INK FORMULATIONS
(A) LETTERPRESS INK
Letterpress inks will be formulated to be as versatile as possible, to run on a number of types of presses and substrates. Examples are given of a range of ink formulations suitable for the conditions stated, which can be modified to suit the other requirements of local conditions.
Platen ink for absorbent papers
Much of the work carried out on plated presses can involve absorbant papers and requires a quick turn around. An ink which penetrates the paper but remains open on the press is therefore advantageous and can be formulated on similar lines to a flat-bed newspaper ink, with higher viscosity and shorter flow :
Carbon Black (Ci Pigment Black 7) |
19.0 |
Reflex Blue |
2.0 |
70 poise mineral oil |
55.0 |
0.5 poise mineral oil |
9.0 |
15 poise bodied linseed oil |
10.0 |
Asphaltum solution |
5.0 |
|
100.0 |
Cylinder press ink for uncoated papers
An ink formulated for a more general range of uncoated papers will require to have some drying properties. The incorporation of some resin giving the ink a degree of tack and flow, and the addition of slightly more blue toner can also be expected :
Carbon Black (CI Pigment Black 7) |
18.0 |
Reflex Blue |
4.0 |
Long oil alkyd |
16.0 |
0.5 poise mineral oil |
5.0 |
Varnish |
55.5 |
10% Cobalt drier |
0.5 |
Antioxidant |
1.0 |
|
100.0 |
a consists of a hydrocarbon resin or modified phenolic resin cooked into a blend of linseed and mineral oils.
Quick-set inks for coated paper
This type of ink will usually be based on a varnish formulated from resin, drying oil and distillates as described in the section dealing with resins. The choice of resin and ratio of resin/oil blend to distillates are determined by the quality of the substrate and the properties required from the final print.
The higher the absorbency of the substrated, the higher the viscosity of the resin/oil phase needs to be, in order that chalking of the print does not occur :
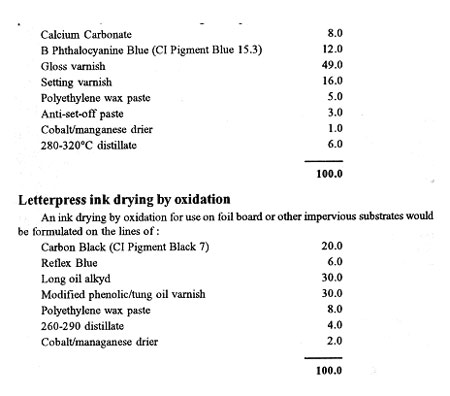
The small percentage of distllate shown can be tolerated, but higher amounts would tend to be trapped in the ink film and make it easier to remove from the surface.
Water-reducible inks
For letterpress printing on corrugate boxes, a typical formula would be :
Water-reducible red
Blance Fixe (CI Pigment White 21) |
10.0 |
Rutile Titanium White (CI Pigment white 6) |
5.0 |
Lake Red C |
14.0 |
Varnish |
54.0 |
Diethylene glycol |
8.0 |
Wax paste |
5.0 |
Amine |
4.0 |
|
100.0 |
Varnish
High acid value |
|
Maleic resin |
50.0 |
Glycol |
40.0 |
Amine |
10.0 |
|
100.0 |
The printing involved will mainly consist of solids, type and linework and the print usually has a semi-matt appearance. On this type of substrate, two colours can usually be superimposed, wet-on-wet without tack grading, but on more solids boards, tack adjustments with mixtures of water and glycols with be required. A low viscosity ink aids distribution on the rollers and the transfer properties from the rubber stereo to the kraft paper.
Process inks
The use of the letterpress process is now hardly known in the UK for this purpose and BS 4160 : 1967 (European Reference CEI 12/66) has recently been made 'obsolescent' by the BSI. This standard specified the colour, colour strength, transparency, lightfastness and solvent resistance of the three primary colours - yellow, magenta and cyan. It also referred to a previous British Standard for letterpress process inks (BS 3020: 1959) for a suitable black ink.
Process magenta letterpress |
|
Calcium 4B toner (CI Pigment Red 57.2) |
15.0 |
Polyethylene wax paste |
3.0 |
Cooked quick-set vehiclea |
32.5 |
Gloss quick-set vehicleb |
28.0 |
Cobalt/manganese Drier |
0.5 |
280-320°C distillate |
20.0 |
Antioxidant |
1.0 |
|
100.0 |
aBased on modified phenolic resin, cooked into a long oil alkyd and linseed oil and let down in 280=320°C distillate.
bBased on modified phenolic resin, cooked into a long oil alkyd, let down with 280-320°C distillate and aluminium gelled.
Similar formulations for the yellow and cyan would contain 15% Diarylide Yellow (CI Pigment Yellow 13) and 14% B Phthalocyanine Blue (CI Pigment Blue 15.3) respectively, to give the correct chromacity figures when printed in accordance with the standard, Because of the thicker ink films laid down, tack grading is essential < when printing two colours wet-on-wet.[/P]
Newspaper coloured inks
The titles and late news items are sometimes printed on very small units which have very limited rolling capacity. Due to the high operational speed of these units, considerable ink spray can be developed. Coloured inks are also widely used in provincial papers to give impact to advertising. These are usually printed on page wide units which present the formulator with similar problems to that of the seal or headliner colours. Occasionally, if the amount of coverage of colour warrants, a complete unit will be used, but more usually, half-deck, and the careful design of the page layout will provide the necessary colour.
A typical formulation would be :
Chlorinated Para Red (CI Pigment Red 4) |
10.0 |
Extender pigment |
10.0 |
Resin varnish |
40.0 |
Mineral oils |
25.0 |
Long oil length alkyd resin |
10.0 |
Wetting agent Antioxidants, etc. |
5.0 |
|
100.0 |
aA hydrocarbon resin or low melting point phenolic resin dissolved in mineral oil.
The amount of pigment/extender is varied depending on the properties of colour strength, etc. That are required and the ratio of resins, solvents and oils adjusted to suit the individual units being used.
Rotary black inks for newspapers
The formulations used for printing newspapers have to meet the following targets which require good tolerance for troublefree running :
- Low misting character;
- Non-drying on press, but reasonable rub resistance on paper;
- Easy deliver to the press;
- Good transfer to the substrate;
- Low linting character;
- No adverse effect on stereos used;
- Good penetration on newsprint but a minimum of strike through during the normal life of the paper.
- Good de-inking properties;
- Economical to use.
The colour strength is critical in formulating newspaper inks. If the ink is over-strength, reduced film weights are used, and this may give rise to poor coverage and uneven inking. Problems of linting and transfer may also occure if an insufficient volume of ink is being replaced on the forme and ink distribution roller chain. Conversely, with low-strength ink, problems of strike through, misting, flooding the stereo and marking off on path rollers occur, as high volumes of ink are transferred through the printing system to obtain the correct density.
The actual amounts of ink used per copy vary with the content of the edition and the absorption of the newsprint used. A guide to how much ink is used is : 1.7 g of rotary news ink per 1000 copies of a 32-page tabloid. (This is based on experience rather than a calculated formula). While the amount of ink used per copy is extremely small, the total amount of ink used by a newspaper publisher can be over 3000 tonnes per annum. The cost of the ink is therefore a significant factor in newspaper production costs, and can be a limiting factor which has to be taken into account by the formulator, restricting the use of certain raw materials.
A further economic factor to be taken into account is the need to include a proportion of reclaimed material in the newsprint paper manufacturing process. Before this happens, the printed paper must be deinked to maintain the final prightness of colour of the newsprint. The de-inking process consists of treating the paper with alkali to reduce the paper to fibre form allowing the ink to separate and float to reduce the paper to fibre form allowing the ink to separate and float to the surface from where it is removed. The paper slurry is then neutralized and included in the fresh paper-making cycle.
While this process is reasonable easy with conventional rotary letter-press inks, harder drying formulations can prove more difficult to separate.
The formulations in Table 5.2 show the type of variations in formulae used to obtain the correct properties for various presses, plates and papers. They must only be regarded as starting formulations to give the technologist guidance. Individual printers require inks with properties specific to their needs, and each type of manufacturing plant will produce inks of slightly differing properties using the same materials. The formulations have been chosen to give similar print performance under the various conditions used.
Formula A : General-purpose low mist black
This ink is capable of running at very high speed (50,000 cps) on a variety of presses and newsprints. It has a blend of mineral oils and flow acids which will give good density with other good print qualities of strike through, and non-marking on the turner bars of the press. The anti-spray additives are added to give the ink low mist and ink sling properties.
Formula B : Ink rail
A differing blend of mineral oils and flow aids to give excellent print qualities to an ink which is thinner and longer flowing than Formula A. This is necessary to allow the ink to freely circulate on the ink rail distribution system.
Formula C : Page-pak
This formulation has longer flow and is thinner than both the previous formulations because of the restrictions in the page-pak distributing systems.
Formula D : Keyless inking (indirect flexo)
The formulations of news inks for this type of ink metering system are similar to those for conventional units. The viscosity of the ink needs to be low enough to fill the cells of the etched roller and flow sufficient for the inks to be readily pumped. The level of pigmentation is dertermined by the depth and shape of the cells of the etched roller.
Formula E : Flat-bed rotary
The flat-bed rotary formulation included in Table 5.2 would normally by supplied in tins or buckets for use on the slower flat-bed and rotary presses. The relatively low ink usage and the position of the ducts is such that the ink is normally transferred to the duct manually using a palette knife. This type of ink is commonly referred to as 'knifeable'. The slow press speeds involved also required inks of a higher viscosity and shorter flow than previous formulations and the inclusion of anti-spray additives is not normally required.
The amount of Carbon black in the formulation needs to be increased compared with high speed rotary presses in order to achieve similar print densities due to the different transfer properties of these inks.
Formula F
The formulation has been included to show that rub resistance of conventional news inks can be improved by the incorporation of an amount of varnish. This varnish usually consists of hard resin, typically hydrocarbon resin, mineral oil and distillate.
(B) LITHOGRAPHIC INKS
TYPICAL INKS AND VARNISHES
The details of litho ink and varnish formulation are dependent on the conditions under which the products are to be printed and the end-use requirements of the print. The major distinctions are between sheet-fed and web-fed printing and between the main classes of substrate, namely low-quality papers, high-quality papers, carbon boards and impervious substrate. Specific formulations are also usually employed for the small offset presses found in instant print shops and in-plant printing departments.
Inks and varnishes for sheet-fed paper printing
The quick set mechanism is the standard drying process employed in the sheet-fed offset printing of paper substrates. The formulating approach shown below is used to produce process colours, blacks, colour blending system inks and specially matched individual spot colours :
Organic pigmenta |
18.0 |
Cooked quickset vehicleb |
|
Gloss quickset vehiclec |
70.0e |
Fast quickset vehicled PE wax paste |
5.0 |
Anti-set-off paste |
3.0 |
Cobalt/manganese driers |
1.0 |
280-320°C distillate |
3.0 |
|
100.0 |
- For example, CI Pigment Blue 15 : 3, for a process cyan.
- Based on low solubility modified rosin ester cooked into linseed oil and let down in 280-320°C distillate.
- Based on high solubility, low melting point modified rosin ester and long-oil alkyd, aluminium gelled.
- Based on soluble modified rosin ester, used at high resin-to-oil ration.
