SILICATE GLASSES
The silicate glasses are technologically and commercially the most important of the oxide glasses. They constitute more than 95 per cent of the tonnage of glass manufactured, and of this the greater part falls within the relatively small composition range of what are usually termed soda-lime-silica glasses. The compositions of these glasses are more complex than the term suggests, since, in addition to the oxides Na2O, CaO, and SiO2, they often contain some MgO, which improves their resistance to devitrification, and Al2O3, which improves their chemical durability. However, most of the points of scientific interest relevant to silicate glasses may be made by considering simple systems such as the binary alkali silicate systems and the ternary system, Na2O-CaO-SiO2.
A. BINARY SYSTEMS
1. Alkali Silicate Systems
A. Structural considerations
In previous chapter we saw how in Na2O-SiO2 glasses, the introduction of Na2O results in the formation of "singly-bonded" or "non-bridging" oxygen atoms, i.e. oxygen atoms linked to only one silicon atom. The sodium ions fit into the structure possibly in the way shown in Fig.5 and are linked to the surrounding oxygens by bonds which are much more ionic and also much weaker than the silicon-oxygen bonds. Thus the structure of the sodium silicate glasses is weaker than that of vitreous silica, as is shown by the higher expansion coefficient and lower viscosity which results when Na2O is added.
As the Na2O content is increased, more and more non-bridging oxygens are formed until eventually the material consists of isolated SiO4 tetrahedra linked together by ionic Na-O bonds. By analogy with the structures of crystalline silicates, one may expect this type of structure to be formed in the melt at the composition of the orthosilicate Na4SiO4, i.e. when the Na2O/SiO2 ratio is 2/1. Crystallization of this melt is likely to be very rapid. The fracture of strong Si-O bonds is not required for reorientation of the tetrahedra from the irregular arrangement in the melt to the regular arrangement in te crystal, i.e. the mechanism of crystallization will be non-reconstructive. The orthosilicate melt does not in fact form a glass.
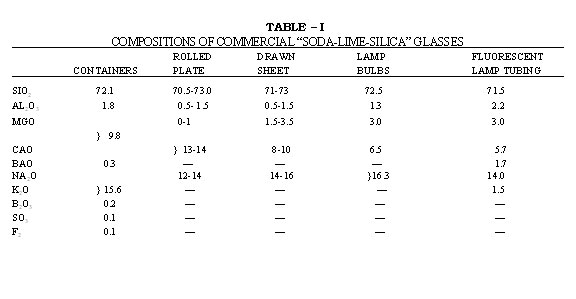
Indeed glass formation does not occur at all readily at the metasilicate composition, Na2SiO3. At first sight this may seem a little surprising. Grund has shown that the crystalline compounds Na2SiO3 and Li2SiO3 both have structures containing infinite chains of SiO4 tetrahedra, in common with many other crystalline metasilicates. It is impossible to say with any certainty what kind of groupings of tetrahedral are present in the melt but it is more than likely that there are chains and/or closed rings of tetrahedral, the latter type of grouping also being found in a number of crystalline metasilicates. Whatever the melt structure may be, it is likely that the process of crystallization will involve the fracture of at least some Si-O bonds, i.e. the process will be reconstructive. In spite of this a glass is not easily formed.
It is instructive to compare the behaviour of the metasilicate with that of sodium metaphosphate, NaPO3, which forms quite a stable glass. Here we have a much clearer picture of the nature of the crystallization process. It is known that the melt contains long chains of PO4 tetrahedra whereas the crystalline material contains trimetaphosphate anions, which consist of closed rings of tetrahedra. The crystallization of this material is clearly a reconstructive process. Thus although both crystalline compounds, Na2SiO3 and NaPO3, have structures in which each tetrahedral group shares two corners with its neighbours, the glass-forming ability is quite different. It is likely that the different stability of the glasses can be explained in terms of the widely differing melting points of the two compounds, Na2SiO3 melting at 10880 and NaPO3 at 6250. Even if the mechanisms of crystallization were identical and involved the fracture of bonds of equal strength, crystallization of the silicate melt would occur more readily because of the higher temperatures involved. This example clearly shows the unsatisfactory nature of considerations of glass stability which are based solely on an examination of the structure of the materials concerned.
