Chemical industry based on Sodium Sulfide Flakes
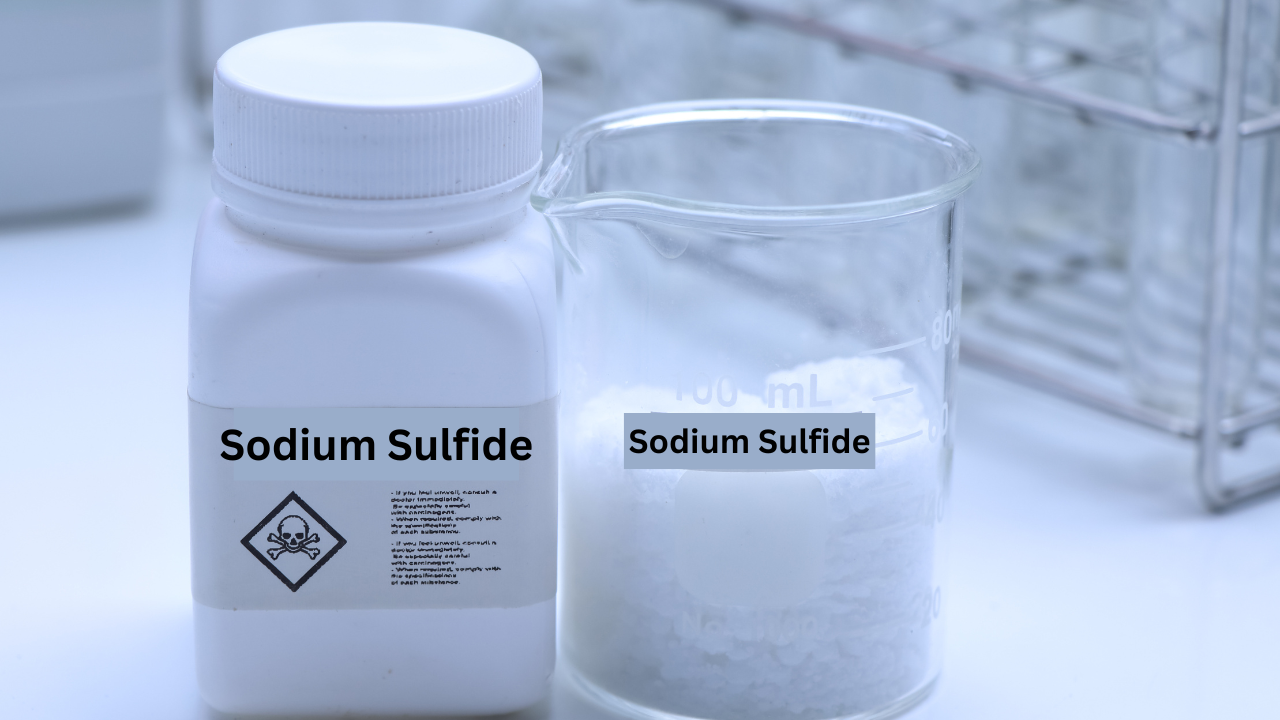
One such chemical compound is Na₂S, a very essential component in various industries, from the production of paper and water treatment to mining. One of the common forms that is used as a result of its convenience and easy handling is sodium sulfide flakes. These flakes are usually produced from sulfur, which is an element that occurs naturally.
Properties of Sodium Sulfide Flakes are -
Appearance: The colour of sodium sulfide flakes can range from yellow to red. It depends on the amount and type of impurities that might be present and, obviously, on the production process itself.
Solubility: Sodium sulfide is soluble in water
Reactivity:Sodium sulfide is reactive with acids which release hydrogen sulfide gas (H₂S), which is toxic and requires careful handling.
Processes to produce Sodium Sulfide Flakes from Sulphur?
-
Formation of Sodium Sulphide :The sulfuric acid is subsequently neutralized with soda ash, sodium carbonate, to produce sodium sulfate, Na₂SO₄. This sodium sulfate is then heated in excess with carbon, normally in the form of coke, to produce sodium sulfide.
Related Project Report : Chemicals (Organic, Inorganic, Industrial) Projects
Advantages of opening chemical industry based on Sodium Sulfide Flakes
-
There is very high demand for sodium sulphide flakes in various industrial applications like pulp, paper, textile, leather Tanning etc.
-
It acts as a crucial player in the production of sulphur dyes, rubber, chemicals and other speciality chemicals.
-
Sodium sulfide is applied to dehairing in the leather-making process and further in dyeing and finishing for textiles.