- The exact proportions of the various vehicles will depend on the desired balance of gloss, setting and machine performance.
Black inks of the highest density require the incorporation of specific wetting vehicles, generally based on low viscosity resins and alkyds to give high solids in the vehicle at moderate viscosity. This enables the vehicle to wet fully the substantial surface area associated with high loadings of fine particle size carbon blacks.
Good pigment wetting is essential for satisfactory in rheology, particularly flow and transference, to the promotion of gloss and a true black jetness.
Quickset overprint varnishes for sheet-fed lithographic application to paper substrates are based on rather different formulations to anything usually encountered in vehicles for inks. A typical varnish would consist of the following :
Maleic modified rosin ester (pale colour) |
30.0 |
Tung oil |
15.0 |
Long-oil alkyd |
15.0 |
PE wax paste |
7.5 |
Cobalt driers |
2.5 |
260-290°C distillate |
30.0 |
|
100.0 |
The pale colour of the resin is necessary to minimise yellowing on top of non-ink-image are as and to avoid shade distortion of underlying colours. Tung oil is introduced to give a tough dry film for maximum rub and scuff resistance. As setting of overprint varnishes is often partially restricted by the ink films already present. Oxidation drying is speeded by the use of high drier contents, and solvent separation is encouraged by the use of more mobile and slightly more volatile, lower boiling range distillate fractions. These latter generally give acceptable roller stability since the throughput of varnish on the press is usually high due to the relatively high film weights and coverage which are commonly applied.
Specific ink formulating approaches are utilised where there are particular substrate requirements, such as with label papers, or particular pigment characteristics, as in metallic inks, or where there is a distinct variation in the characteristics of the printing process, e.g. small-offset.
Sheet-fed label inks
Plain paper labels for the can, jar and bottle industries are generally printed on large format sheet-fed machines with single sheet carrying many individual labels. The substrates used are normally low in base weight and coated on the front side only. Large sheet size, high ink coverage (in order to meet the visual impact demands placed on labels) and lightweight paper produce severe sheet curl problems unless specially formulated low tack inks are used. Adequate viscosity is preserved in such inks by the use of gelled vehicles and gelled reducer. A typical formulation would be :
Permanent Orange (CI Pigment Orange 13) |
20.0 |
Cooked quickset vehiclea |
60.0c |
Gelled quickset vehicleb Long-oil alkyd |
5.0 |
Long Oil alkyd Anti-set-off paste |
3.0 |
Gelled reducer |
3.0 |
Cobalt/manganese driers |
2.0 |
PE wax paste |
7.0 |
|
100.0 |
- Based on low solubility modified rosin ester cooked into linseed oil and let down in 280-320° distillate.
- Based on soluble modified rosin ester. Aluminium chelate gelled.
- The ratio of the two vehicles depends on the exact viscosity/tack relationship required.
Metallic inks
Gold and silver inks are based on bronze and aluminium linings respectively. These linings are powders of a specific physical from which consist of extremely small, flat particles. In order to achieve a satisfactory metallic luster at the low film weights printed by offset lithography, very high loadings of the finest particle size grades are utilised. Even then, optimum brilliance and luster can only result if the particles are able to 'leaf' in the ink vehicle, i.e. orientate themselves such that the flat surfaces are overlapping and parallel to the substrate surface. Care is required in formulating metallic litho inks in order to ensure that the vehicle both permits leafing and retains adequate tack and rheology characteristics when very high proportions of the metal linings are also major considerations because reactions can take place between the metal powder and ink vehicle components. A typical formulation of an offset litho gold suitable for sheet-fed printing on to paper and board would be :
Bronze lining pastea |
50.0 |
Metallic quickset vehicleb |
41.5 |
Cobalt driers |
1.0 |
PE wax paste |
7.5 |
|
100.0 |
- Approximately 85-90% bronze lining in low sulphur content distillate. (The latter is important to avoid tarnishing.
- Based on soluble modified rosin ester resin and long-oil alkyd in low sulphur contents distillate. Stabiliser is incorporated into the vehicle for single-pack gold production.
Silver inks stilise a lower lining content than golds, due to the lower specific gravity and superior luster and opacity of aluminium linings. A typical level of incorporation would be 20%. Also, stabilizer is not usually required in single-pack silver inks since aluminium linings are inherently less reactive with oleoresinous vehicles that bronze powders.
In order to preserve the leaf line potential of the linings, all metallic inks must be manufactured by processes involving low shear only. Thus, slow mixing and blending are appropriate but high speed stirring and three roll milling are not.
Small-offset
The presses used in small-offset are designed for ease of operation, since they are often run be staff who are not fully trained litho printers, and for economic construction, in order to provide a low-cost facility for the duplication of type matter. Inking and dampening systems are frequently rather different from those employed on larger, sheet-fed presses and are often extensively integrated. The ink distribution system is restricted in rolling power. Additionally, a wide range of plates is used, extending down to very low cost grades which rely on a tough paper as the base support material. Such plates may have only limited distinction between image and non-image areas.
These factors impose a unique set of requirements on the physical and chemical characteristics of small-offset ins. Primarily, the inks must show good distribution and transference, controlled emulsification even on inteqrally damped presses with their associated founts (which may contain gloycols or glycerol), and high cohesion in order to prevent ink transfer to poorly protected non-image areas. The inks are usually required to remain non-skinning over extended periods because the presses are not routinely washed up, even at the end of the day of week, particularly where they are only utilized for printing black. This does not pose too many drying problems when the inks can be formulated to dry be penetration into uncoated paper stocks. Here rubber resin based inks can be used as well as inks based on oxidation drying vehicles with appropriately high additions of anti-oxidant. Where the role of small-offset presses is extended to include the printing of coated papers, oxidation drying systems with a very careful blance of driers and antioxidants must be utilized, usually to give extended non-skinning with relatively slow drying.
Typical formulations for oil-based and rubber-based small-offset blacks are as follows :
Carbon Black (CI Pigment Blaqck 7) |
20.0 |
Reflex Blue (CI Pigment Blue 18) |
2.0 |
Oxidation drying vehiclea |
70.0 |
Anti-oxidant pasteb |
2.0 |
Alkali-refined linseed oil |
6.0 |
|
100.0 |
- Based on modified rosin ester in linseed oil.
- Butylated hydroxy toluene inoleoresinour vehicle.
Carbon Blak (CI Pigment Blue 7) |
20.0 |
Reflex Blue (CI Pigment Blue 18) |
2.0 |
Microised talca |
10.0 |
Cyclised rubber vehicleb |
65.0 |
280-320°C distillate |
3.0 |
|
100.0 |
- Incoroorated to control the severe flying tendency of cyclised rubber based system.
- Cyclised rubber resin dissolved inrelatively high aromatic content distillate, at low resin solids.
Inks and varnishes for sheet-fed carbon board printing
A significant proportion of sheet-fed offset carton printing is now carried out using UV curing systems. This subsection will consider those formulations for board substrates which dry by the quickset mechanism. Although inks and varnishes produced for paper printing can be applied to board stocks, optimum performance to meet the stringent and unique demands of the folding carton packaging industry is usually achieved with specialized formulations. The major requirements are :
- Hard drying with maximum scuff resistance in order to avoid markingon filling, distribution or retail of the packaged goods.
- Very rapid setting to minimize set-problems and the needs for anti-set-off spray, aggravated by the substrate weight and its rapid development of pressure in the stack.
- Minimum odour and minimum tendency to impart off-flavours (taint) when used for food and confectionery packaging.
- Suitability of subsequent varnishing or lamination in relevant instance. (Note : It this requirements also applied to sheet-fed paper jobs, formulations similar to that outlined below can be used).
Maximum scuff resistance is achieved in inks typified by the following :
Naphthol Red (CI Pigment Red 2)a |
20.0 |
Cooked quickset Vehicleb |
50.0 |
Hard-drying vehiclec |
20.0 |
Micronised PE wax |
2.0 |
Micronised PTEF wax |
1.0 |
280-320°C distillate |
5.0 |
Cobalt/manganese driers |
2.0 |
|
100 |
- Resistant red pigment for soap and detergent carton requirements.
- Based on low solubility modified rosin ester cooked into linseed oil and let down in 280-320°C distillate.
- Distillate-free oxidation drying vehicle based on modified rosin ester in tung and linseed oils. This type of ink is relatively slow setting particularly if the content of hard oxidation drying vehicle is further increased to meet particular rub resistance demands. Consequently, substantial use of a relatively coarse spray powder is normally necessary to avoid set-off. Where a less hard drying ink can be tolerated, substantial advantages in setting can be achieved by using a formuation as below, which is also appropriate as the basis for low odour and tain or varnishable requirements :
Rubine 4B (Ba salt) (CI Pigment Red 57 : 1) |
20.0 |
Low odour quickset vehiclea |
55.0 |
Hard drying quickset vehicleb |
15.0 |
Micronised PE waxc |
2.0 |
Micronised PTFE waxd |
1.0 |
Low aromatics 280-320°C distillate |
6.0 |
Cobalt/manganese driers |
1.0 |
|
100.0 |
- Based on soluble modified rosin ester and soluble low odour modified hydrocarbon resin in long-oil soya modified alkyd and low aromatics distillate.
- Oxidation drying vehicle. This eliminated where minimum odour characteristics are demanded.
- PE wax content is reduced in inks for subsequent varnishing or lamination.
- PTEF was is eliminated in inks for subsequent varnishing or lamination.
The key to success in this approach is very careful formulation of the low odour quickset vehicle. Resins must be chosen that have inherently low odour and good solubility in low aromatic distillates.
Overpring varnishes for sheet-fed lithographic application to food and confectionery packaging have to be formulated with due consideration for both these odour and taint factors and the colour and drying aspects described earlier.
Maleic modified rosin ester (pale colour) |
30.0 |
Long-oil soya alkyd |
25.0 |
PE wax paste |
7.5 |
Cobalt driers |
2.5 |
Low aromatics 260-290°C distillate |
35.0 |
|
100.0 |
Ink for sheet-fed impervious substrate printing
Offset lithography is heavily orientate towards the printing of paper and board substrates which posses a significant degree of absorbency. This enables penetration and setting to play major roles in drying and adhesion in most sheet-fed work. However, a range of foil and plastic stocks are printed lithographically either wit oxidation drying of UV curing formulation.
Oxidation drying inks for impervious substrates represent a difficult compromise between press stability and hard drying. They must be nonskinning in the duct and on rollers, plate and blanket, but free from set off and must give good key and adhesion to the substrate. In practice, stability times are trimed to the bare minimum in order to promote rapid, hard oxidation drying. Even so, anti-set-off spray powder and small stack heights are essential to avoid severe set-off and blocking. Bearing in mind the restrictions that apply to the chemistry of ligho vehicles as discussed in Section 6.1, it is not possible to achieve key to plastic substrates by incorporating resins of similar chemistry to the plastic in the binder vehicle of the ink. Key and adhesion have to be achieved through oxidation drying producting a hard, yet flexible, polymerized film. Because of this lack of formulating flexibility, litho inks cannot readily cope with the wide range of impervious substrates that are printed by gravure, screen and flexo.
A further complication arises in the areas of ink/water blance. Since the substrates are impervious they are unable to transport fount solution away from the impression areas of the press in the way that paper and board substrates can. This increases the likelihood over emulsification of the ink. As well as being a potential source of poor reproduction quality, such emulsification can also retard oxidation drying and provide another obstancle to satisfactory ink adhesion on print.