B. Glass formation in the alkali silicate systems
It has been shown by a number of workers that the range of glass formation in the Na2O-SiO2 system is continuous from SiO2 to a limiting composition close to that of the metasilicate Na2O. SiO2. The limiting composition depends on the experimental conditions. As is to be expected, the smaller the melt and the greater the rate of cooling, the higher is the Na2O content at which the material can still be made as glass free from any crystalline material. Among recent workers, Moore, working with 6 g melts, established the limiting composition as 47 mole per cent Na2O. Imaoka, in a general survey of glass-forming regions in simple silicate systems, found it possible to make glasses containing up to 57.8 mole per cent Na2O (58.8 weight per cent) on a scale of 1-2 g. In the corresponding alkali silicate systems K2O-SiO2 and Li2-SiO2, they found the limiting compositions to be 54.5 mole per cent
K2O (65.2 weight per cent) and 35.5 mole per cent Li2O (21.6 weight per cent) respectively. The different results for the Na2O-SiO2 system clearly show the effect of the scale of melting, illustrating the importance of specifying as clearly as possible the melting and the cooling conditions when reporting the region of glass formation in a system.
C. Phase diagrams of the alkali silicate systems
The positions of the limiting glass-forming compositions, as determined by Imaoka in relation to the phase diagrams of the respective systems, show no features common to all systems. It may be significant that the limit in the Na2O-SiO2 system coincides almost exactly with the composition at which Na2O becomes the primary crystalline phase, i.e. the first phase to crystallize
from the melt. At this composition a change will occur in the nature of the crystallization process which will be reflected in the kinetics of the process. The range of glass formation in the Li2O system is much more limited. This may be due to the fact that the liquidus temperatures are appreciably higher than at corresponding compositions in the Na2O and K2O systems. Also, as will be seen later, the rate of crystallization of the secondary phase, lithium disilicate, plays a more important role in determining the stability of the glass than is the case in the Na2O system. The phase diagram data for the K2O-SiO2 system does not extend far enough to include the limiting glass-forming composition.
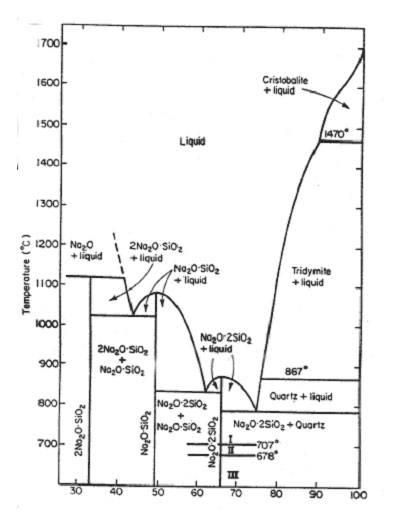
D. The kinetics of devitrification
(i) Effect of composition. The most extensive study of the effect of composition on the rate of devitrification in an alkali silicate system is that of Dietzel who made measurements on twenty compositions in the system Na2O-SiO2 containing 0-42 mole per cent Na2O. The effect of temperature on the rate of devitrification was determined for each glass. The curves obtained were of the usual form showing a maximum rate of crystal growth at some temperature below the
liquidus. The reciprocal of the maximum growth rate, KG max, was used as a measure of the stability of the glass and was termed the "glassiness" (Glasigkeit) of the material, G. Figure 4 shows the variation of log G with Na2O content. The stability decreases markedly in the range 0 to 0.5 mole per cent Na2O. Then in the range above 10 mole per cent Na2O it increases to a maximum at 23 mole per cent Na2O, a composition close to the eutectic between silica and sodium disilicate, Na2Si2O5. There then follows a second minimum at the disilicate composition and another maximum close to the eutectic between sodium disilicate and sodium metasilicate, Na2SiO3. The results were explained in terms of two main factors. One is a steady decrease in stability with increasing Na2O content caused by the progressive breakdown in the continuity of the silica network by the introduction of non-bridging oxygens. Superimposed on this trend is a second effect which gives rise to the low stability at the compositions corresponding to the compounds Na2SiO5 and Na2SiO3. Dietzel and Wickert suggest that at these compositions, there exists in the melt a high proportion of the "structural elements capable of precipitation", i.e. there is a close similarity between the structure of
the melt and that of the corresponding crystal. Hence, crystallization occurs readily. The weakness of this explanation is that it is based on assumptions concerning the melt structures for which there is practically no evidence. An alternative explanation would be to invoke the liquidus temperature effect, i.e. to attribute the maxima at 23 and 38 mole per cent Na2O to the relatively low liquidus temperatures at these eutectic compositions and the minimum at 33 mole per cent Na2O to the higher melting point of the disilicate compound.
