It is a process manual, semiautomatic or fully automatic for the manufacture of plastic articles and it is the basic, fast, economical and major processing method and require little or no subsequent finishing operation or rework for the product.
Plastic moulding especially thermoplastic items may be produced by compression moulding methods, but since they are soft at the temperature involved, it is necessary to cool down the mould before they may be ejected. This would not be convenient since on a run of production, it is desirable to keep up the temperature to avoid the slow and protracted operation of alternative heating and cooling . Besides much time has to be spend for accurate charging. This has resulted in a process of injection moulding technique.
Injection moulding differs from compression moulding is that the plastic material is rendered fluid in a separate chamber or barrel, out side the mould is then forced into the mould cavity by external pressure. The mould is cooled and split, the two halves being locked by pressure to resist injection force during moulding and opening automatically when the mould cavity has been filled by the molten plastic. The cooled, hardened or vulcanized article is then ejected from the mould and the process repeated.
In simple machines, it consist of a heated barrel with hydraulically, pneumatically or manual operated ram, an opening in the rear of the barrel there is a hopper into which measured amounts of plastic material generally in the form of granules are fed. The material is then forced under high pressure by the plunger into the heating zone of the barrel, pushing out an equal weight of molten plastic into the mould. A torpedo shaped distributor and the nozzle to heat the plastic uniformly and to feed the mould.
In a typical injection moulding machine, the plastic is feeding through a hopper which is loaded using a hopper loader fitted outside the machine. The material is then feed to the heating zone by the rotating screw whose rotation is controlled by an electrical device and the screw not only intake required volume of material but also acts as a ram as described earlier. The groves of the screw distribute the material uniformly around the barrel and forces the heat plasticized material in to the mould cavity. Higher capacity is achieved by the incorporation of plasticizing units, which increases shot capacity and by operating at low temperature reduces decolouration and degradation of the material. All of these machines are self contained in so far as heating and pressure pump units are concerned, and they have control system that make either automatic or semiautomatic. The mould locking is achieved by toggle or hydraulic clamping mechanism. The nozzle may be fitted with a device known as non-return valve to prevent premature leakage of molten plastic and to permit high pressure build up before the shot begins.
A. A good injection moulding can be achieved by the correct selection of machinery, proper mould design, mould, right material, and best processing method.
As mentioned earlier almost all the items can be produced by compression moulding. But it is not an economical method in most cases. Similarly a conventional mould can not offer uniform and economical production in the place of a hot runner mould, if the quantity of the moulding is very high. A number of hand mould is equal to a machine mould and a number of machine mould is equal to a hot runner mould in the case of small parts. When we switching to the latter method much time, manpower and material can be saved and also higher quality and uniformity can be achieved.
Similarly the processing parameters and setting methods are equally important. When we use solid inserts, direct cooling to the insert is better than nest cooling. A nest can give 80% of the cooling effect, a back plate can give 50% of the cooling effect and the pipe ring fit can give 65% cooling and tubular coils can give 10%. Every machine settings must be based on the consideration of the mould profile and the size of the moulding than standard setting parameters prescribed by the manufacturer. Always remember to add only the right percentage of ground material.
When using hot runner, temperature control to each cavity is necessary so that even if one cavity fails it will not affect production run. Similarly for large 'mouldings, valve gate instead of valve pin offer faster cycle. The gate system must be suitable to the moulding and material, considering the type of mould, and number of cavities.
B. Correct injection speed is necessary for filling the mould.
All parts of the mould should be filled in correct injection pressure to avoid jetting and formation of weld lines.
The mould must be filled with correct pressure. It must be as low as possible but as high as necessary. There is no solution if the material jammed due to solidification of the sprue, runner or by partly filled moulding.
C. Plastic melt should not suffer degradation. Correct plasticisation is a must for good moulding. For this;
- Material should be in an amorphous thermoplastic condition.
- Volume utilization should not be less than 45% but at any case less than 20%.
- Residence time should be as less as possible.
- If possible higher capacity machines should be avoided.
- Frictional heat from screw should be taken into consideration.
- Speed of rotating screw should be controlled.
- Back pressure should be adjusted to avoid excessive heat.
- Maintain correct mould temperature for the particular plastic material.
- The cooling must be uniform with respect to the profile.
- Use releasing agents for smooth ejection of part if sticking; in the beginning.
- For parts have undercuts, threads etc., employ a faster and earlier ejection.
- Furring-up of mould is harmful to temperature controllers.
- When the cycle must be interrupted also interrupt the temperature controls so that the mould temperature will not drop heavily.
- Each moulding should be solidify in the direction of sprue, so that follow-up pressure intended for compensating the shrinkage can remain effective in the last stage.
- For moulds have side cores, use coupling system for ejection to avoid mistakes.
- Operate separately complete system before the commencement of moulding cycle.
- Check the gating whether it is applicable for the particular material when moulding in another material.
- The important points to be noted are ;
- The material temperature should be as low as possible to avoid degradation.
- The cylinder utilization should be as high as possible to avoid degradation,
- The residence time should be as low as possible to avoid degradation.
- Use correct screw size and speed to suit moulding .
- Use correct back pressure to suit moulding .
- The cycle time should be in proportionate to the part,
- The screw should be suitable for the particular material.
- There is a connection between injection pressure, quality of the moulding, cooling system, and pressure built up.
- There is an interlinking between injection speed, material, cylinder temperature, gating and runners, shape of moulding, surface quality, flash and clamping force etc.
- There is an interaction between back pressure, material, screw size and type, and plasticizing capacity of the machine.
- Instead of using trial and error, use stored data, if available.
- If the mould is a new one or first time loading for production, it should be handled by experienced personnels.
- Check the screw, valve system etc. before loading the mould. For example for acetal ordinary screw is not sufficient. Similarly for nylon and PPS flow control valves are necessary,
- Avoid break in cycle to get better quality products,
- Do not start with maximum force and speed; start from minimum possible values.
- Avoid hard impact of mould halves,
- Extreme speed charges should be avoided,
- When flashes noticed first up all check mating surface instead of increasing mould locking force,
- Do not eject part at extreme speed.
- Use correct tools, mould, and material.
- Spend a few minutes for oiling and greasing the machine and mould.
- Open the bag for material only at the time of loading to the hopper.
- Use only pure material and recommended percentage of ground material.
- When changing inserts in a production running mould, it should be done by the recommended person,
- When moulding using same material for long period, frequent cleaning of material will improve quality of product,
- Avoid reground of blended material especially with rubbish materials.
- Keep the floor and machine clean, so that the operator will not slip.
- Before starting the operation, see whether the safety guards are in place; there is every chance for damaging the hand.
- When plastic material jammed in moulds, use softer materials to take it out.
- Heating the mould with electric heaters before the commencement of production can solve the above problem,
- If the mould have side cores, make it sure that it will not 'foul' or use coupling system for ejection.