Despite all these potential pitfalls, correctly formulated oxidation drying inks in the hands of skilled litho printers regularly produce fully satisfactory work on foil boards and on plastic sheets. A typical formulation would be :
Phthalocyancine gree (OI Pigment Green 7) |
20.0 |
Oxidation drying Vehiclea |
70.0 |
Micronised PE wax |
3.0 |
Micronised PTFE wax |
1.0 |
Cobalt driers |
3.0 |
Manganese dries |
1.0 |
Alkali-refined linseed oil |
2.0 |
|
100.0 |
aBased on modified rosin ester containing high proportions of tung oil.
Inks for web-offset paper printing
The engineering advantage of handling a continuously running web rather than discreted sheets enables web-offset printing to cope with lower weight papers at significantly faster speeds than even the most productive sheet-fed press. This advantage can only be exploited with inks that are capable of printing and drying at high speeds. Thus, web-offset inks must be formulated to the correct chemistry and rheology for high speed, high shear lithographic printing and fast drying.
Coldset
A typical coldest formulation is illustrated by the following process cyan :
Phtalocyanine Blue (solvent stable) (CI Pigment Blue 15.3) |
15.0 |
Hydrocarbon vehiclea |
10.0 |
Process oilb |
50.0 |
Montmorillonite clay-gelled process oil |
20.0 |
280-320°C distillate |
5.0 |
|
100.0 |
- Low cost hydrocarbon resin in process mineral oil and distillate used to assist pigment wetting.
- Broad-cut liquid petroleum fraction, significantly less refined than the close-cut distillates used in quickset sheet-feed and heatset inks. Unlike distillates, process oils processes some pigment wetting capabilities.
Since coldest printing is used for relatively low quality, low cost publications, cost is a prime consideration in ink formulation, hence the use of hydrocarbon resin and process oil as the basic vehicle components. Where the dark colour can be tolerated in black inks, it is usual to utilize a cheap natural asphalt or bitument resin, such as gilsonite, in place of hydrocarbon resin to boost the pigment wetting capabilities of the process oil.
Heatset
Heatset inks are much more like quickset sheet-fed formulations. This can be seen from the following example :
Diarylamide Yellow (CI Pigment Yellow 12) |
15.0 |
Fast heatset vehiclea Fast heatest gel vehicleb |
75.0d |
Slow heatset gel veiclec Micronised PE wax |
2.0 |
Micronized PTFE wax |
0.5 |
Low armatic 240-260°C distillate |
7.5 |
|
100.0 |
- Based on a combination of modified rosin ester and modified hydrocarbon soluble resins at high resin : alkyd ratio in 240-260°C low aromatic distillate.
- As (a) but gelled with aluminium chelate.
- As (b) but on 260-290°C low aromatic distillate.
- The exact proportion of the various vehicles will depend on the desired balances between tack and viscosity and between stability and heasetting.
Resins are chosen for good solubility in low aromatic distillate but must also allow rapid solvent release for optimum heatsetting. A highly efficient wax combination is required, the achieve good surface slip immediately upon solidification of the ink film. This ensures that the print is protected adequately as is passes over chill rollers en route to the in-line folders and cutters.
(C) GRAVURE INKS.
Publication inks
Once a major source of publications print, the last 10 years has been the decline of the gravure process in favour of web offset, certainly where runs below 500,000 copies are concerned.
Publication gravure inks are formulated to achieve the lowest possible cost; the main demands are on their press performance. Once printed their prime function is to provide text and illustrations, merely requiring adhesion to the substrate and a moderate degree of scuff resistance and lightfastness.

Inks for catalogue printing
The ink requirements for catalogue printing are somewhat different from those outlined above. The coated paper normally used in highly calendered with a rather more brittle surface than magazine papers. This means there is less ink penetration into the surface and a reduction in mechanical bonding.
In addition to high glose, inks are required to have tough flexible films with good rub resistance and printability. As there is little assistance from the substrate, rapid solvent release and hard film forming properties are essential to ensure adequate drying. Because of the nature of the paper, press speeds are usually lower than those used for magazine printing.
The solvent system is usually toluene or possible toluene/ester Typical formulation of catalogue ink would be :
Phthalocyanine Blue (CI Pigment Blue 15.3) |
8.0 |
Chlorinated rubber |
15.0 |
Phenolic modified resin |
10.0 |
Resinous plasticiser |
5.0 |
Polyethtylene wax |
1.0 |
Toluene |
51.0 |
Ethyl acetate |
10.0 |
|
100.0 |
Packaging inks for paper and board Lables
The use of labels in packaging is widespread and varied, normally the preprinted labels is attached to the product container to identify its contents. Unlike printed wrappers, labels do not have close contact with the product, which is normally packed in glass, plastic, metal or some other impervious material. This allow, within certain limitations, a fairly wide choice of solvent and resin combinations to be utilized for label printing inks. When printed labels are produced for returnable bottles, the ink film should be penetrable during the washing process, which utilizes a dilute of caustic soda, thus allowing easy removal of the label.
Pigment selection will be dependent on colour requirements. A reasonable degree of lightfastness is obviously desirble and some labels may require product resistance. Where high levels of gloss in liquid inks should be utilized. Normally, ball milling or bead milling is the method of manufacture. Advantage can be taken of the low viscosity grades of chlorinated rubber to help promote gloss.
Typical fast-drying formula for labels :
Rubine 4B (CI Pigment Red 57) |
5.0 |
Lake Red C (CI Pigment Red 53) |
7.0 |
Chlorinated rubber |
12.0 |
Phenolic resin |
20.0 |
Resinous plasticiser |
4.0 |
Dioctyl phthalante |
3.5 |
Polyethylene wax |
1.0 |
Toluene |
27.0 |
Ethyl acetate |
10.0 |
Aliphatic hydrocarbon |
10.0 |
Some label printers have a preference for alcohol/ester-based inks choosing to avoid toluene for environmental reasons. This reduces the choice or resin systems considerable and normally means the use of nitrocellulose, maleic and ketone resins.
Non-curl properties and easy wash-off can be achieved by correct plasticisation and the choice of a suitable maleic resin. The main problem is to formulate suitable glossy inks that are sufficiently hard drying, especially when the label is not varnished. The use of specially developed, easily dispersed pigments give reasonable results. But as these pigments are limited range, it is often found to be expedient to use nitrocellulose chips as a means of equaling the gloss of the chlorinated rubber-based links.
Typical formula of a chip-based non-curl label ink :
50% Rubine 4B nitrocellulose chip |
10.0 |
50% Lake Red C nitrocellulose chip |
14.0 |
Maleic resin |
10.0 |
Dioctyl phathalate |
3.5 |
Wax dispersion |
5.0 |
Ethyl acetate |
40.0 |
Ethyl acetate |
14.0 |
Selected glycol either |
3.5 |
|
100.0 |
A third option for labels are co-solvent polyamide based inks, where advantage is taken of their natural non-curl properties and potentially high gloss levels. There are some limitations to their use due to the high degree of resistance to weak alkalis, which prohibits them being used on wash off labels. Also ink film based on polyamide tend to weld when ram punched or quillotined, therefore they cannot be used on the edges of the labels.
Over recent years there has been a small but significant increase in the use of metallised paper for labels. There have been problems associated with ink adhesion on this substrate, vacuum depositing process has been completed has alleviated problem to great a extent. However, as the surface is basically non-absorbent, problems can occur with ink trapping as is the case with aluminium foil and certain films. In these circumstances it is useful to use a co-solvent polyamide backing ink, overprinted with nitrocellulose inks.
Typical co-solvent polyamide ink :
Phthalocyanine Blue (CI Pigment Blue 15.3) |
10.0 |
Co-solvent polyamide |
22.0 |
Nitrocellulose |
3.0 |
Polyethylene wax |
1.0 |
I sopropanol |
12.0 |
Toluene |
37.0 |
I sopropyl acetate |
8.0 |
Ethanol |
7.0 |
|
100.0 |
Metallic label inks
Many labels require the use of metallic inks as part of the overall design. The various shades of bronze inks are particularly popular, usually they are the last colour to the printed in a multicolour design and often overprint one or more of the preceding inks.
Aluminum-based inks are used less frequently that bronze inks on labels. Primarilly they are used as background to give a metallic effect to overlying colours. Care is required in the selection of a suitable grade of aluminum if this is the case, to ensure interlayer adhesion. A typical formula for a bronze medium into which bronze powder would be added at 30-40% be weight is :
Chlorinated rubber (medium viscosity) |
30.0 |
Dioctyl phthalate |
10.0 |
Wax dispersion |
7.0 |
Stabilizer |
1.0 |
Toluene |
52.0 |
|
100.0 |
and a bronze ink : |
40.0 |
Bronze powder (gravure ink lining) |
20.0 |
Acrylic resin |
5.0 |
Stabilizer wax dispersion |
1.0 |
Toluene |
27.0 |
I sopropyl acetate |
7.0 |
|
100.0 |
Paper wrapper inks
With paper wrappers being used predominatly for food, confectionery and toiletry packaging, the choice for raw materials in gravure inks is largely determined by their suitability for these end used. It is of paramount importance that the dried ink film is free from odour or potential tain that might be derived from retained solvent or odorous resins. Although inks are not intended to come into direct contact with foodstuffs, they should not cotain pigments or dyes which are likely to bleed into food constitutents, for example animal fats. Vegetable oils and in the case of chocolate product, cocoa fat. Migratory materials should be avoided where possible and harmful pigments, chemicals and additives should not be used.
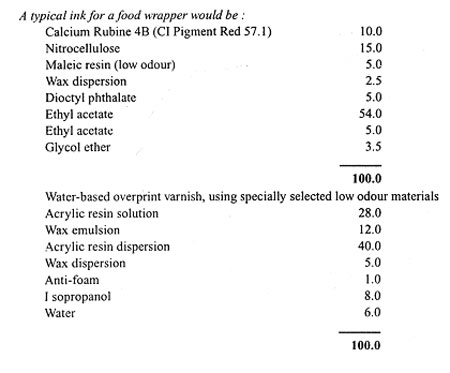
Carton Inks
This is one of the areas in which gravure printing competes with offset litho and comparisons in print quality are often made. For this reason the lay characteristics of a carton cravure ink is of critical importance. Also many of the cartons for well known brands of chocolate confectionery and cigarettes, have considerable coverage of a colour with which their name is associate. Therefore particular attention is given to the print quality to ensure that it is somooth and unblemished.
Almost invariable, cartons are varnished and as with paper wrappers water-based overprint varnishes have become increasingly important. All cigarette cartons and many chocolate boxes and overwraped with transparent film which is heatsealed directly over the printed surface. Obviously this requires the inks to be heat resistant and the overprint varnish to have heatseal relase properties against the particular film employed.
In addition to heat resistance properties, the water-based overprint varnish should be formulated to give an acceptable gloss level and also be based on hard drying acrylic resins which have the ability to release water from the drying varnish film as rapidly as possible. In this respect the amine content should be critically evaluated and, if tolerable, ammonium hydroxide should be considered. Sometimes the best overall results can be reashed by a carefully balanced combination of two amines.