Morley has measured the devitrification rates of five Na2O-SiO2 glasses with Na2O contents between 18 and 23.5 mole per cent Na2O, i.e. on the silica-rich side of the SiO2-Na2Si2O5 eutectic. He found that as the eutectic composition was approached the rate of crystallization of the primary phase, cristobalite, decreased until at the 23.5 mole per cent Na2O composition it was less than 1 m / min. At the same time he noted an increase in the rate of crystallization of the secondary phase, sodium disilicate, which begins to form at temperatures below 7600. At 23.5 mole per cent Na2O the maximum rate of crystallization of this phase was about 7 m /min-much greater than the rate of crystallization of cristobalite.
A similar, but much more marked effect was observed in a corresponding series of Li2O-SiO2 glasses containing between 22.7 and 28.3 mole per cent Li2O. At 22.7 mole per cent Li2O, the maximum rate of crystallization of the lithium silicate secondary phase was slightly less than that of the silica primary phase. However, at 28.3 mole per cent Li2O, close to the eutectic composition, crystal growth rates of more than 800 m/min were observed for the silicate phase, and about 60 m/min for the silica phase. Thus the instability of these glasses is due primarily to the high crystallization rate of the secondary silicate phase. Morley found that in both systems, the maximum rate of crystallization of the primary phase was inversely proportional to the viscosity of the glass at the corresponding temperature. He also noted in the Na2O-SiO2 system that the logarithm of the maximum growth rate of the primary phase was proportional to the reciprocal of the liquidus temperature in 0K. However, the rate of crystallization of the secondary phase is not affected by the liquidus temperature, and it is clear that there will be no simple relationship between the stability of the glass and the liquidus temperature when the secondary phase has a high rate of crystallization. In the Li2O-SiO2 glasses studied by Morley the secondary phase begins to appear at 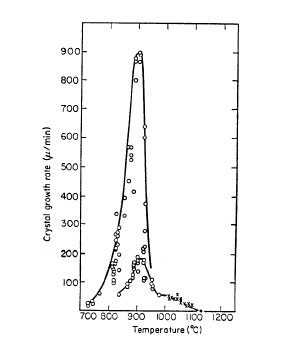
about 10000, i.e. just below the eutectic temperature, in all compositions and the maximum rate of crystallization occurs at about 9000 again in all compositions. As the Li2O content increase, the viscosity at 9000 decreases and the maximum rate of crystallization of the secondary phase increases, as is to be expected. The net result, in this part of the system, is that the stability of the glass decreases as the eutectic temperature is approached.