- When squirting out material, protect the face and hands,
- When moulding corrodable material take necessary steps to safe guard the mould and machine.
- Which is the material, grade and manufacturer.
- Processing data's for the particular material.
- Pre-dying is necessary or not ?
- Allowed percentage of reground
- Which machine can be used; and the type of screw required.?
- Whether the material is corroding type or not.?
- Where is the material kept and volume is sufficient or not.?
- Previous experience.
- The part drawing and tolerance.
- Quantity requirement and allotted time.
- Have it previously produced or not ?
- Time gap required between production and Q.C. check for the particular material.
- Annealing required or not.?
- Other finishing operations.
- Assembly operation and inserts.
- Special fixtures and checking equipment's.
- Time required for rework, if necessary.
- Weight and size of moulding.
- Where is the mould.
- Mould size.
- Type of mould and number of cavities.
- Mounting, cooling or heating facilities.
- Mould have side core or not, if so safety measures like core pullers required or not?
- What temperature control is necessary and what preparation is required.
- Additional attachments required or not?
- Previous experience.
- Suitable machine and its specification.
- Available date and condition of machine.
- Any additional equipment like hydraulic ejectors or core puller required or not?
- Type of nozzle required.
- What cylinder required for the process.?
- Previous experience.
- Hand injection moulding machines.
- Horizontal injection moulding machines.
- Vertical injection moulding machines.
- Universal injection moulding machines.
- Multi colour injection moulding machines.
- Special purpose injection moulding machines.-
- Shot capacity
- Plasticizing rate
- Clamping force
- Injection pressure
- Ejection force
- The weld like formation area of moulding, should cool at last ; so that for the next cycle these areas will be hotter than the injection points.
- Large difference in cooling water temperature between the inlet and outlet, or across subsidiary water circuits should be avoided, since these lead to differing temperatures in various parts of the mould and may cause moulding difficulties.
- The amount of cooling provided must be sufficient to maintain the temperature of the mould when the latter is running at maximum production. So additional cooling if necessary should be provided on back plates.
- The inlet and outlet should be on the same side and normally at the rear of the machine, in order to prevent restriction for the operator.
- Where ever possible use extended nozzle to mould inserts so that optimum result can obtained.
- The design should be such that there should not be any leakage between plates or inserts ; use 'O' rings or gaskets.
- Overheating leads to the production of formaldehyde gas and if produced in sufficient quantities with in the container of an injection cylinder or extruder barrel, the gas pressure may become sufficiently high that there is a risk of damage or injury and the gas effect is similar to tear gas. A typical copolymer maybe kept in an extruder barrel for 110 minute at 190°C before serious discolouration occurs. Dead spot must be carefully avoided.
- Although less hygroscopic than the nylons, it must be stored in dry place.
- With most homopolymers and copolymers the apparent viscosity is less dependent on temperature and sheer stress (up to 10 6 dyn / cm2) than the polyolefins thus simplifying mould design. On the other hand the melt has a low elasticity, and strength and so extruded sections need to be supported and brought below the melting point as soon as possible .
- The high crystallinity which develops on cooling, results to a shrinkage of 2%. Because of low glass transition temperature, crystallization can take place quite rapidly at room temperatures and after shrinkage is usually complete within 48 hours of moulding or extrusion. In processing operations injection moulds, blow moulds and sizing dies should be kept at about 80 - 120º C in order to obtain best result.
- Because of low glass transition temperature (- 13 °C and - 73 °C ) it is not possible to make clear film, stable at room temperature, by quenching. Some improvement in, clarity may be obtained by cold rolling as this tends to dispose the crystal structure into layers.
- Injection pressure to fill the mould and pack out parts.
- Injection speed required for filling.
- The dimensions of parts and runners at the mould parting line (projected area of cavities and runners)
- Side cores, core pull requirements etc.
- Precision and tolerance requirements.
- Indication of actual operating values
- Automatic indication of high and low values for various parameters
- Display of fault alarm and logging with time occurrence
- Statistical process control of various parameters like melt cushion position, refill time, refill end position, fill position, fill time and cycle time.
- Cylinder heat temperature monitor
- Shot counter
- Mould data memory up to 50 moulds
- Setting protection by 3 password
- SR control circuit for heater bands
- Hour meter
- Mould temperature controller
- Automatic starting system for heater
- Alarm lamp
- Mould cooling water / oil heater connection with valve and flow indicator
- PC connection.
- Mould temperature
- Injection pressure
- Screw forward time
- Melt temperature
- Gate size
- Part thickness
- Grade of resin
- Reinforcement
- Too small machine for shot size and production rate
- Insufficient clamp capacity
- Melt temperature too high or too low
- Screw forward time less than gate seal time
- Too rapid freezing of too thin gate
- Operating with different mould temperature
- Poor mould temperature control in each cavity or from cavity to cavity
- Injection pressure too low
- Poor gate location for adequate filling of mold may result in voids
- Leaking back flow valve.
- Do not regrind moulded parts, sprues or runners that are discoloured or splayed. These conditions shows that the material is degraded during processing.
- Avoid accumulation of reground resin whenever possible by continuous reuse of sprues and runners.
- Maintain a constant ratio of reground resin to virgin always and mix adequately prior to molding. A suitable ratio depends upon the quality of the reground and the thickness of the part. Quality of the part is another important point. A 2:1 ratio of virgin to reground is allowed maximum for large and thicker components, still higher ratio is common.
- Keep grinder blade sharp and properly set according to manufactures instructions to minimize fines formation.
- Use cutter screens with 8 mm (5/16") holes.
- Remove excessive quantities of fines using vibrating screens.
- Avoid reprocessed resin from outside sources.
- Store in dry place and preheat before moulding.
[/ol]
D. The mould must be controlled for better quality product. Bear in mind that the mould is setting the shape. The points to be noted are :
E. Logical consideration of moulding profile and material is important than standard setting guide lines.
F. Economical setting of the machine.
For an economical, quality and faster production, the following points should be noted.
G. Proper maintenance of machine;
H. Safety Operations.
PRELIMINARY CHECKING FOR MOULDING
A. Material
B. Component
C. Mould
D. Machine
Injection Moulding Technique
The capacity of moulds to produce parts is completing only, when it is fitted to the correct injection moulding machine. So it is essential that the mould should be designed to suit the moulding machine of sufficient capacity and its cooling system and ejection system should be suitable for the machine. " THE MOULD MAKING THE SHAPE OF PARTS WHERE AS THE MOULDING MACHINE SETTING THE SHAPE"
The Various Type of Injection Moulding Machines are.
With hydraulic, pneumatic or toggle joint clamping system in the fashion of semiautomatic/fully automatic/ progra-mmable/ Multi-microprocessor control machines without or with independent temperature control to each cavity for sprueless or runnerless moulding.