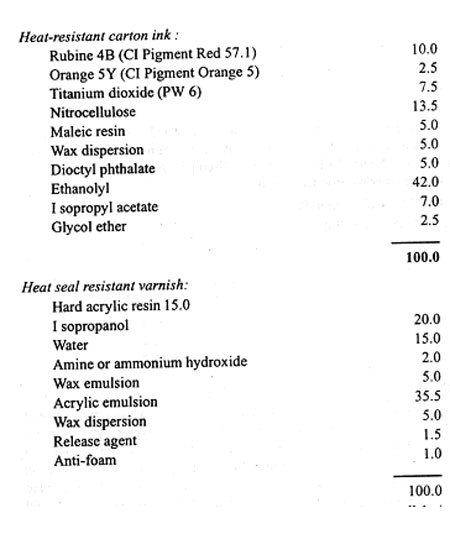
When metallic links are required for carton printing the overall design has to be carefully considered. If the areas of metallic print is small and if the ink has to overprint other colours, it is likely that the best printability will be achieved with a toluene-based acrylic resin type of ink described previously. If the ink is required to print directly on to the board then an ester-based acrylic metallic ink should perform satisfactorily.
Problems can occur when a large area of gold is required to overprint a nitrocellulose based colour and, be cause of the low odour requirements, a toluene system cannot be used. The best approach is to use a vinyl modi fied acrylic with a carefully balanced ester solvent system, suited to the machine speed and its drying capacity.
The choice of material for bronze inks is discussed in detail in the section dealing with metallic inks.
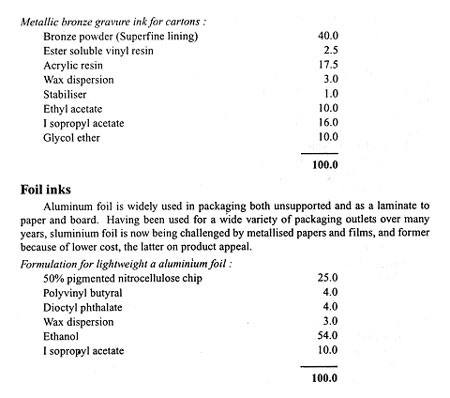
Foil board laminates
Printing foil board laminates was at one time almost exchlusively done by sheet-fed litho. The foil was usually coated with a cold tined nitrocellulose lacquer. After printing by offset the sheets were then varnished, often as a separate operation. A similar approach was followed when the gravure process was originally adopted to print cigarette cartons on foil board laminate. Using a shieet-fed machine the gold lacquered foil/board was printed in one operation. Problems were encountered with printability and adhesion on the gold nitrocellulose base lacquer.
It is now more customary to print on foil/bord laminates which have been coated with shellac. Often the darker colours are printed directly on to the substrate with the light colour, usually a good, printed last also playing the part of an overprint varnish.
For example :
50% Yellow 83 nitrocellulose chip |
3.0 |
50% Orange 5 nitrocellulose chip |
2.0 |
Nitrocellulose |
20.0 |
Modifying resin |
10.0 |
Wax dispersion |
5.0 |
Ethanol |
46.5 |
I sopropyl acetate |
10.0 |
Glycol ether |
3.0 |
|
100.0 |
Inks for polyethylene film
The vast majority of polyethylene film is converted by the flexographic process because of the similicity of the design or the length of run which makes the gravure process commercially unviable. However, derigns of a more complex nature still utilize the gravure method or alternatively the offset gravure process which can allow a blend of flexo and gravure printing stations.
Conventionally co-solvent polyamide resins have been used in gravure inks for polyethylene because of their excellent pigment wetting properties, good solvent release characteristics, good water resistance and not least they enable a high gloss print to be obtained. The trend to remove hydrocarbon solvents from packaging inks has meart a change to the use of alcohol-soluble polyamide resins. Unlike their co-solvent counterparts the alcohol-soluble grades have inferior solvent release and water resistance properties and modification with nitrocellulose is essential to provide inks of the desired quality.
For heat-resistant application polyamide resins cannot be employed and inks based on nitrocellulose modified with polyurethanes are used.
Inks based on co-solvent polyamide resin :
Phthalocyanine Blue (CI Pigment Blue 15.3) |
12.0 |
Co-solvent polyamide resin |
25.0 |
Antoxidant |
0.5 |
I sopropanol |
32.0 |
Toluene |
14.0 |
Aliphatic hydrocarbon |
12.0 |
Water |
2.0 |
Amide wax |
1.0 |
Polyethylene wax |
1.5 |
|
100.0 |
Inks based on alcohol-soluble polyamide resin :
Phthalocyanine Blue (PBI. 15.3) |
12.0 |
Alcohol-soluble polyamide resin |
13.0 |
Nitrocellulose |
18.0 |
Dioctyl phthalate |
2.0 |
Antioxidant |
0.5 |
Ethanol |
40.0 |
Ethyl acetate |
7.5 |
n-proply acetate |
5.0 |
Amide wax |
1.0 |
Polyethylene wax |
1.0 |
|
100.0 |
Inks for treated polypropylene films
Treated polypropylene films have continued to find increasing use in gravure packaging outlets. The homopolymer film. (i.e. Opp) is still little used despite being the lowest cost since it is unsuitable for heat seal operations and the corona discharge treatment losses its effectiveness with time. Treated co-extruded polypropylene films are mainly used for heat resistant applications while the 'pearlised' grades have attained tremendous growth in cold seal outlets. The pearlescent effect in these films in produced by air entrapped in the film rather than by use of mica pigment. The insulating properties of these air bubbles makes heat sealing difficult within the dwell time on a packaging line.
For co-extruded films, inks based on nitrocellulose modified with polyurethanes and titanium acetyl-acetonate (TAA) are used for both surface and reverse printing as well as for lamination. Tianium acetylacetonate acts as the adhesion promoter to the treated side for the film but has a drawback in that it may also react with the pigment to give an unstable ink. The same system can also be employed for printing on the treated side of homipolymer polypropylenes though higher levels of the adhesion promoter may prove necessary with a consequent risk of ink instability and high residual odour.
White ink for treated side of co-extruded polypropylene :
Titanium dioxide (CI Pigment White 6) |
30.0 |
Nitrocellulose resin |
11.0 |
Dioctyl phthalate |
3.0 |
Polyurethane |
8.0 |
Polyethylene wax |
1.0 |
Frucamide |
1.0 |
Ethanol |
27.0 |
Ethyl acetate |
16.0 |
Titanium acetyl-acetonate (TAA) |
3.0 |
|
100.0 |
Since in cold seal work there is no heat resistance requirement, polyamide inks can be employed with polyamide varnishes to give base adhesion to the treated polypropylene film. For this reason micronised polyethylene or polypropylene waxes are used to give the correct coefficient of friction levels to suit the packaging requirements.
Coated polypropylene films
The PVC coated polypropylene films are heat sealable and have excellent gas and moisture barrier properties. Modification of the PVC latex with a methacrylate can broaden the sealing range of the films.
Yellow ink for printing on coated polypropylene film :
Diarylide Yellow (CI Pigment Yellow 12) |
8.0 |
Alcohol soluble propionate |
10.0 |
Acrylic resin |
6.0 |
Ethanol |
45.0 |
Ethyl acetate |
30.0 |
Polyethylene wax |
1.0 |
|
100.0 |
Cellulose films
Due to the high energy costs involved in the manufacture of cellulose films they are continuing do decline in use in contrast to the increasing popularity of the polypropylene based products. For convenience the films can be divided into three categories :
(1) Single side coated films, using either a PVdC or nitrocellulose coating. The uncoated side (designated PT) must be printed and then laminated to another film to protect it from moisture. Inks are relatively simple, being based on plasticised nitrocellulose but high in ester solvents to prevent excessive retention of alcohol-based solvents.
Green ink for revere printing on PT film lamination A |
|
Diarylide Yellow (CI Pigment Yellow 13) |
7.0 |
Phthalocyanine Blue (CI Pigment Blue 15.3) |
2.5 |
Nitrocellulose (high nitrogen grade) |
14.0 |
Dioctyl phthalate |
5.5 |
Polyethylene wax |
1.0 |
Ethyl acetate |
70.0 |
|
100.0 |
(2) Two side coated nitrocellulose films are available varying in the content of wax and plasticiser in the coating to alter the properties of the film. While plasticised nitrocellulose inks offer excellent adhesion to these films great care must be exercised in the resin to plasticiser ratio to prevent blocking. The high wax content in the film coating also causes ink to pinhole and the surface tension of the ink must be adjusted, usually by the addition of a phenolic resin.
White ink for surface printing on N/C coated films :
Titanium dioxide (CI Pigment White 6) |
30.0 |
Nitrocellulose |
12.0 |
Dioctyl phthalate |
7.0 |
Polyethylent resin |
1.0 |
Polyethylent wax |
1.0 |
Ethanol |
30.0 |
Ethyl acetate |
19.0 |
|
100.0 |
(3) Two side PVdC coated cellulose films form the third grouping with the PVdC being applied via an aqueous emulsion or solvent based varnish. Ink systems are similar to those described for PVdC coated polypropylene films though since the coatings have better anchorage to the cellulose base retarding solvents can be used in moderatinon.
Polyester films
The high tear and impact strength of polyester film makes it particularly suitable for packaging both heavy and abrasive goods and its high heat resistance lends the film to boil-in-the-bag and retortable pouches. Only grades which are PVdC coated or have a special chemical coat can be heat sealed an therefore in the majority of applications lamination to polyethylene or foil and polyethylene is necessary.
For reverse printing and lamination uncoated polyester a vinyl ink must be used since other resin systems give poor bond strenghs either initially or after a period of time. It is especially important to select the pigments carefully for the vinyl carrier in order to obtain maximum flow and aid printability characteristics. Solvent retention can also be a problem especially with key tone/ester based laminating adhesives and alcohol soluble grades are therefore preferred as virtually no rewetting of the ink is then given.
On the rare occasions when inks are required for surface printing polyamide inks can be used for non-heat resistant applications. For heat resistant packs inks based on nitrocellulose modified with polyurethane and TAA, as for co-extruded polypropylene film, can be adopted.
For both surface and reverse printing of the PVdC-coated grades inks on CAP-acrylic systems can be used as previously described for PVdC-coated polypropylene films.
Red ink for reverse print and lamination on uncoated polyester film :
Barium 2B red toner (CI Pigment Red 48.1) |
9.0 |
Vinyl chloride/vinyl acetate/vinyl alcohol co-polymer |
10.0 |
Ethyl acetate |
40.0 |
n-propyl acetate |
40.0 |
Polyethylane wax |
0.5 |
|
100.0 |
Wall coverings
A variety of processes are used to print wall covering, with gravure, flexo and inks emboss predominating where surface printing once reigned supreme. Many manufactures use all three processes and it is not uncommon to see combinations of them used to print the same reel of wall covering.
A modern trend is for printers to carry the same range of inks for printing vinyl-coated papers and plain paper by both gravure and flexo. This is done to reduce the range if inks they have to stock. Normally the ink maker supplies a palette of colours along with reducing mediums, pearlescent bases and specials such as non-tarnish golds. Colour matching is carried out on site by the printer.
Inks for paper
Gravure inks for paper are normally expected to withstand the spongeability test without varnishing after embossing and the washability test after varnishing. As the base paper plays an important role in resistance to these tests, it is sometimes difficults to judge whether a failure is due to paper of ink.