(ii) Effect of temperature. Detailed measurements have been made by a number of workers of the variation with temperature of the rate of devitrification of a glass of the disilicate composition, Na2Si2O5, which devitrifies to form a crystalline phase having the same composition as the parent glass.Their results are compared in Fig.6. Those of Scott and Pask are in reasonable agreement with
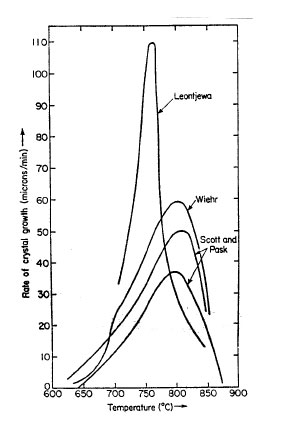
Wiehr's. Leontjewa observed a significantly higher maximum growth rate, which occurred at a temperature 400 below that at which the other results show a maximum. A valuable feature of Wiehr's data is that a relatively large number of repeat measurements were made at each temperature (eight in some cases). Scott and Pask carried out fewer repeat measurements but made direct observations of the crystal growth using a hot stage microscope and identified the particular form of the compound Na2Si2O5 which crystallized. Two crystalline forms are known, the a orthorhombic form stable from 6700 to the melting point (8740) and the b monoclinic form stable below 6700. The transformation of one form to the other is said to be sluggish. Scott and pas observed no discontinuity in the growth rate of crystals of the b form between the temperature region in which it is stable and that in which it is metastable. No transformations from b to a or vice versa were observed during the crystal growth measurements, which extended for times up to 15 minutes. Also no difference was observed between the growth rates of the a and b forms over the entire temperature range in which measurements were made.
However, some evidence for a change in the devitrification kinetics at the a-b transition temperature may be found even in the results of Scott and Pask., where the logarithm of the crystal growth rate, u, is plotted against the reciprocal of the absolute temperature, T. Above the transition temperature the results of Wiehr and Scott and Pask fall on parallel straight lines, the slope of which corresponds to an activation energy of 26 kcal/mole. Wiehr's results show a marked discontinuity nears the transition temperature and the slope of the log u-1/T curve is much steeper below this temperature. No marked discontinuity is observed in Scott and Pask's data. However, their points begin to fall below the line near the transition temperature.
No explanation can at present be offered for this interesting difference between the two sets of results. It may be significant that Wiehr's observations were carried out on specimens heated in air whilst in the high temperature microfurnace used by Scott and Pask, the glass was heated in vacuo. It is known that moisture in the atmosphere increases the speed of the a-b transition. It is therefore possible that in Wiehr's experiments, the glass devitrified to the stable crystalline form at all temperatures, whilst this did not occur in Scott and Pask's work. However, in view of the latter's observation that the rate of crystallization was independent of the particular crystalline form growing in the glass, this "explanation" is not very plausible. It is interesting that Westman and Murthy have observed a similar discontinuity in the log u-1/T plot for NaPO3 glass, but for this material the discontinuity could not be related to a crystallographic inversion in the devitrification product.
Scott and Pask obtained reasonably good agreement between their result and an equation derived by Hilling.
u =ADT1.75
where A is proportional to the fluidity of the glass (i.e. the reciprocal of the viscosity) and DT is the undercooling. The Hillig-Turnbull equation is expected to be valid only when DT is small, but the agreement was found to be satisfactory over the whole temperature range. The fluidity values were obtained from an empirical equation due to Skornyakov which is in good agreement with the experimental results for sodium disilicate glass over the temperature range 600-14000C.
An equation relating the rate of crystal growth, u, and the viscosity, h, which should be more satisfactory than the Hillig-Turnbull equation in that it is not restricted to small values of DT is Turnbull and Cohen's equation.

Figure 8 shows a comparison between Wiehr's data and a curve through points calculated from this equation. Since there is some uncertainty as to the value which should be used for ago, the "jump distance", the calculated curve has been scaled to give a reasonable fit with the experimental curve near the maximum. The agreement is seen to be unsatisfactory, except below the transition temperature where the two curves have practically the same slope.