2. Platen Mounting of Moulds
Moulding machines have two halves for mounting the mould; the fixed half and the movable half. Standard threads at standard distance is provided in them to facilitate easy mounting of the mould. These two platens are aligned with the tie bars or by side frame construction. For both halves a center bore is provided to locate the mould. This center bores and nozzle of the machine are in one axis.
For hand moulding machine the clamping is against the frame and the machine available only in the vertical model for direct injection.
3. Locating Spigots
There are two types of locating spigots also known as locating ring / register ring. The first model have around 0.5 mm clearance with the sprue bush and around 0.05 - 0.1 mm clearance with the machine bore. An H7/g6 fit is provided between the clamping plate bore on mould and the register ring. This method is adopted where the sprue bush have separate heating and the clamping plate have insulation. The main advantage here is that the heat will not conduct to much to the machine platen. So it is widely used for hot-runner moulds and for bigger moulds. The second method is with out bore for mounting plate. The spure bush head is directly located with the spigot using H7/g6 fit and the spigot have around 0.05 - 0.1 mm clearance to the machine bore.
4. Mould Clamping
Two methods for securing the mould to the press platens are in general practice, namely direct clamping and clipping. In the first method the bolts are passing through the hole or milled slots on the clamping plate to the platen. In second method a separate metal clamp/dog is used. It can be flat or "Z" type to suit the mounting plate. Second method is more popular because the position of clamping holes and thickness of plates are unimportant.
Press Capacity
Before the mould loading for production ; it is necessary to determine the press capacity that will be required for successful operation, and hence the particular press to be employed. When the actual moulding machine is known that the information necessary in respect of design data for mounting, platen area, tie bar clearance; can be obtained as previously indicated. The essential consideration are;
1. Shot Capacity
Injection pressures are normally rated by the maximum weight of moulding material that can be injected per shot. Originally this was given as the weight of cellulose acetate, but present practice is to express the weight in ounce /gm of polystyrene (PS). Thus to determine the shot capacity of a machine with any other material B from a machine specification that is based on material A. (PS) is,Shot capacity with material B = Shot capacity with material A ´ Density of B / Density of A.
If the bulk factors of the plastics are not equal then the calculation must be multiplied by the factor bulk factor A / bulk factor of B. This method widely using for plunger machines. For screw machines the formula is, Shot capacity (g) = Swept volume (cm3) ´ density of melt at plasticizing temperature and pressure (g / cm3).
If the effect of pressure is ignored then,
Shot capacity (g) = Swept volume (cm3) ´ e ´ c
Shot capacity (oz) = Swept volume (in3)´0.5776 e´c
Where e = density of plastic at normal temperature in g/cm3, and c = Correction factor ( % volume expansion at moulding temperature).
Correction factor for amorphous materials C = 0.93 Correction factor for crystalline materials C = 0.85
Shot capacity can also be calculated roughly by using standard values (F). Where, F = 0.5 for PS and ABS etc. = 0.4 for PE and PP etc.
Thus Shot Capacity = Swept Volume of Cylinder ´ F.
2. Plasticizing Capacity
Plasticizing rate is expressed as the number of pounds of material that the machine can bring per hour or grams per hour. Polystyrene is the standard material taking for calculations. The plasticizing capacity is a function of the heating capacity of the machine and hence the amount of material that can be brought to moulding condition in a given time is dependent upon the moulding temperature necessary and the specific heat of the material.
Plasticizing rate with material A = Specific heat of A /Specific heat of B X Moulding temperature of A / Moulding temperature of B.
If the total heat content per / lb or per / gram or kg. of the material is known and is equal to Q , (B.Th.U or J) the plasticizing rate may be determined from;
Plasticizing rate with material B = Plasticizing rate with material A ´ Qa / Qb.
It is necessary, therefore that the moulding machine selected should be capable of plasticizing sufficient material to maintain the moulding cycle expected with the tools, and this may be determined from ; Plasticizing rate kg /lb / hr = Weight of moulding (kg / lb) X Number of moulding per hour.
For maximum efficiency it is generally considered that an injection press should not operate at above 80% of its rated performance as either shot weight or plasticising capacity.
To calculate the quantity of heat Qc (B.Th.U) or (J / Kg ) to be extracted from mould per hour, the formula is;
Qc = M(Cp(T1-T2) + L) where,
M = Mass (Ib / Kg ) of plastic material injected per hour into the mould.
Cp = Specific heat of material.
T1 = Injection temperature of material (°F or °C)
T2 = Mould temperature (°F or°C)
L = Latent heat of fusion of material (B.Th.u / lb or J / Kg )
Then Qc = Alternatively, if the total heat per pound or per kg. of the plasticised material is known then;
Qc = MxAwhere,
M = Mass of plastic material injected in to the mould (Ib or kg)
A = Total heat content in B.Th.u/ lb or J/ kg. of the plasticized material.
3. Clamping Force
The clamping tonnage of the press controls the maximum projected area of moulding that can be produced. The injection pressure exerts with in the mould cavity is a force which tends to open the mould. This force is proportional to the projected area of the moulding and runner, and must be opposed by the clamping force. Only a proportion of the pressure produced by the injection cylinder is transmitted to the cavity, various losses occurring in the heating cylinder, nozzle and gate. The actual cavity pressure to be counteracted by the clamping force is, only a fraction of the injection gauge pressure, and it is usual to take this fraction as between 50% - 33% so;
Clamping force = Projected area of moulding including runners ´ 1/2 -1/3 of Injection pressure.
4. Injection Pressure
The exact proportion of injection pressure to be adopted is dependent upon the thickness of the moulding section and the ease of the flow of moulding material used. Thin and uneven section require a high injection pressure to fill, and need more clamping force.
Injection pressure may be found from the formula,
injection pressure = Injection hydraulic line gauge pressure ´ di 2 ¸ dp2
Where, di = Diameter of injection cylinder
dp = Diameter of heating cylinder ram
As mentioned earlier the injection pressure necessary on the machine is dependent upon the section thickness, length and size of runners, gates, and the material to be employed.
It is quite frequent practice however to fit where necessary a machine with a special high pressure injection cylinder. This is done by reducing the diameter of the ram and the base of the heating cylinder, thus increasing the specific pressure although it will reduce shot capacity.
5. Ejection Force
The ejection of the moulding is performed by the ejector pins, core ejectors, plate ejection or by air ejection. These ejection units are secured to and operated by, an ejection plate or grid with in the mould. Pneumatic ejectors are incorporating for multi colour insert mouldings to facilitate additional ejection between cycles as well as for large mouldings like luggage shell, to release vacuum sticking to the core.
The ejection force determines mainly based on the following factors. (1) Area of contact. (2) Surface quality (3) Shrinkage. (4) Vacuum formation. (5) Flexibility of the material. (6) Under cuts. (7) Draft for the core. (8) Stiffness and rigidity of the moulding. (9) Ejection unit balance. (10) Condition of machine.