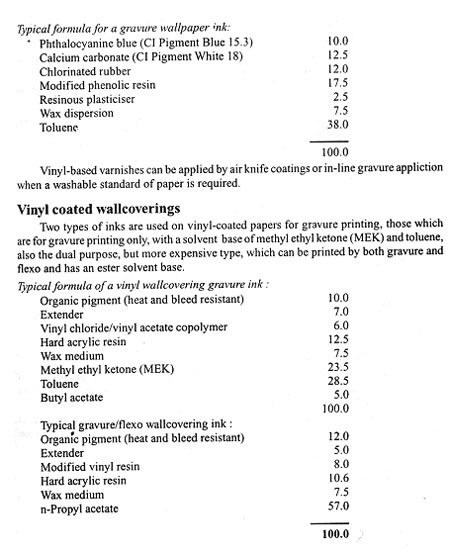
Specialty Systems
Metallic inks
For many years ready mixed metallic gravure inks were of minor interest to ink manufactures, as gold and silver inks were mainly blended on site by the printer. It was the development of frame board for cigaratte cartons using metallic bronze inks to match the existing gold lacquered foil board laminates, that introduced the need for premixed inks. Printers lacked the facilities to mix the large quantities of ink involved.
Inks for this purpose required careful formulation and must have the following basic properties :
- Be viscosity stable; although a slight increase in viscosity as the bronze powder is wetted out is normal, long-term stability should be achieved.
- Have good solvent release coupled with a low level of odour after printing. The use of toluene should be avoided.
- Exhibit a high degree of brightness even after prolonged storage as the frame board is often part of a foil board laminate pack.
- The ink should print with maximum coverage and minimum stration, for which all the components are important including the correct solvent balance.
- The ink film should be tough, flexible and have good rub resistance. However, as complete rub resistance is difficult to achieve, frame board is normally given a light coat of varnish.
With toluene being excluded and the adverse effect on storage stability of some alcohols, the normal choice of solvents for frame board golds, are esters with selected propylene glycols as retarders.
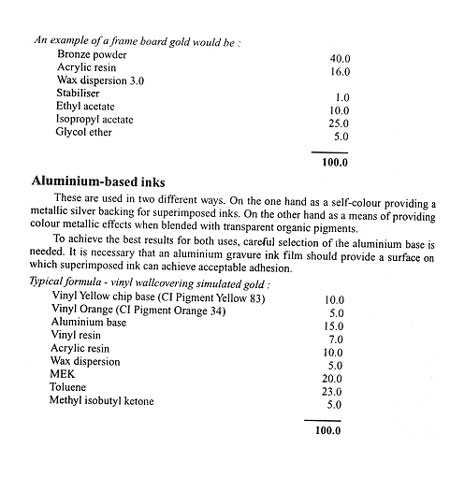
Pearlescent inks
The use of pearlescent pigments to replace pure mica has been a growing practice in the gravure printing of wall coverings. Their advantage is that they are more flexible and provide a considerably more cohesive surface than the old dextrin bound micas, thus ensuring adequate adhesion of superimposed colours.
Cosmetic and soap packaging designs take advantage of pearlescent inks to enhance customer appeal. As with wall coverings the pearlescent print often forms a background to the whole design. Overprinted colours are usually transparent thus allowing the pearl effect to be transmitted.
Typical formula-pearlescent ink for wall covering would be :
Pearlescent pigment |
20.0 |
Vinyl resin |
10.0 |
Acrylic resin |
15.0 |
Wax dispersion |
5.0 |
MEK |
20.0 |
Toluene |
25.0 |
MIBK |
5.0 |
|
100.0 |
(D) FLEXOGRAPHIC INKS
Dyes-based inks
The dyes can be dissolved by stirring but solubility and laking are improved if some heat is used. Denatured ethyl alcohol (methylated spirit) is the solvent and dependent upon the mordant which is used this can contain up to 6% water which can improve solubility although an excess of water will precipitate the laked dye. After the inks are made and allowed to stand at room temperature there will be a tendency for a small deposit to settle which should be discarded as this may cause problems on the press when printed.
Additions of resin solutions may be made, e.g. shellac or alcohol soluble maleic, to improve transfer properties and wax or glycerine resistance (glycerine being used to improve the flexibility of paper for sweet wrappers). If further resistances are required phenolic resins and other can be used. Ethyl cellulose in small quantities is sometimes added to reduce tack and also to increase drying speed. Glycol ethers may be incorporated to retared the ink and because they are good dye solvents they improve clean working on the press by keeping the type open during printing.
A typical formulation for a paper ink is :
Basic Yellow 37 dye |
8.0 |
Victoria Blue dye |
4.0 |
Tannic acid (or other mordant) |
20.0 |
Varnish (60% alcohol coluble maleic) |
5.0 |
Glycol ether |
4.0 |
Methylate spirit (64 op) |
59.0 |
|
100.0 |
Water-based inks
The traditional water-based ink for paper and board consists of a pigmented resin system, the resin being first dispersed into water. While a number of natural resins exist which are soluble in water such as casein and gum arabic they will also remain soluble after printing, which is not acceptable. It is therefore necessary that the resin be capable of being dispersed but then become insoluble once printed. One, method of achieving this is to add an alkali to a suitable resin and converting this to a soap or resin/water dispersion Traditionally shellac was used but has been largely superseded by carboxylated acrylics although other resins are also employed.
Water-based inks have several advantages, the first being that due to their low evaporation rate the inks are stable on the press without drying on the stereo or in the duct giving constant viscosity. Water does not attack stereo materials including photopolymers and the inks present no fire hazards and give economies by the use of water as a reducer and cleaning solvent.
A problem for the printer is the disposal of water ink and wash-up solution which tend to be generated at a larger volume because water is freely available. Such wastes cannot be discharged into the drains because of pollution and have no recovery value, the alternatives being expensive water treatment plant or the cost of dumping.
The most extensive area for use of water-based inks is for multiwall paper sacks and corrugated case printing where non-flammability and fast drying on the highly absorbent substrates are an advantage. Good water resistance shortly after printing is obtained and also good level of rub resistance essential for the case and box-making machines. Red water-based ink
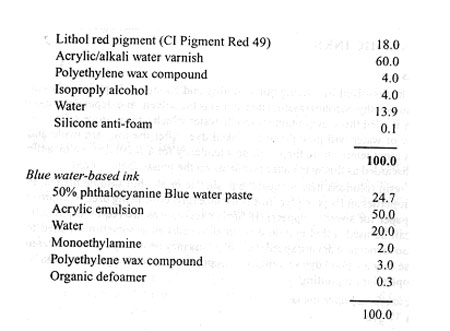
Pigmented Inks for Specific Substrates
Paper and board
In formulating pigmented solvent-based inks for paper substrates the main concerns are in producing inks having satisfactory colour and strength with good printing properties together with good drying and rapid solvent dilution characteristics. Adhesion to board and paper surfaces is not normally a problem with the possible exception of glassine and heavily coated papers. Most inks must be dry rub resistant unless and overvarnish, which may be matt or glossy, is used.
Flexographic printed papers are used for labels, packaging and decorative wrappers, wallpaper and other applications already mentioned and in the ink the choice of pigment must satisfy the resistance requirements associated with the end use. Generally wrapping and bag inks do not demand lightfast pigments except the normal avoidance of those with poor lightfastness in pastel shades since this will reduce lightfastness even further. Pigment used for waxed papers and soap wrappers would need to be insolouble in the respective material in each case.
The principal binder for these inks is nitrocellulose which has good pigment wetting and can be pigmented either by direct grind methods or, where increased gloss and strength are required, by using chip dispersions. Nitrocellulose resin gives good driving and single pigmented inks are not absorbed as readily into paper, as is the case with the dye inks, faster drying is required. Maleic resin is often used with nitrocellulose in the inks and the main solvent is methylated spirits with esters or glycol ethers to avoid solubility. Plasticizers and waxes may be incorporated to improve flexibility and rub resistance and other binders or modifiers may be used for special application or to give particular properties.
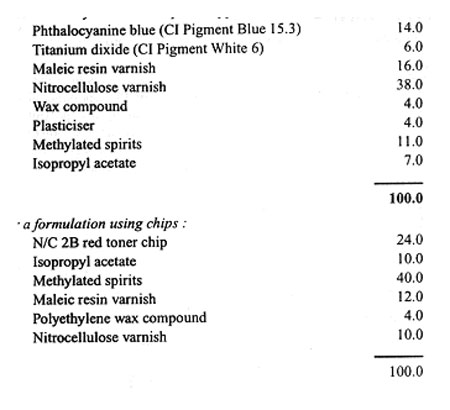
Nitrocellulose coated films
There are a number of cellulose films coated with nitrocellulose most of which are heat sealable.
Inks which are heat resistant are, however, more difficult to fuse. Solvent retention can be a problem and alcohol solvents can be absorbed more readily than other solvents. Heat resistant inks are often required for MS film if the print comes in the seal area and nitrocellulose is the normal binder used together with a modifying resin and plasticizer. It will be necessary to conduct tests to ensure that the formulation will not block and as satisfactory adhesion and flexibility particularly when inks are superimposed. A typical formulation for an MS film ink is :
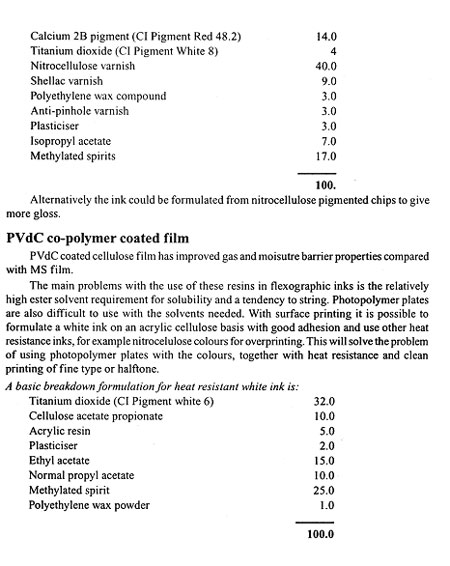
Isopropyl acetate is avoided due to its tendency to be retained by PVdC coating after drying.
Polyolefin films
There is a wide and expanding range of films in this group and together they now represent the largest use of packaging films. All of these materials are important with respect to the flexographic process and for the purpose of covering the inks requirement they are placed into three main categories, these being : uncoated, co-extruded and coated.
Polyethylene and uncoated polypropylene films
The different versions of polyethylene together with cast and oriented polypropylene are normally treated for flexographic printing as ink adhesion is difficult if not impossible on untreated film by this process.
Cast polyproylene films which is used for garment packaging because of its high clarity has somewhat improved barrier properties than polyethylene but because of the possibilities of lower treatment levels the alcohol dilutable inks many need some modification to improve their adhesion. In other respects similar inks are used.