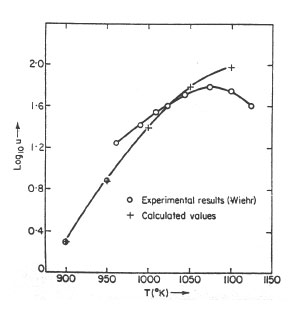
It appears that above the transition temperature, the kinetic process governing the rate of devitrification is one which varies less rapidly with temperature than does the viscosity of the glass.
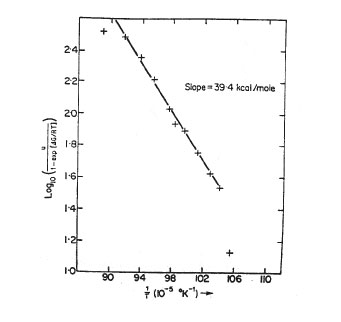
Some indication of the temperature variation of the kinetic factor may be obtained by dividing Wiehr's growth rate values obtained in the temperature range between the liquidus and the transition temperature by the thermodynamic factor (1-exp DG/RT). Apart from one point close to the liquidus temperature, the remainder falls on a straight line having a slope corresponding to activation energy of 39.4 kcal/mole. The activation energy for viscous flow is about 60 kcal/mole in this temperature range. A less detailed analysis of the devitrification kinetics of more complex glasses led Stanworth to a similar conclusion, i.e. that the rate of crystal growth varied less rapidly with temperature than would be expected if the rate were simply inversely proportional to the glass viscosity.
Morley has made an extensive comparison of his experimental data on Na2O-SiO2 and Li2O-SiO2 glasses with three equations which have been proposed to describe the temperature variation of the rate of crystal growth. Two of these were the Hillig-Turnbull and the Turnbull-Cohen equations referred to earlier. The third was an equation derived by Frenkel from a model which involves two-dimensional nucleation of successive planes of atoms as the crystal grows. The least satisfactory agreement between experimental and calculated values was obtained when using the Turnbull-Cohen equation. The Frenkel equation was considered to be slightly more satisfactory than the Hilling-Turnbull equation in that it predicts an asymptotic approach of the crystal growth rate-temperature curve to the temperature axis near the liquidus temperature. The results for the Li2O-SiO2 glasses appear to show this feature. However, Morley is careful to point out that the growth rates are least reliable in this temperature range.
2. Binary Systems Containing Alkaline Earth Oxides
Little information is available on glass formation in other binary silicate systems. It consists very largely of observations made in the course of phase diagram determinations, in which the scale of melting is usually small and the rate of cooling very rapid.
Imaoka have determined the limits of glass formation for 1 g melts in the binary systems containing BaO (40 mole per cent BaO), SrO (40 mole per cent), CaO (56.7 mole per cent) and MgO (42.5 mole per cent). However, in the last three systems single phase glasses cannot be made over the whole composition range from silica to the composition given. Thus in the CaO-SiO2 system between 1 and 28 weight per cent CaO, the melt, at temperatures just above the liquidus, consists of two immiscible phases. Although each phase may form a glass on cooling, the resulting material is of little value or interest.
B. The Na2O-CaO-SiO2 System
1. Structural Considerations
It is generally believed that the introduction of calcium oxide into a silicate glass has a qualitatively similar effect on the structure to that produced by the introduction of Na2O. However, because of the greater charge of the Ca2+ ion, the Ca-O bond is much stronger than the Na-O bond. The calcium ions are held more firmly in the structure than the sodium ions as is shown by the fact that they make no significant contribution to the electrical conductivity of the glass, which is due almost entirely to the migration of sodium ions. Replacement of Na2O by CaO results in a considerable improvement in the chemical durability, the thermal expansion coefficient of the glass is reduced and the viscosity of the melt increased all indications of an increase in the coherence of the structure.