To find out ejection force a number of formulas are available. But when considering the above points a clear value is impossible to achieve especially in the case of vacuum sticking where a slight passage of air is enough to release the total ejection force.
MOULD COOLING
It is necessary to reduce the temperature of the hot plastic material injected into the mould cavity to a point when the material freezes into a sufficiently rigid state to allow the moulding to be extracted. Thus the temperature of the mould must be maintained sufficiently low to cause the hot material to give up both its sensible and latent heat of fusion to the tool surfaces. Cooling time increases in proportion to the wall thickness and size of the moulding. If the heat input to the tool from the hot material is greater than can normally be dissipated by the mould through conduction, etc, then other means have to be introduced to remove the excess heat. Such additional heat removal is usually doing by water cooling, warm oil cooling, and by high pressure air cooling.
Cooling doesn't mean that mould temperature should be brought down to minimum possible. To set best result and reduce post moulding shrinkages etc. a particular temperature should be maintained depending upon the plastic. For those values refer the table No.8 at the end ot this part
Water Cooling
Most of the moulds are water cooled; the water mixed with anticorrosion chemicals, being directed through passage provided in the mould.
All the injection moulding machines have valves for water, and these are connected to the inlet and outlet of the mould by means of flexible pipes, the valves being adjusted to control the flow of water to maintain optimum mould temperature. Water cooling allows an increase in the production rate, especially when the shot weight-moulding weight ratio is high. Cooling circulation passages can be made either by drilling, by milling slots between plates, by copper tubing or by making partition for center bores.
The following particular points should be observed by mould designer.
2. Air Cooling.
There are occasions where water cools too rapidly or water cooling is difficult to apply to particular mould piece. In such case air cooling at standard air line pressure (6 to 10 bar) may be used.
3. Oil Heating/Cooling.
A number of thermoplastic materials like PMMA, PA, PC, POM, PBT etc. will not mould satisfactory in cold moulds, and hence the tool temperature must be raised before sound moulding can be achieved.
This can be done by continuing to inject the material until the mould temperature rises, but this is slow and wastage of time. So external method of heating the mould to the operating temperature are adopted.
This heating may be effected electrically or employing strip or catridge heaters similar to those used for compression mould heating and operated at main voltage.
Nowadays portable mould heaters known as temperature - controllers are very popular which not only raise the mould to the required temperature but also hold this temperature to the close limits now demanded by high class moulding technique. The controller normally comprises a unit in which the heating liquid (oil or water) is heated and pumped to the mould the same way as explained earlier.
Mould temperature is very important to avoid post moulding shrinkage.
4. Mould Cooling Time
S = t2/2pa log e [p (Tx-Tm) ¸ 4 (Tc-Tm)] where,
S = Minimum cooling time in seconds.
t = Thickness of moulding (in or cm)
a = Thermal diffusivity of material (in2 / s or cm2 /s)- refer table No.25
Tx = Ejection temperature of moulding (ºF or ºC)
Tm = Mould temperature (ºF or º C)
Tc = Cylinder temperature (ºF or °C).
p = 3.14
Melt Processing
Different materials have different processing parameters and tips. Here Delrin a polyacetal, one of the latest material is taken as an example, which require special care. Acetal resins may be processed without difficulty on conventional injection moulding, blow moulding, and extrusion equipment. The main points should be noted are:
Both homopolymers and copolymers are available in a range of molecular weights 20,000 - 100,000. The material are normally characterized by the melt flow index (MFI) using basically the same tests as employed for polyethylene. For high precision work and complex moulding low molecular weight polymers should be used (MFI as high as 27). For general purpose work MFI of about 9 are employed. For extrusions and thick walled moulding a polymer with MFI about 2.5 (molecular weight 45,000) is often employed, although for extrusion blow moulding the special polymers used have an MFI of about 1.0.
Acetal is a crystalline polymer which requires a greater heat input for melting than amorphous resins. This additional heat is needed to destroy the ordered crystalline structure of the solid, and it is called the heat of fusion.
EQUIPMENTS FOR INJECTION MOULDING
1. Heating Cylinder
To deliver the necessary amount of uniformly melted resin of good quality, the adapter, non-return valve (screw check valve), screw, and cylinder must be properly designed to ensure maximum streamlining. This is necessary to avoid hold-up of resin, which will lead to resin degradation. Relatively insignificant hold up spots can cause degradation and a reduction in quality of the parts moulded. Poor seating or matching of diameters as well as poor maintenance can also cause hold up spots.
2. Nozzle
The nozzle of the open design (not shut off) are suitable for acetals. The heater bands should extend as close to the nozzle tip as possible and cover as much of the exposed surface as practical to counteract loss. It is particularly important to cover the small orifice by heat bands, where the material separation occurs. If a thermocouple is used the well should be located over this orifice. Improper location of heater bands of thermocouple will results in over heating of certain areas in an effort to prevent freezing of the tip.
Screw decompression or suck back is frequently used to make control of drool easier with these open nozzles. This feature is available with most machines.
3. Non-Return Valve
Although shut off nozzle have been used successfully with acetals they tend to cause hold up of resin which results to brown streaks or gassings especially after some wear has occurred in the moving parts of the nozzle. The non-return valve or check ring prevents melt from flowing backward during injection. A non-return valve should meet the following requirements:-
1. No hold-up spots. 2. No flow restriction. 3. Good seal. 4. Control of wear.
4. Adapter
The adapter have a standard tapered short cylinder sections to match with the cylinder as well as the nozzle inner diameters and it is the intermediate between the nozzle and cylinder. In addition to its mechanical functioning of reducing the diameter, the adapter acts to isolate the nozzle thermally from the front of the cylinder for better control of nozzle temperature. It also protect the cylinder from damaging that can occur due to frequent change of nozzles, and it should be out of thermally stable good quality medium hardened steel.
5. Screw
The length of the screw will affect the melt quality and consequently the output usable for good parts. The preferred length is about 20 times the screw diameters (L /D = 20/1) or 20 turns when the pitch and diameter are equal. The screw should be divided as follows 45 - 50% (9-10 turns) feed section. 20 - 30 % (4 - 6 turns) transition section and 25 - 30% (5 - 6 turns) metering section. Normal division of screw is 10 - 5 - 5. In the screws less than 16 turns, the feed section should have 7 or 8 turns.
The shallow metering high compression ratio screws suggested for acetals are designed to increase the heat input by mechanical working of the resin. Since the energy for this increase comes from the screw motor, additional horse power must be available if an increase in melting capacity is to be realised. The suggested screw also have to be operated at a higher RPM to deliver equal or greater melt output during a specified screw retraction time, because the amount displaced by one turn is less. Neither a general purpose nor high compression screw should be operated at rotational speed so high that unmelted particles or degradation occurs.