-
It's used in ore flotation and extraction of metals such as zinc, copper, and lead.
-
The manufacturing process of sodium sulfide flake is known and involves simple chemical reactions, mainly the reduction of sodium sulfate with carbon.
-
This process can be scaled up or down for production as per demand.
-
Raw materials for manufacturing sodium sulfide, such as sodium sulfate and carbon, are inexpensive and readily available.
-
Sodium sulfide flakes have higher value addition over its raw materials, thus attracting good profit margins.
-
Rich natural resources in a country, such as sulfur, coal, and natural gas, can reduce production costs and make you gain profit.
-
A country with ample natural resources and a well-built industrial base, supplemented by port facilities, can easily export sodium sulfide flakes to markets around the world.
-
Advanced technology controls emissions and waste, ensuring that the operation is within environmental regulations.
-
Establishing a sodium sulfide plant creates jobs in production, maintenance, logistics, and administrative areas.
-
In turn, this creates skill development and training opportunities related to the manufacture of chemicals.
-
These are supplemented by many governments' incentives, subsidies, and support for developing chemical industries, including tax breaks and support in infrastructure.
-
A clear regulatory framework can therefore offer a stable environment for business operations and expansion.
Profit of opening chemical industry based on sodium sulfide flakes
-
Production Costs: The cost of raw materials, production processes, and operational costs are all constitutive factors. The implementation of efficient methods of production may help to shore up margins.
Challenges
-
The demand for sodium sulfide flakes can be volatile, influenced by changes in industries that use the product.
-
Difficulty in securing supply of raw materials consistent and reliable and arranging logistic for distribution.
-
Setting up a Chemical Manufacturing Plant involves huge capital investment in equipment, facilities, technology etc. Adequate financial planning and arranging sources of finance is also most essential.
-
Technical expertise to produce Sodium Sulfide flakes requires its development and up-gradation, it is most essential.
-
The production of sodium sulfide may lead to environmental hazards like pollution. Proper waste management and pollution control should thus be put in place to ensure reduced harm to the environment.
-
There could be existing competition in the chemical industry, and thus many established players could be engaged in the manufacture. It is always tricky to differentiate your products in a market already occupied by established individuals.
Considerations -
-
Invest in appropriate production technology and infrastructure. With efficient production processes and quality control, it is possible to have a product at a very competitive price and consistent quality.
-
Set up proper control measures to ensure your sodium sulfide flakes meet industry standards and customer expectations.
-
Invest in R&D for product and process upgrading. It opens new markets and creates opportunities for better performance and cost savings.
-
Create a detailed business plan that includes startup costs, operational expenses, and revenue projections. Ensure you have sufficient capital for initial investment and ongoing operations.
-
Consider incorporating sustainability into the operations. This will ensure brand realization and increase demand for green products.
-
Test for rigorous quality control procedures to ensure that your sodium sulfide flakes meet industry standards and customer expectations.
-
Sodium sulfide is a hazardous substance that has to be stored in appropriate facilities for handling and storage.Strict safety measures are to be implemented to safeguard the workers from any kind of accident or misfortune.
| Best places to open industry based on Sodium sulfide flakes in India |
-
Mumbai, Pune, Navi Mumbai and Nagpur of Maharashtra
-
Dahej, Vadodara and Ankleshwar Of Gujarat
-
Chennai, Cuddalore and Tuticorin of Tamil Nadu
-
Visakhapatnam and krishnapatnam of Andhra Pradesh
-
Paradeep and Angul of Odisha
-
Bangalore and Mangalore of Karnataka
-
Alwar and Bhiwadi of Rajasthan
CONCLUSION
Setting up an industry in sodium sulfide flakes is a strategically critical enterprise with huge market potential in the textile, leather tanning, paper, and mining industries. The journey to setting up this industry involves several critical steps that ensure a well-planned, sustainable, and profitable operation.
Grasp of dynamics in demand, competitor landscapes, and pricing trends would show the opportunities and challenges of the market. It acts as the backbone of a business plan where the vision is characterised with financial and operation strategies. The right location selection would aid in the optimization of production efficiency and logistics enabling. If all the steps mentioned above are combined with the attributes of quality, safety, and sustainability, then an entrepreneur could successfully build up a profitable chemical industry.
For any Inquiry on Chemical Industry : Visit NPCS
See More Links:
YouTube Channel
Startup Consulting Services
Start a Business in Middle East Countries
Most Demandable Business Ideas for Startups
Business Ideas with Low, Medium & High Investment
|