The addition of CaO, and to a somewhat greater extent Mgo, to an Na2O-SiO2 glass increases the stability in that glasses can be made with a lower silica content. Thus Moore were able to make a glass on a 6 g scale of composition 0.84 Na2O. 0.02 CaO.1.00 SiO2, i.e. with 49 mole per cent SiO2. The limit in the Na2O-MgO-SiO2 system, the silica content could be reduced even further. Thus a glass was made of composition 0.84 Na2O. 0.35 MgO.1.00 SiO2, i.e. with 45.7 mole per cent SiO2. Moore and Carey suggested that in these glasses the oxides MgO and CaO, because of the Strong Mg-O and Ca-O bonds, were able to preserve the continuity of the silicate network, and acted to some extent as network formers. This use of the term "network former" is hardly acceptable. However, it is plausible that the essence of Moore and Carey's suggestion is correct, that the strong R-O bonds impede the rearrangement of the silicate structure which occurs when the glass devitrifies.
2. The Glass-forming Region
The result of the most recent determination of the glass-forming region in this system is shown in Fig.10, due to Imaoka and Yamazaki. The scale of melting was 1-2 g and the melts were made in platinum. The boundary of the field of glass-forming compositions is found to lie slightly on the low SiO2 side of the line joining the points representing the binary compositions containing 50 mole per cent SiO2. This diagram does not show the region of immiscibility which is to be found close to the CaO-SiO2 side of the diagram. However, the region is not very extensive. The addition of a few per cent of Na2O to the two-phase CaO-SiO2 melts converts them into single-phase materials. The diagram is broadly in agreement with the results of earlier work, although Berger reported two distinct regions in which glasses could be made, a broad region extending from the Na2O-SiO2 side of the diagram and a more restricted region adjacent to the CaO-SiO2 side. Composition between these regions could not be melted at the maximum temperature attainable in his furnace (15000C).
3. The Phase Diagram
Morey has determined the phase diagram of that part of the Na2O-CaO-SiO2 system in which glasses are formed. The region of the diagram which is of most interest is that shown in Fig.11. It contains the compositions which form the basis of all commercial soda-lime-silica glasses. Also all the available data on rates of
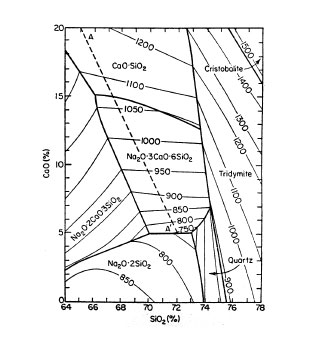
devitrification have been obtained on compositions in this part of the system. The diagram shows the primary crystalline phases which are formed. These are the various phases of silica (quartz, tridymite and cristobalite), wollastonite (CaO.SiO2), devitrite (Na2O.3CaO.6SiO2), sodium disilicate (Na2O. 2SiO2) and the compound Na2O.2CaO.3SiO2. The numbered contour lines join compositions having the same liquidus temperature. The lowest liquidus temperature (7250) occurs at the ternary eutectic between quartz, sodium disilicate and devitrite. The eutectic composition is 5.2 per cent CaO, 21.3 per cent Na2O, 73.5 per cent SiO2.
4. Devitrification Kinetics
Although a number of investigations have been made of the rates of devitrification of individual glasses, relatively little has been done to study the effect of systematic changes of composition. Dietzel has studied twenty-four glasses in the region from 12 to 20 weight per cent Na2O and 6 to 16 per cent CaO. The contour lines join compositions for which the times taken to grow crystals 10 micron in length are the same. Thus along the line labeled 5 sec, the maximum rate of crystal growth is 2 micron/sec. The dotted line on the diagram labeled "line of Morey and Bowen" corresponds to the line on the phase diagram which separates the phase fields of tridymite and cristobalite from those of wollastonite and devitrite. The second dotted line joins the most stable glass compositions in this part of the system. Dietzel pointed out that in these compositions the sum of the Na2O and CaO contents is about 26 weight per cent. A clearer picture of the relationship between glass stability and liquidus temperature for these glasses may be obtained from Fig.12, in which Dietzel's results have been replotted and super imposed on the phase diagram. In the tridymite field the lines of equal rate of crystallization run almost parallel to the liquidus temperature contours. The higher the liquidus temperature, the less stable are the glasses. In the devitrite and wollastonite fields, the liquidus temperature is practically independent of the silica content. However, as the silica content is decreased, the viscosity at the liquidus temperature decreases, which may account for the increased rate of crystallization which is observed, particularly at high CaO contents. Littleton has pointed out that for the glasses containing 14 or 16 weight per cent Na2O, studied by Dietzel, the maximum rate of crystal growth is inversely proportional to the viscosity at the corresponding temperature. All these compositions are in the tridymite field. Although the validity of this relationship has not been investigated for all the glasses studied by Dietzel, it would appear that the general pattern of glass stability in this part of the system can be explained in terms of the effect of composition on liquidus temperature and viscosity.