Usually the moulding machine injection unit chosen so that the shot size is 50% or less of the injection stroke. For thin parts moulded at more than four shots per minute, as little as 10 - 20 % of injection stroke capacity may be used to obtain adequate melting capacity. On the other hand for thicker parts moulded on long cycles more than 50% of the stroke may be used. These considerations determine the average holdup time of the resin in the moulding cylinder.
6. Cylinder Temperature
Inter zone temperature control should be used and thermocouples should be placed near the centre of each zone. Burn out of one or more heater bands with in a zone may not be apparent from the temperature controllers, so some moulders have used ammeters in each zone to detect changes. In latest machines PID temperature controls are available which can give an accuracy of ±1.5°C.
7. Injection Rate
The moulding machine should be able to inject its rated capacity in less than 2 seconds with lower viscosity acetal resins. Highly viscous acetals may have slower fill rates. Control of injection rate, however will often be necessary to correct certain molding problems; a slower injection rate may be required to prevent warping or jetting of resin into some cavities. Now a days latest machines have the facility for two stage injection ie, initially with low clamping force to release any gas or air, then with high clamping force to prevent flashes. Latest machines have an injection time setting range of 0.1 second and screw position digital indicator range of 0.1mm.
8. Clamping Force
The force required to hold mould closed against injection pressure depends on;
Most well built moulds can be adequately clamped if the machine has 48-69 MPa (3.5-5.0 tons / in2) based on the projected area, since the injection pressures are seldom over 100 MPa (14,500 Psi) and fill rates are moderate. Higher available clamping pressure is preferred and will give more freedom in choosing the most suitable molding conditions for some molds. Very thin, long flow parts may require clamp forces as high as 100 MPa (7 tons / in2 ) because extremely fast fill rate and high injection pressures may be required.
START UP AND SHUT DOWN PROCEDURES
1. Start Resin Change/Purging
The following procedure is designed to prevent over heating of the resin and contamination of the cylinder with material from previous runs.
Before loading the acetal resins to the hopper the cylinder which contains another resin must be purged at temperatures above the melting temperature for the other resins with a clear PS or natural colour low melt index PS (MFI 1-2) until the cylinder has been cleared. The cylinder temperatures should be then to be adjusted to 205ºC (400°F) while continuing to process the purge resin through the machine. When the cylinder has reached 205°C acetal resin can be added to the hopper. After the purge resin has been cleared from the cylinder, the moulding operation with acetal may begin.
Both PS and PE are chemically compatible with acetal resins where as PVC is not. Contamination of acetals with such foreign materials can cause objectionable odour or even a violet blow back. Very thorough purging is necessary to remove the last traces of PVC from the cylinder. In the worst cases like after glass reinforced resins or severe degradation of previous material, it may be necessary to pull the screw and clean the equipment manually to prevent contamination of the mouldings.
2. Temporary Shut Down
A moulding machine with acetals in the cylinder at operating temperatures should not be allowed to stand idle. When it is necessary to interrupt cycle for a minor repair, it is good practice to take periodic air shots or shut the hopper feed gate and empty the cylinder and screw, if the interruption will be more than a few minutes. The cylinder temperature should be reduced to about 150 °C (300 °F), if the interruption is prolonged.
3. Normal Shut Down
The best practice is shut off the hopper feed gate, turn off the cylinder heaters leaving the nozzle heater on and continue moulding or purging until the cylinder became empty. The machine is then turned off with the screw in the forward position and is ready for reheating by the procedure mentioned earlier. If another resin will be moulded next, the acetal should be purged from the cylinder with PE or PS
4. Start Up After Emergency Shut Down
In this case the screw may be full of materials which may bo cooled slowly and was exposed to melt temperature for a prolonged period. The screw may even be in retracted position with large quantity of material in front of the screw. In order to vent gases from resin that may be degraded, it is essential that the nozzle be open and heated to operating temperature and the material in this area be completely melted before the cylinder reaches melt temperature. The cylinder zones should be heated to an intermediate temperature below the melting point of jammed material and the machine allowed to equilibrate at that temperature. Cylinder temperature of 150-175 °C (300-350 °F) are suggested for acetals. After all zones have been at this temperature for 30 minutes, cylinder temperature should be raised to 195 °C (380 °F). As soon as the material has melted it should be purged with fresh materials. The partly degraded purged acetal should be placed in water if it emits an odour.
5. Cylinder Temperature
Acetal resin is a crystalline material with a melting point 175 °C (347 °F) for homopolymer and 163 (325 °F) for copolymer. The resultant melt temperature should usually be in the range of 205-225 °C (400-440 °C) for homopolymer as measured with needle pyrometer in melt purged from the cylinder on cycle. The actual cylinder temperature settings to achieve this melt temperature will depend on the design of the cylinder and screw, screw back pressure, screw rotation speed, shot size and cycle time. The settings will frequently be 5-10 °C (10-20 °F) lower than the actual melt temperature because of the mechanical heat of the screw. When the cycle is short and melt output is high, higher temperature settings may be required. Similarly when cycle is long and melt output is low, lower settings, especially in the rear zone may be used.
In latest machines provisions are there for very accurate settings and for repeated operations using stored data . The incorporation of monitor and control unit in a machine have the following features.
The proper design and operations of heating, cylinder component are intended to provide a homogeneous melt of uniform temperature. The uniform melt crystallizes uniformly, as can be shown by microstructural analysis, and produces a structure with minimum internal stress. Uniform melt also promotes uniform mould shrinkage.
6. Thermal Stability of Acetals
Acetals has very good thermal stability. If the resin is overheated decomposition to formaldehyde can cause splay marks in the moulding and bubbies in the melt. Degradation also cause yellow or brown discolouration. The rate of decomposition depends on both temperature and time. Contaminants and impurities have an adverse effect on thermal stability and it can be from improper purging also.
Fig. 1. Effect of Temperature on Hold up Time of Acetals.
7. Back Pressure
Increasing back pressure increases the work done by the screw on the melt. This in turn, increases the melt temperature and its uniformity. Higher back pressure may be used to eliminate unmelted particles and to improve colour mixing when colour concentrates are used. Increasing back pressure, however decreases the output of the screw, and it tends to reduce glass fibre length and change properties of reinforced resins. Back pressure should be used only when increasing cylinder temperature or other changes are not effective or not possible. The maximum permitted back pressure for acetals is 200 bar.
8. Injection Pressure
Normal injection pressure for acetal resins is in the range 750 -1500 bar. High injection pressures are used to fill long flow thin sections and to reduce shrinkage. To get maximum toughness and elongation an injection pressure of 80 - 100 MPa (11,600 to 14,500 psi) may be required to fill highly viscous acetals. Injection may be limited by mold construction. Insufficient support will also result in fin or flash.