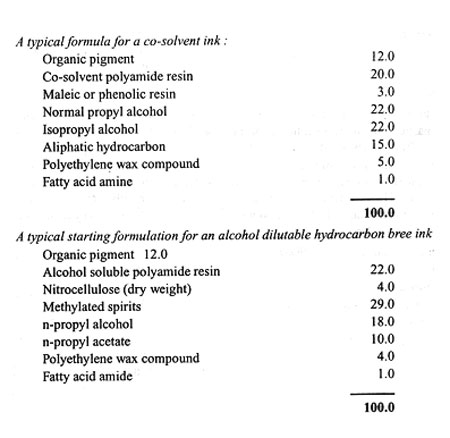
Metal and metallised substrates
Aluminium foil
This material gives the most light and barrier protection properties of all the flexible packaging materials and this together with its reflective appearance has led to foil being chosen where there properties are of high priority. The surface of aluminium tends to oxidize in the atmosphere rather quickly and adhesion becomes difficult.
Inks are required to be flexible and resistant to the packed products and with confectionery and chocolate wrappers, low odour level is essential. Esistance to blocking must be carefully tested particularly with virgin foil as pressure in the reel can be serve.
Bright transparent effects can be given using dye inks are already mentioned but for non-bleed results and high resistance specifications pigmented inks which are transparent can be formulated using selected pigments and chips.
A typical formulation for a transparent ink for aluminium foil is :
Nitrocellulose pigmented chip (60% pigment) |
20.0 |
Maleic or shellac varnish |
10.0 |
Alcohol soluble polyamide |
4.0 |
Nitrocellulose varnish |
10.0 |
Micronised polypropylene wax |
0.5 |
Plasticiser |
3.0 |
Normal propyl alcohol |
20.0 |
Methylated spirits |
22.5 |
Normal propyl acetate |
10.0 |
|
100.0 |
Metallic inks
These inks are made from aluminium or bronze powders mixed with a suitable resin solution. The particle size of the metallic and normally are larger than pigment particles and normally are leafing grades which give maximum reflectance and coverage.
Aluminium powders are more stable with resins than bronze powders but gold shades can be obtained with aluminium by mixing with a varnish that contains some dye or finely dispersee pigment. These mixtures are, however, less bright than with a bronze powder based ink but have the advantage of being copper free which may be necessary for certain food wrapper specifications.
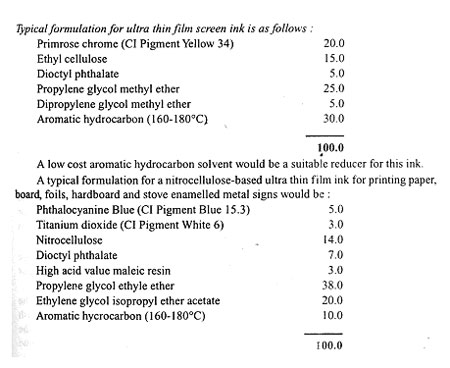
(E) SCREEN INKS
Inks for paper and board
The early screen inks for printing on paper were oil based. They usually contained a high proportion of coarse extender, such as whiting, and the vehicle was based on highly bodied inseed stand oil in white spirit.
Thin film screen inks
The most significant development during this early period occurred with the introduction of EHEC (ethyl hydroxy ethyl cellulose). This allowed the formulation of the first thin film screen inks. Inks based on EHEC were a significant advance in that they overcame the problems associated with 'cellulose inks', with the added advantage.
A typical formulation for a thin film screen ink for posters would be :
Toluidine Red (CI Pigment Red 3) |
5.0 |
China clay (CI Pigment White 19) |
36.0 |
Low viscosity EHEC |
6.0 |
Penta ester gum |
10.0 |
White spirit |
30.0 |
Aromatic hydrocarbon (160-180ºC) |
10.0 |
Propylene glycol ether |
3.0 |
|
100.0 |
The function of the ester gum resin is to increase the finish and assist pigment dispersion. This type of ink would be suitable for printing on most paper stocks. Typical applications would be poster printing both for indoor and outdoor use, showcards and point of sale displays in comparison to oil based inks, EHEC inks offer better rub resistance higher mileage, more finish and faster drying. Air drying time of the formulation give above would be approximately 20 minutes.
Ultra thin film screen inks
The increasing use of automatic screen printing machinery brought a demand for even quicker drying inks. This demand led to the development of the ultra thin film inks. The technique here is to use a cellulose derivative to give low solids and high viscosity vehicles. The introduction of higher speed printing machines permitted the use of more volatile solvents without problems of drying in the screen. The combination of lower solids vehicle and fast evaporating solvents formed the basis of fast drying, ultra thin film inks.
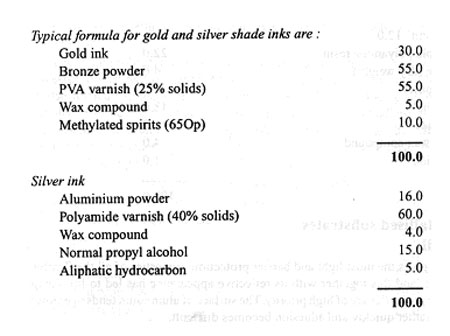
Blance fixe is chosen for its good gloss and leveling properties.
INKS FOR IMPERVIOUS SURFACES
Metal signs
Metal signs which are screen printed with non-ceramic insk are intended to have all life on 3-5 years. This is considerable more permanent that the relatively short lived paper poster but not as durable as a vitreous enameled sign. Typical applications of metal signs would be traffic signs, semi-permanent window displays, fire exit notices. In view of the long life of metal signs, the main requirement of screen ink is durability. This refers to lightfastness, weathering and adhesion.
It is normal practice to use long oil alkyds as the basis of suitable screen inks. These alkyds are ideally suited in that thick deposits are possible, which is essential for outdoor durability. Alkyd are also capable of being air dried or stoved and have a well-proven history of reliable weathering properties.
The inks are normally applied over a stoved enameled background; they may be stoved or air dried. Once the design has been printed it is then protected with a spraying or roller coating varnish. The completed sign is then subjected to a final stoving.
It is important that the screen inks are sufficiently dry to withstand attack from the solvents present in the spraying varnish. The base enamel, screen ink and protective varnish must be tested as a complete system. There should be good intercoat adhesion between the three systems. Formulation for a lightfast, durable, metal printing red ink is given below :
Quinacridone Red (CI Pigment 122) |
6.0 |
Calcium carbonate (CI Pigment White 18) |
24.0 |
Long oil linseed alkyd |
50.0 |
Mixed napthenate drier |
4.0 |
White spirit |
16.0 |
|
100.0 |
Drier content should be calculated on a alkyd resin solids. The amounts and type of drier to be used is dependent on the specific alkyd used; however, it is normal to use calcium, manganese and cobalt napththenate with long oil alkyds.
Metal containers
It is often convenient to add identification or other marking to drums. This can, of course, be done by normal stenciling methods but a neater result can be achieved with screen-printing. If a large number of drums are to be printed, then screen-printing is more convenient. The inks are not usually applied to bare metal but drums anamelled with a back ground colour. The screen print is usually air dried, particularly if the drums have a large capacity. The requirements of such inks are that they exhibit good adhesion and are not removed by the chemicals packed inside the container.
Since the printing process is liable to be slow and intermitten, it is desirable to use high boiling solvents in the inks to avoid drying in the screen. It is also necessary to restrict the flow of the ink : this is particularly important with screens that are physically carried form to drum.
A suitable ink would be :
Carbon Black (CI Pigment Black 7) |
6.0 |
China clay (CI Pigment White 19) |
30.0 |
Medium long oil alkyd |
54.0 |
Naphthenate driers |
3.0 |
Anti-oxidant |
0.1 |
Structuring additive |
3.0 |
Dipentene |
12.0 |
|
100.0 |
Inks for sheet plastic
The decoration of sheet plastics is now a very important part of the screen industry. Many traditional materials have, for economic and technical reasons, ben replaced by sheet plastics. A good example of this is the increasing number of traffic signs produced in acrylic sheet, to replace metal signs.
The variety of plastic substrates that exists presents problems to the inkmarker in that each substrate may require special consideration. An ideal situation is where one screen inks is suitable for all substrates; in practice this is not possible but an ink formulation whould be as multi-purpose as possible. Possibly, the nearest approach to this is a screen ink based on acrylic/vinyl resins.
An ink for a road sign must be very weather resistant and lightfast; pigments with Blue wool ratings not less than 7-8 should be used. In order to achieve a high degree of weathering, the ink must have excellent adhesion to the substrate. Some printed acrylic sheets are subjected to thermoforming, and the ink must be sufficiently flexible to withstand this process, However, if an ink has low softening point the prints will show mould marking if contact is made with the mould.
A lightfast red ink suitable for outdoor use on acrylic or PVC sheet would be :
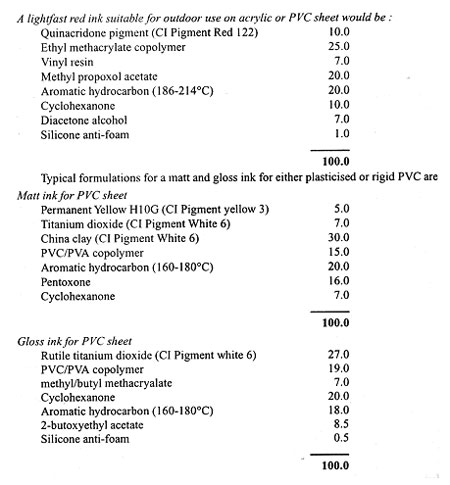
Inks for glass
Inks for screen printing on glass fall into two main categories :
- Conventional screen inks; and
- Ceramic inks.
A two-pack epoxy/polyamide, screen ink would be suitable for this application; a typical starting-point formulating would be :
Paste
Titanium dioxide (CI Pigment white 6) |
45.0 |
Epoxy resin |
35.0 |
2-Butoxyethanol |
20.0 |
|
100.0 |
Catalyst
Reactive polyamide |
70.0 |
2-butoxyethanol |
10.0 |
Aromatic hydroacarbon (186-214ºC) |
20.0 |
|
100.0 |
Mixing ratio 100 parts to 15 parts of catalyst. Mirror pictures, i.e. Where the silvered area covers only part of the glass, usually in the form of a simple picture or pattern are produced with the aid of screen printing. An acid resisting ink is printed directly on to the silver. The mirror is subjected to an acid bath which removes the unprotected silver. This leaves a mirror pattern against a clear glass back-ground. A suitable acid resisting ink can be formulated using isomerised rubber resins in aliphatic hydrocarbons.
Ceramic screen inks are used whete a permanent marks is required on the glass container, e.g. rerable drink bottle, glass ware pottery and laboratory glassware.
Ceramic screen inks can take a variety of forms and may be applied by direct printing, decalcomania or hot melt screen. Regardless of the type used, the principle is the same; the inks is fird into the glass and becomes an integral part.
A ceramic ink consists of pigment, frit or flux and a varnish. The function of the varnish is simply as a temporary carrier of the other components. After the ink is applied to a bottle, it is fired at temperatures in the order of 800ºC : the pigment and frit, know as the enamel, fuse into the glass and the varnish completely volatises at these temperatures.
Formulation for a ceramic screen inks for direct printing is as follows :
Ceramic enamel pigment |
52.45 |
Thixotropic alkyd |
26.23 |
Hydroquionone |
0.07 |
Napthenate drier |
0.13 |
White spirit |
21.12 |
|
100.0 |
INKS FOR PLASTIC CONTAINERS
Polythene containers
There are a number of alternative methods of decorating polythene bottles but, it India the most popular process is screen printing. The alternative processes are, letterset printing, paper labeling, hot melt transfer printing, hot foil stamping, in-mould labeling and shrink labeling.