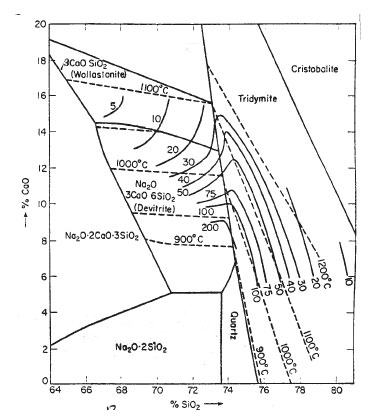
More stable glasses can be made if the CaO in an Na2O-CaO-SiO2 glass is partly replaced by MgO. Swift showed this effect in a series of glasses based on the ternary composition 74 per cent SiO2, 16 per cent Na2O, 10 per cent CaO, i.e one of Dietzel's more stable glasses. The CaO was replaced in 2 weight per cent steps by MgO. Up to 6 per cent MgO the liquidus temperature decreases with increasing MgO content and the rates of crystallization of both the primary and secondary crystalline phases decrease correspondingly. With further replacement of CaO by MgO the liquidus temperature rises and the stability of the glass decreases. Swift also showed that the introduction of Al2O3 has a similar effect in increasing the stability of the glass.
C. SOME SPECIAL SILICATE GLASSES
1. Alkali Aluminosilicates
A well-known feature of the structure of silicate minerals is that silicon ions may be replaced isomorphously by aluminium ions provided that either univalent or divalent cations are available to maintain local neutralization of charge in the structure. This feature is shown particularly well by the framework silicates, which have silica-like structures, the univalent or divalent cation being held in voids in the framework formed by the SiO4 and AlO4 tetrahedra. In these materials the ratio R2O/Al2O3 or RO/Al2O3 is unity and no non-bridging oxygens are present.
It is also a feature of silicate minerals that aluminium ions are also found with an oxygen co-ordination number of 6. In the terminology of the Warren-Zachariasen network theory, the Al2O3 is then behaving as a network modifier. There is a considerable amount of evidence suggesting that the same situation is found in alkali aluminosilicate glasses. It is believed that when the ratio
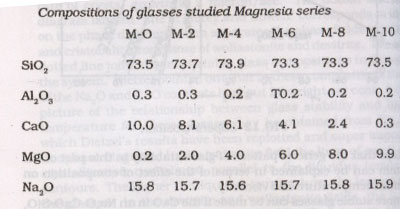
R2O/Al2O3]1 all the aluminium ions are in fourfold co-ordination, and that aluminium ions in sixfold co-ordination are found only when the ratio R2O/Al2O3[1. Thus one may expect that the alkali alumino-silicate glasses which have a ratio R2O/Al2O3 of unity will have silica-like structures. Even though the glass structure may not be known with certainty, it is known that these glasses have particularly high viscosities, comparable with that of fused silica. However, they have liquidus temperatures considerably below the melting point of silica. The phase diagram of the Na2O-Al2O3-SiO2 system shows that as Na2O and Al2O3 are added in equimolecular proportions to silica, the liquidus temperature decreases to 10620 at the eutectic composition, 8% Na2O.15% Al2O3.67% SiO2 (by weight), and then slowly rises to 11200 at the composition of albite, Na2O.Al2O3.6SiO2. The viscosity of albite at the melting point is 108.5 poise-about 1000 times greater than the viscosity of a commercial soda-lime-silica glass at its liquidus temperature. It is not surprising that such a glass is extremely difficult to devitrify. Schairer reported that no sign of crystallization was observed on heating albite glass for several years at various temperatures in the range of to 1000 below the melting point. It could, however, be devitrified in a matter of hours by a "conditioning treatment", which involved heating the melt for progressively increasing periods at a series of decreasing temperatures above the melting point with a final treatment below the melting point. Apparently the melt structure must be brought into a favourable configuration before crystallization can occur and this configuration can only be attained at a measurable rate at temperatures above the melting point. This remarkable behaviour has not been observed for any other glass, although some of the recent work on fused silica may indicate a similar though less marked pattern of behaviour in this material. In spite of the astonishing nature of Schairer's observations, no attempt seems to have been made to investigate these effects any further.[/P]