Although single stage injection pressure is frequently used for molding acetals. two stage injection is sometimes useful to accomplish both complete filling and yet avoid flash, sticking to the cavities etc. Misuse of two stage injection such as excessively high and prolonged first stage pressure can cause moulded in stress near the gate. The injection pressure is controlled by a relief valve that limits the maximum oil pressure in the screw.
9. Injection Rate
The optimum fill rate for a part depends on its geometry, the size and location of the gate, type of gate, number of cavity, mould temperature, and melt temperature. When moulding thin sectional parts high injection rates are usually required to fill the parts before it freezes. Higher and more uniform surface gloss can be obtained if the injection rate is fast enough to allow the cavity to be filled before the resin begins to solidify. Low injection rate can reduce jetting and gate smear. Warpage to certain extend can be adjusted by injection rate. When molding thick parts a slow injection pressure is essential to delay freezing of the gate and allow packing for the maximum time.
The injection rate is controlled by the flow control valve that regulated the rate of flow of oil to the injection hydraulic cylinder. In latest machines the injection can be programmed and it is available in the range 0.1 grams .
10. Moulding Cycle
The moulding cycle is made up of several parts and the major elements of cycle are a) screw forward time b) hold time. c) mold open time.
Screw forward time includes injection time plus the time that the screw is held forward by hydraulic pressure. During molding time, the screw rotates and retracts, and the mouldings cools sufficiently to be ejected when the mould opens. In an ideal case the moulding cycle will be determined largely by part thickness.
Fig. 2. Moulding Cycle Chart
The screw forward time which is a function of part thickness and changes slightly with mould temperature, will be long enough for the gate to freeze. This results in maximum part weight, minimum mould shrinkage, and minimum tendency to form sinks or voids. In some cases, mechanical properties, especially elongation will be greatest when screw forward time equals or exceeds gate freezing time, there is usually little need for additional cooling time, so the hold portion of the type only needs to be long enough for screw retraction. However when cooling time must be longer screw retraction time should be extended by slowing screw rotation to occupy most of the available cooling time. This tends to give better melt and colour uniformity.
Calculation of cycle time
T =tM+tE+tN+tC+tPa ¸ tK
or
T = tE+tN+tPI where,
T = Cycle time
tM = Machine movement time
tE = Injection time
IN = Holding pressure time
tC = Set cooling time
tK = Effective cooling time = tC+tN
tPa = Time for pause
tPI = Time for plasticizing
Fig. 3. Screw Forward Time for Gate to Freeze
At the end of injection, mould protrusion can be done provided if there is provision for mould and machine. The gate cut off using ejector unit in a two stage ejection mould, not only produce a clear component but also prevents any sinking due to voids that can be formed on thicker parts at the injection point; however, it is applicable to only to direct and overlap gated moulds.
11. Mould Temperature
Acetals can be molded successfully maintaining temperature between 40-120 °C. However as a standard value of 80-105 °C can result into obtain a moulding of maximum dimensional stability, flow, gloss and minimum moulding stress. Moulding out of low temperature moulds have high strength and is recommended for heavy moulding and thicker parts. Similarly minimum temperature as low as 10 °C is recommended for thin parts (as thin as 0.8 mm ) out of lightly viscous materials to give maximum strength. If the resin is of improved melt flow, faster and easier fill is possible and the tendency to wrap is less. If it have high lubricity, easier ejection and low wear for mould can result. Reduced sensitivity to slight variation in moulding conditions can produce more uniform moulding, fewer rejects, and considerably fewer cycle interruptions and faster set up rate is necessary for a earlier ejection of the part.
12. Reground Resin
Successful use of reground resin depends upon the following factors.
ECONOMICAL PRODUCTION OF PARTS
1. Quality Parameters of the Part
Critical quality parameters of a part can be part weight, dimensions, tolerances, finish, flatness etc. For practical reasons it is desirable to check the parts shortly after they are out of the mould to determine the relative effects of moulding variables with a minimum time loss. However, it should be noted that a mould dimension will change as the part is cooled and for a part if the dimensions are critical it should be checked only after 24 hours at 20°C. If the moulding is to use different conditions it should be immersed in cold water. The water absorption can change part weight and dimensions. So a dry dimensions chart and a wet dimensions chart has to be prepared for the customer approval always. Similarly parts moulded at different parameter settings are to be recorded and kept in quality control department or production department. For example, fine tuning of process variables such as injection pressure may enable you to bring a part within dimensional tolerance at a faster cycle than seemed possible. In latest machines such parameters can be stored in the machine itself, or in diskettes or can be transferred to PC.
2. Periodic Inspection Of Equipment Operations
In order to obtain maximum moulding results all parts of injection moulding machine should maintian recommended settings and it should function properly. Frequently, an equipment problem can be easily corrected, which will allow to attain optimum level of productivity and it is very essential if the machine is an old one. In latest machines this failures will intimate on monitor or by alarm.
3. Start Moulding On The Established Cycle
Begin moulding in the usual cycle using old production records. If the machine is a programmable type it will make the work easier. Care should be taken to misload the mould, if there are more than one mould for a particular part and also if it is an interchangeable cavity type. If the material is an higher flow type, it is advisable to reduce injection pressure by 10-20% on the first series of shots to avoid flashes.
4. Keep Low Mould Open Time
The mould should remain open just long enough to allow the parts and runners to drop. Low pressure close protection should be always used to prevent banging of mating parts. The opening stroke should be as short as possible and techniques such as airjet or robots can be incorporated, to accelerate the extraction or to protect the part from damages. If the mould is three plate construction or two stage ejection type with core protrusion etc, springs or rubber bumpers should be used in between the plates to avoid banging. If the mould have cams, cores etc. it should be operated at a lower speed fitted with coupling or other safety measures.
5. Minimize Injection Time
In order to get a better part of better quality the gate should freeze at the end of injection. The gate will start to freeze as soon as the melt has slowed or stopped flowing to the melt cavity. Therefore a faster injection contributes to minimum gate freeze time. The high volume pump, should normally be used to fill the cavity rapidly. The screw travel time usually depends on the booster time and the first stage injection pressure. Pumping time or booster time should end before the cavity is filled. In latest machines it is possible to set the injection time in the range 0.1 sec.
6. Maximize Injection Pressure
The injection pressure should normally be raised to the maximum level that does not cause the mould to flash, provided that the mould is adequately supported, correct dimensions and thickness of plates are maintained and necessary clamping pressure is maintained.
7. Reduce Hold Time
Hold time can be reduced to equal to the screw retraction time. Screw RPM can be increased to minimize screw retraction and hold time. With well designed and maintained, shut off nozzle, hold time might be reduced further, since the mold can be opened and the parts ejected while the screw is still retracting.
8. Adjust Mould Temperature Controller
If the mould temperature is maintained using hot fluid, when the cycle time reduced, the mould surface temperature can go up. Generally this temperature will balance because the material residing time is less. If not, the controller value or temperature has to be adjusted accordingly. In latest machines this value normally be indicated on the monitor and adjust automatically.
