.
- Degree of hardness depends on the extent of cross linking
- Very good heat resistance
- Highly water-repellant
- The resins are good electrical insulators particularly at elevated temperatures and under, damp conditions.
- Have good resistance to most aqueous chemical reagents
- Good inherent weatherability
- Resistance to many organic solvents is poor
Silicone Elastomers
- Degree of hardness depends on the extent of cross linking
- Good resistance to most aqueous chemical reagents
- General inertness
[tsble] PropertiesValues Silicone fluids (Dimethyl Siloxane 100 mol %) Viscosity at 25°C, mm /s10 Pour point, °C-73 Flash point, °C210 Thermal conductivity at 65°C,w/m K1.3 Electrical strength, KV/mm1.4 Electric constant2.6
Properties | Values |
Silicone impregnating resins |
|
Wt. loss after 3 hrs. at 250°C, % |
4 |
Power factor at 25°C at 100 Hz |
0.0084 |
Dielectric constant at 25°C at 100 Hz |
3.0 |
Properties | Values |
General purpose silicone rubbers |
|
Tensile strength, 1 bf/in |
500-1000 |
Hardness |
40-50 |
Useful temp., °C |
-55-250 |
Linear shrinkage, % |
2-6 |
Power factor, 60 Hz |
0.002 |
Dielectric constant, 60 Hz |
3-6 |
Silicones are available in the following grades:
- Resin grade
- Elastomer grade
- Rubber grade
- Fluid grade
Manufacturers/suppliers | Trade Names |
Wacker -Chemie |
Wacker, Elastosil |
Union Carbide Corpn. |
Bakelite |
Mobay Chemicals Co. |
Baysilone |
Dow corning Corpn. |
Dow corning, Sylgard |
Genera, Electric Co. |
G.E. |
Crucible Chemical Co., Inc. |
Cru-Rez |
Custom Materials, Inc. |
Custom - Load |
Rhodia, Inc; May & Baker Ltd. |
Rhodorsil |
SWS Silicones, Inc. |
Silgan |
Textron Inc. |
Spenkel |
Thiokol Corporation |
Spraythane |
Thuscon laboratories |
Super-Porseal |
Applications
Silicone fluids
They are used in vinyl polishes and high temperature greases. Their most important application in relation to the plastics industry is as mould release agents. They are used as additives in polishes and waxes, heat-transfer fluids, electrical transformer fluids, textile fibre lubricants, antifoaming agents in chemical processes & carriers and softness in cosmetics.
(b) Silicone Resins
Silicone resins are employed in a wide and increasing range of industrial applications. These include surface coatings, high temperature paint additives, electrical moulding compounds, masonry water repellants, abrasion resistant coatings for plastics, tackifiers for silicon adhesives and for electrical applications.
Abrasion resistant silicone coatings are used to protect transparent plastics against scratches, chemical attack and UV degradation. Silicone is widely used as the release coating on plastic film label stock.
The use of silicone resins in paints and other surface coatings depend on their heat resistance, water repellency and resistance to chemical reagents. A blend of silicone and organic resins pigmented with aluminium powder is used in applications such as coatings for metal chimneys, exhaust pipes and furnace doors involving exposure to temperatures upto 500°C.
Silicone resins form useful release agents and although more expensive initially are more durable. To release confectioneries from baking pans, these resins are used.
Silicone laminates are used in electrical applications such as slot wedges in electric motors, terminal boards, printed circuit boards and transformers.
Silicone Elastomers
Made into parts like valve cover, oil pan gaskets, device axle boots, o-rings, diving masks, medical catheters, hose, tubing, wire and cable, sponge & profile, tiny and complex parts, electrical connectors and baby bottle nipples. Adhesives, sealants and many industrial grades are used for glazing and for gaskets.