The original polythene bottle inks were based on long oil linseed alkyds but in modern times better chemical resistance is required. An oxidation drying ink would be formulated by using epoxy ester resins as follows :
Phthalocyanine Green (CI Pigment Green 7) |
6.0 |
Titanium dioxide (CI Pigemnt White 6) |
10.0 |
Long oil epoxy ester |
82.2 |
4% calcium napthenate |
0.6 |
Silicone anti-foam |
0.2 |
|
100.0 |
PVC containers
Containe is made from PVC have, to a limited extent, replaced glass bottle. Typical products that are packed in PVC bottle are soft drinks, disinfectants, shampoos, and sun tan oil. The vast majority or PVC bottles are, in fact, paper labeled, not screen printed.
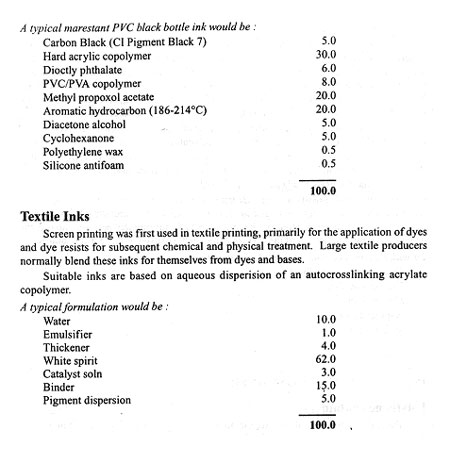
This type of ink is an oil-in-water emulsion where the oil is, in fact, white spirit. The high proportion of solvent, in a basically water-based system, gives an ink with easy printing properties and a low film weight. As a consequence the print does not impart any feel to the fabric.
Daylight fluorescent Inks
Fluorescence is a process of photo-luminescence by which light of short wavelengths, either in the UV or visible regions of the electromagnetic spectrum, is absorbed and reradiated at longer wavelengths. This re-emission occurs within the visible region of the spectrum and is manifested as colour. Fluorescent pigments are transparent organid resin particles containing dyes in solids solution.
Two main types of inks are available, evaporation drying or oxidation drying. The latter type gives thicker films and more brilliant results but is slower drying. In fact, oxidation drying fluorescent inks, due to the pigment loading, are tough-dry relatively quickly but then take several hours to become hard.
Two formulations for a fluorescent ink suitable for posters are given below :

When using fluorescent pigment in conjunction with kentone solvents, attention must be paid to the grade of pigment. Solvent-resistant grades are available which give complete stability with vinyl/ketone solutions.
It is essential to print all fluorescent inks over a white background because of the transparent nature of the pigment. It is possible to include some titanium dioxide in fluorescent inks but there is an inevitable loss of brilliance.
Process Inks
The quality of screen process printing line has improved dramatically, over recent years. This may be attributed to developments in inks, meshes, stencils, printing machinery, separation techniques and printing skills.
A good starting-point for formulating an ultra thin film process inks for poster printing would be :
Organic pigment |
3.0 |
Alumina hydrate |
8.0 |
Ethyl cellulose |
15.0 |
Eioctyl phthalate |
6.0 |
2-butoxyethanol |
33.0 |
Structuring additive |
2.0 |
Aromatic hydrocarbon |
33.0 |
|
100.0 |
Note that higher boiling point solvents are preferred to improve screen stability. For economic reasons and where appropriate it is possible to formulate either EHEC process inks or nitrocellulose based inks.
(F) UV AND ELECTRON BEAM CURING INKS
Formation principles for ultraviolet curable inks
The formulation of any printing inks has to take account of :
- the method of application ;
- the substrate;
- the end-use requirements.
In these respects UV curable inks are no exception.
However, as the major portion of the vehicle system has to be comprised of acrylated species the range and number of combinations of raw materials available is more restricted than would be the case with conventional oleoresinous inks.
The required body and tack of a UV curing ink or vanish is primarily achieved by balancing carefully selected grepolymess and monomers. Addition of diluent to a formulation usually result in a lowerint of tack, yield value and plastic viscosity. This is in contrast to experience with conventional formulation where it is often possible to adjust the theological parameters individually by choosing the ring type of solvent. Further, the viscosity reducing power of a reactive monomer is invariably less that of a typical petroleum distillate.
Most pigment types can be used in UV ink formulation, but some caution in selection is needed for three reasons. Firstly, as a class, acrylated resins do not possess particularly good pigment wetting characteristics. Consequently some pigments that might produce reasonable ink in a conventional vehicle are not suitable for UV or EB formulation. Secondly, some pigments are prone to initiating 'dark' polymerization reactions in the inks during storage. Such pigments must either be avoided or else a suitable stabiliser must be incorporated in the formulations. As these reactions may only manifiest them selves after several months storage, evaluation of individual pigments and stabiliser can be a problem. Acceleration oven tests may be useful but are not always reliable. Finally some pigments. Acceleration oven tests may be useful but are not always reliable. Finally some pigments inhibit cure. This may be result of chemical reaction with the initiating system, or it may arise because the pigment has significant UV opacity in critical special regions. Particular care is needed in formulating black inks.
All in all, formulating effective UV and EB ink probably calls for more and a greater understanding of the physics and chemistry involved than necessary to achieve satisfactory results for corresponding inks based on conventional resins.
Formulation for ultraviolet curing lithographic inks
By far the largest application area for UV curable inks is sheet-fed lithographic printing of paper and board. Formulations of inks for this type of printing will thus be considered in some detail. Many of the principles introduced, however, apply generally to UV ink formulations regardless of the method of printing.
A typical UV curable dark blue litho ink might have the formula :
Phthalocyanine blue pigment (CI Pigment Blue 15.3) |
16.0 |
Carbon black pigment (CI Pigment 7) |
4.0 |
Epoxy acrylate resin |
30.0 |
Fatty acid modified epoxy acrylate |
25.0 |
Monomer viscosity modifier |
8.0 |
Benzophenone initiator |
8.0 |
Coinitiator |
3.0 |
Aromatic amine photosynergist |
4.0 |
Stabiliser, waxes, etc. |
2.0 |
|
100.0 |
The choice of resin blend reflects the need for achieving good lithographic properties while maintaining an effective rate of cure. If the ink is to be applied to a substrate lacking in absorbency, metal, plastic or polyethylene coated board for example, it may be necessary to use a portion of a polyester or a polyurethane acrylate to provide improved adhesion; albeit at increased expense an possibily a sacrifice of cure speed.
A first choce for the photoinitiator package would be benzophenone combined with an aromatic amine. However, the example chosen is a comparatively dark colour and a coinitiator such as 2-chlorothioxanone would probably be required in order to attain a satisfactory curing speed.
Alternatively the use of a cleavage initiator such as dimetoxyphenyl acetophenone might be considered. This latter choice would be important in the case of a white ink where the yellow tint from a thioxanone would be unacceptable. However, the ultimate end use must always be kept in mind. A side reaction of the above initiator leads to the formation of methylbenzoate :
The odour and tainting risk introduced into a cured ink by this compound might be unacceptable if the end use involved foof packaging.
Even when one of the more exotic initiators is selected, it is customaryto leave some or all of the benzophenone in the formulation to retain the advantage of its pigment-wetting and plasticising properties.
As the lighographic process is involved, use of water-miscible amines should be avoided. Ignoring the insignificant effect that these compounds may have on the emulsification of the inks, there would still be a risk of them leaching into the fount solution with a subsequent reduction in cure efficiency. Thus the more expensive, but water insoluble, N, N-dialkyl aniline derivatives are preferred as phtosynergists for litho inks.
The body of a UV ink is controlled by the rheology of the tack and viscosity being made by the addition of monomer until as suitable printing rheology is attained. The selection and concentration of the monomer can best be made on the basis of experiments.
For process colour printing, tack grading of the inks for each different hue may be required to ensure satisfactory trapping. However, when process printing with UV inks it is popular, and relatively easy, to fit a lamp between print units, thus partially curing each colour before the next is applied and reducing the risk of back trapping.
Ultraviolet curable letterpress ink might have the following generalized formula :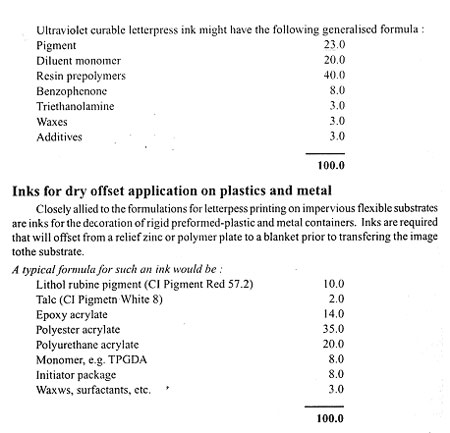
Ultraviolet curable silk screen
Silk screen ink films are typically between 20 and 60 um thick Although they can be much thinner, there is still a substantial depth for the radiation to penetrate when compared with the 3-5 um thickness of a letterpress ink. It might be expected that this would present incuromountable problems for formulating an efficiently curing ink.
However, silk screen technology has two characteristics which have favoured the development of successful UV curable products.
- The pigmentation levels are low and while high proportions of extender are used this is invariable transparent to UV radiation.
- Printing speeds are relatively slow, e.g. 130/m/min.
The wide spectrum of applications for silk screen printing, ranging from printed circuitry to glass bottle decoration, has provided many areas for the successful introduction of UV inks.
A typical formula for a UV curable silk serene ink suitable for decorating a plastic container would be:
Pigment |
8.0 |
Calcium carbonte extender |
20.0 |
Epoxy acrylate prepolymer |
25.0 |
Monomer, e.g. TMPTA |
27.0 |
Polyester acrylate |
5.0 |
Initiatore (1) 2-chlorothioxanone |
4.0 |
Amine, e.g. TEA |
3.0 |
Waxes, surfactant, etc. |
3.0 |
|
100.0 |
Ultraviolet curable varnish and coatings
Varnishes and coatings comprise a major portion of the market of UV products. Varnishing of printed material is carried out to provide protection and promote gloss. The ultimate target in both respects is the quality set by film lamination. Ultraviolet roller coat varnishes almost achieve this criteria for gloss and lay, while the UV printing viscosity products although an order of magnitude lower in gloss are still superior to conventional oleoresinous or magnitude lower in gloss are still superior to conventional oleoresinous or emulsion varnishes.
Scuff and rub resistance for UV curable varnishes can be excellent but to optimise these properties requires a correct balance of the prepolymers and the photoinitiators. Waxes will improve rub resistance, but gloss is sacrificed. Similarly silicones will provide desired levels of surface slip, but incorrect use may lead to reticulation and poor interfilm adhesion.
Because each varnish has to be matched to its proposed mode of application as well as its end-use requirements, it is far from easy to give a generalized formulation. For application at around 10 poise the following would provide a starting-point for an acceptable product:
Bisphenol A epoxy acrylate monomer |
13.0 |
Trifunctional polyether acrylate monomer |
60.0 |
Tripropylene glycol diacrylate |
5.0 |
Amine acrylate |
12.0 |
Benzophenone |
6.0 |
2,2-Dimethoxy-2-phenyl acetophenone |
3.0 |
Silicone slip additive |
1.0 |
|
100.0 |
(G) Non-Impact Printing
Two types of non-impact printing are of interest to the ink industry-electrophotography and ink-jet. The former is the principle used in photocopying machines which has developed over the years to fill a demand for short-run duplication work would be slow, uneconomic or practically impossible by conventional means. The ink-jet process uses a stream of minute ink droplelts projects from a very small nozzle and is widely used for batch and date coding of packaging and in the generation of variable data.