2. Invert Glasses
We have seen earlier that glasses of lower SiO2 content can be made in the ternary systems Na2O-MgO-SiO2 and Na2O-CaO-SiO2 than in the binary Na2O-SiO2 system. Trap have shown that the SiO2 content can be reduced still further (as low as 40 mole per cent) as the glass composition is made more complex. They found it helpful in discussing the properties of their low silica glasses to express the glass composition in terms of a parameter Y, the average number of bridging oxygen ions per SiO4 tetrahedron, which may be calculated from
Y = 6-200/p
where p is the mole percentage of silica. At 40 mole per cent SiO2 the value of Y is 1, i.e. the structure of the glass may contain pairs of tetrahedra, although it is recognized that a mixture of isolated tetrahedra and longer chains would also be possible. Figure 13 shows the structure of one of these glasses for which Y is less than 2, i.e. the silica content is less than 50 mole per cent.
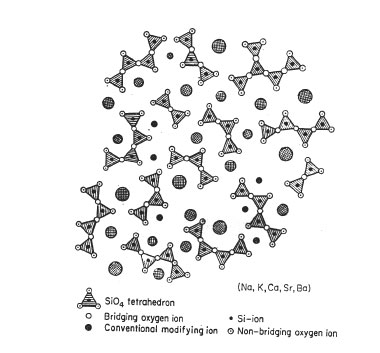
Trap and Stevels suggest that there is an inversion in the structural role of the modifying ions at the 50 mole per cent SiO2 composition, hence their use of the term "invert glasses" for the materials containing less than this percentage of silica. Above 50 per cent SiO2 the modifying ions destroy the continuity of the silica network; below this percentage, they argue, glass formation is understandable only if one thinks of the random structure of the glass as being stabilized by the ionic bonds acting between the modifying cations and the small groups of SiO4 tetrahedra. Curves relating the values of certain physical properties with the parameter Y were found to show marked changes at the critical value of Y = 2. These changes were interpreted as supporting the suggestion of a change in the function of the modifier cations.
Glasses with Y = 1 were made in the systems SiO2-K2O-CaO-SrO, SiO2-K2O-CaO-BaO and SiO2-Na2O-K2O-BaO. Stevels considers that an asymmetry in bond strengths caused by the presence of a number of ions of widely differing field strengths is the relevant factor in understanding why these materials form glasses. It is perhaps a matter of opinion whether this is a helpful way of considering the problem. More work on the factors likely to affect the stability of these glasses is certainly needed. In particular one would like to know if making the composition more complex results in a reduction in liquidus temperature. We know that this happens when MgO is added to an Na2O-CaO-SiO2 glass and that the stability of the glass increases as a result. It should also be remembered that most complex glasses crystallize to form phases differing in composition from the parent glass. The growth of a crystal in such a material involves the diffusion of oxides either towards or away from the crystal-glass interface. It is possible that these diffusion processes occur with greater difficulty when the composition of the glass is made more complex.