9. Minimize Screw Forward Time
When the hold time has been minimised, and if the parts are still with in specifications, injection hold time can be reduced in steps. Again careful records should be kept and samples should be attached for future reference. The minimum injection hold time is the shortest time, related to cycle time, in which acceptable parts are still ejecting smoothly. Further reduction can lead to deformation or penetration to the parts on ejection, or failure of the parts to hold desired dimensions and flatness. In such condition mould temperature have to be readjusted to balance the above problems. Quality parameters in each change should be checked because too short screw forward time may increase mould shrinkage, warpage or, under some conditions, reduce toughness.
10. Operation On New Cycle
Run the machine for about half an hour and periodically check the critical quality parameters of the part before the machine put to continuous production.
11. Enter New Cycle In Records
At the end of production keep the record of the best results based on part acceptance because the main object is production of higher quality product in reduced time, not reduction of time. The cycle records can be stored in the machine or in diskettes or can be directly transferred to a PC, if the machine have provisions.
In order to attain maximum advantage of above improved processability, it is advantageous to consider the following areas;
1. Resin Supply
The resin should be free from contaminates and other impurities and it should be as pure as possible or only permitted reground should be added. It should be pre-dried as specified.
2. Mould Operation
The maximum advantage of high productivity moulding can best be attained with automatic mould operation; CNC machines makes this into practical.
3. Mould Temperature Control
Automatic temperature control for mould is necessary for quality production. When the mold runs at faster cycle it heats up even if there is cold water cooling. In order to obtain a perfect temperature the cooling time or cooling temperature should adjust accordingly.
4. Mould Venting
Venting of mould is critical to part quality. As the cycle time is reduced faster injects put greatest load on vents. The trapped air must rush out the mould freely as the melt fills the cavity. Proper venting should also help mould corrosion and deposits. If the machine have two stage clamping facility as in compression moulding machines the above problems can be eliminated by releasing the gas between the matching plates.
5. Mould Runner System
When the mould planned for faster cycle, a smaller runner and comparatively smaller gate is enough. Another way is to reduce runner wastage is by incorporating extended heated nozzle. By reducing the sprue and cold slug diameter, the cycle time can be reduce because a smaller cold slug at the sprue puller will freeze rapidly. If the volume requirements is very high, runnerless system is ideal, mould protrusion technique is successful.
SAFETY PRECAUTIONS FOR MOULDING ACETAL RESINS
To avoid decomposition of acetals, the resin should be exposed to melt temperatures near the hold up time limits; ie, not more than 20 minutes at 230 °C (450° F). If there is any doubt the temperatures should be checked with a hand pyrometer.
Vapours from the decomposition of acetals are largely formaldehyde, the same as from common thermosetting resins such as MF, UF and PF. Measurements made around an injection moulding machine showed that formaldehyde vapour concentrates is less than 1.0 parts per million (PPM) for acetals. The maximum permissible PPM is 3 PPM for 8 hours, for formaldehyde vapours. The acceptable ceiling concentration is 5 PPM and acceptable maximum peak above the ceiling concentration is 10 PPM for 30 minutes. Since formaldehyde is detectable at 1 PPM, and it will irritate in both eyes and nose at 3 PPM there is little chance for continuous exposure. In normal case the shop should have good ventilation or large space.
Overheating of the moulding cylinder, long holdup at normal temperatures, or contamination from foreign materials can cause objectionable odour or even a violent set back. Should this ever happen, the injection cylinder heat should be turned off, if possible, the decomposed material should be purged from the cylinder rapidly after the injection pressure is reduced and the booster turned off to avoid splattering. Continuous purging with polyethylene helps to cool the cylinder. Over heated or decomposed melt should be dropped into a pail of water.
MOULD SHRINKAGE
The mould shrinkage of acetals depend on the following factors.
As shown in the graph the shrinkage value of a general purpose medium viscous acetal is derived from a moulding setting as mold temperature 93°C (200 °F), injection pressure 112 MPa (1142 bar) (16,240 psi), and a melt temperature of 210 °C (410 °F).
Two other assumptions made in this monograph are the gate is designed with minimum gate thickness equal to one half of wall thickness and that screw forward time is at least equal to the time required for the gate to freeze. A factor of 0.1% should be added to mould shrinkage estimate for an increase of 14°C (25 °F) in mold temperature or subjected for a similar decrease. A factor of 0,04% should be substracted from the mould shrinkage estimate for each 7 MPa (72 bar) increase in injection pressure.
A straight line connecting a part thickness of 3 mm on line 1 to a gate area 4.5 mm2 (gate size 1.5 x 3mm) intersects at 2% ; the estimated mould shrinkage at a mould temperature of 93 °C (200 °F). or,
A straight line connecting part thickness of 3mm(0,12") on line 1 to a gate area of 4.5 mm2 (0,0072" sq inch) or a gate size of 1.5mm (0,06") deep 3mm wide (0, 12") on line II interests line II at 0,020 mm/mm (0, 020in/in), the estimated mould shrinkage at a mould temperature of 93°C (200°F) in the case of POM (Delrin).
Moulding acetals with a screw toward time less than the time required for gate seal can cause a large increase in mould shrinkage. This moulding technique is sometimes used when maximum properties are not required but it is not possible to give a specific correction factor. This increase in shrinkage may vary from 0.1% to 1% depends on the amount of screw forward time, although this increase is often from 0.2% to 0.5%
In practice actual mold shrinkage may vary from estimated from the monograph for the following reasons.
1. Post Moulding Shrinkage
When mould shrinkage occurs in cavity and part reaches room temperature, further shrinkage may occur as time passes. This post-moulding shrinkage is irreversible and it is determined by cooling rate that is, by mould temperature and part thickness. Hot moulds 93ºC (200ºF) or higher measured in the cavity surface reduce post-moulding shrinkage in an almost negligible amount.
ANNEALING OF MOULDINGS
Experience has shown that the use of hot moulds can eliminate the need for annealing. In figure 02 in part 3 showed that dimensional stability of parts molded at 121º C (250ºF) approached that of annealed parts. Only when the most exacting dimensional tolerances are required and prolonged service at elevated temperature will be experienced, annealing is required to improve dimensional stability.
Annealing may be used for correcting over sized parts. The amount of additional shrinkage can be adjusted by varying the temperature and time of the annealing treatment.
Annealing may also be used to relax internal stresses that may be induced by uneven cooling, or sometimes for alleviating warpage, where this problem may be uncontrollable in molding operation. Parts of complex geometries having structured members of widely different wall thickness may have a high level of stress despite can be reduced by the use of high mould temperatures. Annealing may be useful for reducing such stress in the critical areas of such parts where excessive injection pressure cause over packing with attended stress areas, annealing may improved the impact strength in these areas.