Electrostatic imaging
The foundation of modern electrostatic imaging lies in the invention of Xerography in 1938 and does not rely on any chemical reaction process to from an image, but utilizes a purely physical process based on the interaction of light and electricity.
Inks for jet printing
Traditional printing processes work because of contact of an inked image against the stock. Ink-jet printing is non-impact process that uses a stream of minute ink droplets projected onto the stock from a very small nozzle. There are two main systems.
The first uses a continuous stream of droplets which are electrostatically charged as they leave the nozzle and are deflected in flight by the application of a high voltage to a set of deflector plates.
The other techniques is known as 'drop-on-demand' or 'impluse' printing, because droplets are only released from the nozzle as they are required. The drops are not normally charged or deflected in their travel to the substrate. Thus a matrix consisting or a bank of nozzles is required to create the image.
Ink-jet is an extremely versatile, high speed, relatively low cost process and can be used, unlike any other process, to print delioate, uneven or recessed surfaces. Very high speeds can be achieved (60 000-1000 000 drops/second in a continuous jet printer).
Typical ink formulations
A. Solvent-based continuous jet ink
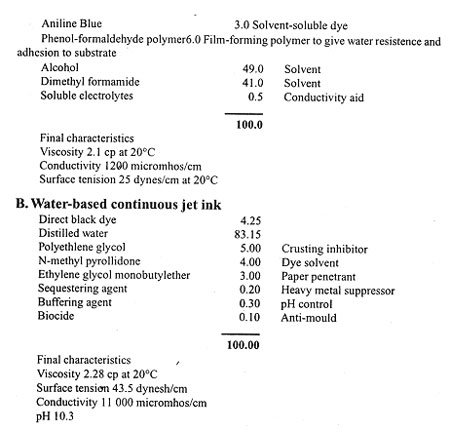
C. Drop-on-demand (impulse) system
D
Direct dyestuff |
3.0 |
Soluble dyestuff |
Polyethylene glycol |
14.0 |
Anti-clogging solvent |
Diethylene glycol |
12.0 |
Humectant |
N-methyl pyrollidone |
15.0 |
ye solubiliser |
Biocide |
0.1 |
Anti-fungal |
Buffering |
0.3 |
pH control |
Polymvinyl alcohol |
3.0 |
Viscosity controller |
Triethanolamine |
1.0 |
Surface tension control |
Distilled water |
51.6 |
Solvent |
|
100.0 |
|
Final characteristics
Viscosity 9.0 cp at 20ºC
Surface tension 45 dynes/cm pH 10.5
(H) INKS FOR THE ELECTRONICS INDUSTRY
Printed circuit products
Despite the fact that term 'ink' is rarely used nowadays to describe products used in the manufacture of printed circuit boards, it is not surprising to find that a few ink manufacturers, with their specialist knowledge of coating technology, have taken up the challenge offered by the electronics industry. The term used for such coatings is 'resists' and the three types most commonly used are etch resists, plating resists and solder resists.
Strictly speaking, we could not use the description 'printed circuit', as this implies that the circuit is applied by a printed process.
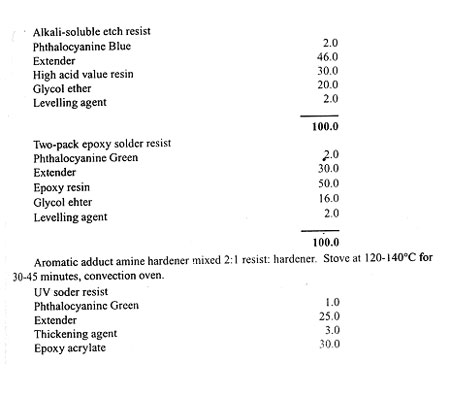
Aromatic adduct amine hardener mixed 2 : 1 resist: hardener. Stove at 120-140ºC for 30-45 minutes, convection oven.
UV soder resist |
|
Phthalocyanine Green |
1.0 |
Extender |
25.0 |
Thickening agent |
3.0 |
Epoxy acrylate |
30.0 |
Reactive monomer |
37.0 |
Levelling agent |
2.0 |
Photoinitiator |
2.0 |
|
100.0 |
Thermal-curing notation ink |
|
Titanium dioxide |
20.0 |
Extende |
20.0 |
Epoxy resin |
40.0 |
Glycol ether |
18.0 |
Levelling agent |
2.0 |
|
100.0 |
Amine hardener mixed 6 : 1 Ink : hardner, Stove at 120ºC for 30 minutes. Much of the technology of resists and board-marking inks is now based on UV curing because of the following advantages :
- Dimensional stability of the boards is maintained. The temperature of the board does not rise above 50ºC/
- Resists and inks are solvent-free and thus have excellent screen stability. The flammability hazard is removed.
- Productivity is increased. The boards can be processed very rapidly.
INK
(1) INKS FOR WALLCOVERINGS
The development of inks for wallcoverings has become a very specialized technology because of the unique end use of the product. Flexo and gravure are both used to print wallcoverings and ink systems are now available to deal with the demands for washability on paper substrates and the specific needs of the popular vinyl materials.
Water-based flexo inks are now widely used, based on acrylic emulsions which give the necessary toughnes and resistance properties.
Water-based flexo wallcovering ink
Pigment Yellow 83 |
10.0 |
Acrylic emulsion |
74.0 |
Anti-foam |
1.0 |
Water |
5.0 |
Isopropanol |
5.0 |
Wax paste |
5.0 |
|
100.0 |
Vinyl-coated substrates have exceptional durability and inks must be formulated to meet the higher specifications. This is achieved by suing vinyl resins and with the introduction of resistant stereos, there has been a trend towards flexo using hydrocarbon-free inks.
H/C free flexolgravure vinyl wallecovering ink
Pigment Yellow 83 |
10.0 |
Vinyl/acrylic varnish |
55.0 |
Ester |
20.0 |
Propylene glycol ether |
10.0 |
Anti-blocking agent |
1.0 |
MEK |
4.0 |
|
100.0 |
Pigment selection is important for wallcovering inks and a minimum lightfastness reading of 5 on the Blue wool scale is essential. Also, pigments for vinyls should have sufficient heat resistance to resist heat embossing and should not bleed in PVC and plasticiser. While the traditional method of achieving these properties was to use inorganic pigments, theindustry in general has moved away from their use an dmore expensive, resistant grades or organic pigments are utilized.
Embossing is a technique for improving the appearance of wallcoverings and can be achieved either by physical or chemical means. In the second case, a specially formulated vinyl coating is used which contains a 'blowing' compound and an activator which will cause the coating to expand when heated. In those areas of the design where expansion is not required, a special ink containing an inhibiting agent is applied. At high temperature, the inhibitor reacts preferentially with the activator in the coating and prevents the blowing action. Designs can be varied, register is good and deep emboss can be achieved. More recently, an even deeper soft-touch emboss can be achieved by pattern printing the vinyl coating by rotary screen, thus elimination the need for inhibitor.
(1) TEXTILE TRANSFER INKS
Sublimation transfer printing involves the dry sublimation of dye from a printed paper when the paper and synthetic fabric are brought together at around 200ºC. Only the dye is transferred, leaving the ink resin on the paper. The transfer can be regarded as taking place in two stages. Firstly, the dye is sublimed on to the surface of the textile fibres; secondly, the dye diffuses into the fibres to give the necessary standard of fastness.
Flexo water-based heat transfer ink
Dispersed dyestuff |
15.0 |
Alkali solublised aqueous acrylic |
65.0 |
Anti-foam |
2.0 |
Wetting agent |
0.5 |
Water |
15.5 |
Amine |
2.0 |
|
100.0 |
(K) STERILISATION INKS
Specialise printing inks that undergo an irreversible colour change during sterilization are widely used on the packaging of surgical or medicab products. Such inks are used to identify if the contents of the pack have been properly sterilized before they are used. There are several ways that sterilization can be carried out-dry heat, wet heat (autoclaving) and by using gas or radiation.
Onr-pack steam sterilization ink
Lead thiosulphate |
27.5 |
Zinc sulphide Extender |
10.0 |
Butyrate resin |
13.0 |
Plasticiser |
2.5 |
Wax methylated spirit |
45.0 |
|
100.0 |
Gas sterilization normally uses ethylene oxide, so nay indicator must be based on a raw material which gives a colour chance response on reaction with the gas. One such hydrated magnesium chloride which is converted to magnesium hydroxide which in turn causes a colour change in the presence of an alkali/acid indicator such as bromophenol blue or methyl red.
(1) Metal Decorating Inks
Metal has tremendous scope because of its strength and the ease with which it can be formed into shapes. Thus it has become widely used for cans for food, household products, beers and beverages, aerosol cans, tins for sweets and biscuits, caps and closures for bottles and jars, collapsible tubes, drums, trays, ashtrays and advertising signs. Its decoration and protection can often involve the use of a complex system of enamels, varnishes, lacquers and inks. The technology of enamels, varnishes and lacquers is a study in itself and falls outside the scope of this book. This section will concentrate on the role of the printing inks used in the decoration of tinplate, tin-free steel and aluminium.
There are two ways of decorating metal :
- Print a flat sheet which is subsequently formed into a can, closure, tray, etc,; or
- Print a pre-formed container.
Decoration of sheets
For Sheet-fed printing, decoration can take place directly on to themetal surface or over a transparent size or pigmented enamel previously applied by roller coating. Lithography and dry offset are both used for applying metal printing inks.
Metal printing ink-sheet fed
Diarylide Yellow |
30 |
Long oil alkyd |
58 |
Antioxidant |
1 |
Driers |
2 |
Reducer |
9 |
|
100 |
The traditional technique of using a long, traveling oven is still widely used. The printed sheed are picked up on an endless chain of racks (known as ‘wicketsâ€TM) which carry them through in a vertical position. Hot air is blasted at the sheets as they pass through the oven and the total stoving time is in the region of 10.15 minutes. With some exceptions, the inks are protected by a suitable finishing varnish.
Printing a pre-formed container
One of the most radical advances in can making in the last few years has been the development of the two-piece drawn and wallironed (DWI) container. It consists of a body and base made in a single unit from a flat strin or coil of aluminium or tinplate.
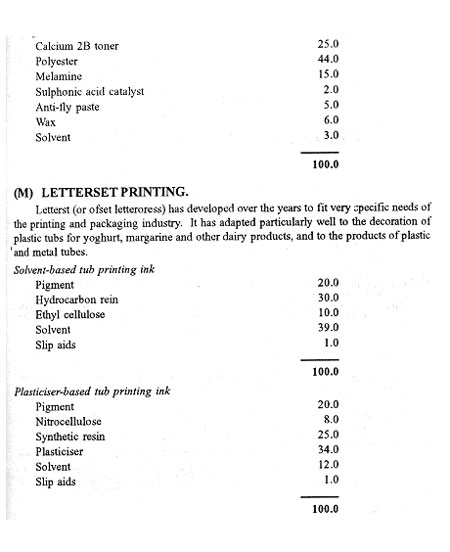