1. Annealing Procedure
Annealing of acetal resins may be conducted in air or oil. Air annealing of acetals is best conducted in an air circulating oven maintained at 160°C ± 3 °C (320 °± 5 °F). When the oven temperature returns to this temperature after the parts are put in the oven, 30 minutes, should be allowed to achieve uniform temperature in the part and then 5 minutes additional annealing time per 1 mm (0,04 in) of wall thickness. Times became excessively long to obtain equivalent annealing at temperatures below 160 °C.
Some annealing may occur when hot moulding are packed in boxes immediately after molding, because cooling may be prolonged. Although this technique may be used deliberately, more often it is accidental and may cause excessive shrinkage. A brief cooling period before packing will prevent undesired annealing shrinkage.
Parts may be annealed in high boiling, inert mineral oils such as "Primol 355, "Chevron" # 15 and Nujol or Primol 342 "Majoline 238 CRA or ordina 33". Annealing time in oil at 160 °C, is 5 minutes per mm of wall thickness after the parts reached annealing temperature. Annealing of lower temperature 152°C (305 °F) will require several hours or more to obtain the same dimensional change. Thorough agitation should be provided to assure uniform bath temperature and to avoid localized overheating of the oil. The latter condition may cause deformation or even melting of the parts.
2. Cooling Procedure
When either air or oil annealed parts are removed from the annealing medium, they should be cooled slowly to room temperature in an undisturbed manner. Stacking or piling of parts that could be deformed while they are hot should be delayed until parts are cool to the touch. A temperature step down of 45°C per hour is recommended as a standard value.
ENVIRONMENTAL CHANGES
Dimensions of acetal will change with environmental temperature and absorption of water. In figure 5 the changes of general purpose medium viscous acetals are shown. The graph prepared with respect to moisture (% RH) and immersion in water. So when selecting the materiel for particular application these factor should be taken into account seriously.
From the monograph it can be seen that at rise in temperature and relative humidity, the environmental changes are higher for acetals. The monograph shows that at 100 % RH and 60°C use temperature the variation in length is 0.8% .
Polyether ether ketone have excellent heat resistance and electrical charactaristics similar to PE and similar fluoro plastics.lt also withstand 50,000 hours exposure at 150°C,has low flammability with limiting oxygen index of 35% generates an exceptionally low level of smoke and has good resistance to water at 125°C,under which conditions other heat resisting materials such as the aromatic polyamides are liable to fail.Water absorption of PEEK for 24 hours at 40% RH is only 0.15%.Other specific features are excellent gamma radiation resistance and good resistance to environmental stress cracking.
Preliminary indications are that, PEEK has superior heat resistance to PPS and it is the highest rated thermoplastic in terms of heat resistance.lt is also tough and more expensive. It can be injection moulded and can be used in chemical plants may be regarded as the ultimate in heat resistance among currently available melt processable thermoplastics. It can withstand a service temperature of 440°C for more than 1 hour.
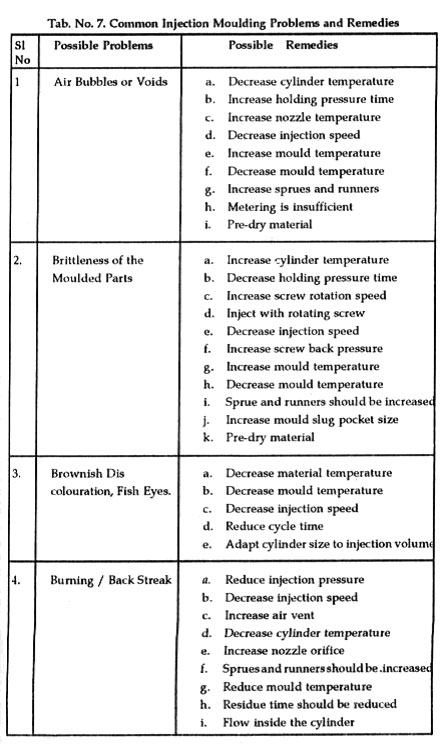
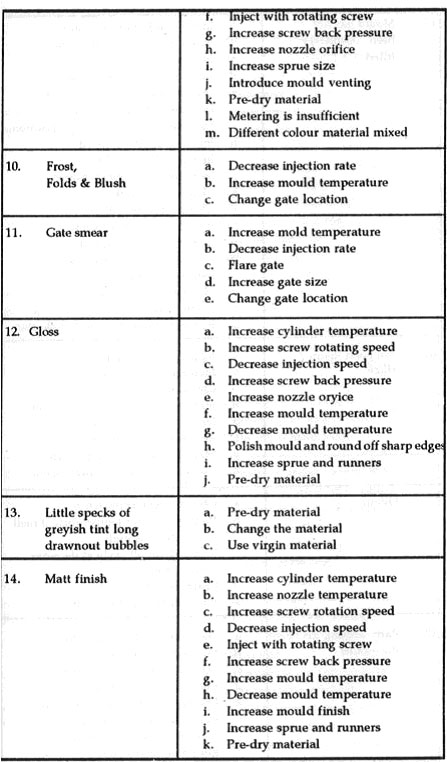
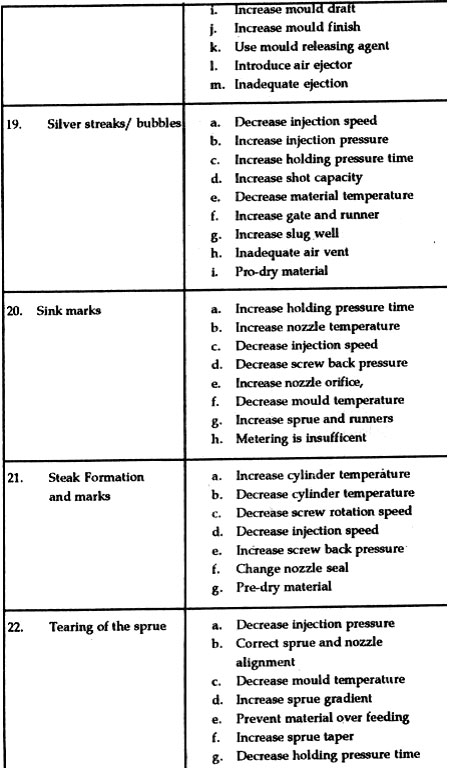
Injection moulding is the most important, fast, economical and widely accepted plastic processing method applicable for thermoplastics thermosets and elastomers.
1. Thermoplastic Materials
Soften and plasticise the raw material, which are generally in the form of granules, by applying heat energy and inject the mass into a mould cavity and then remove the heat by seperate cooling arrangement provided with in the mould. The important materials which can be sucessfully injection moulded.
2. Thermosetting Materials And Elastomers
Inject a pre-processed plastic mass and then vulcanize the material in the mould by the application of heat and pressure. The screw in this case should have a central bore and must be water-cooled.