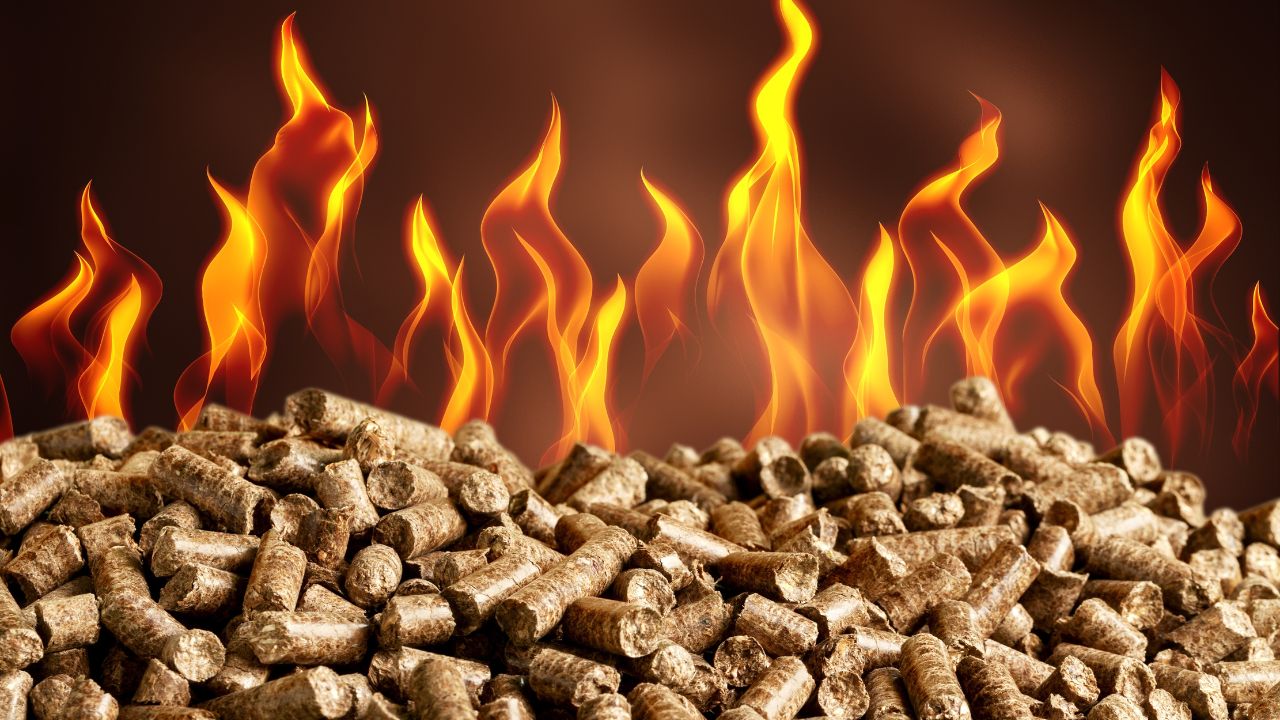
At present, renewable energy sources are more essential than ever to our world. A sustainable solution lies in producing biomass pellets from bio waste as an eco-friendly replacement to fossil fuels while offering lucrative opportunities to startups and entrepreneurs looking to make an impactful mark on this field.
Biomass Pellets Biomass pellets are organic waste materials such as wood waste, agricultural residues and other biodegradable waste that is compressed and formed into pellets for energy usage. Used in boilers, home heating systems and power plants as a renewable source of energy source replacing coal, biomass pellets can significantly lower carbon emissions while simultaneously improving waste management practices and stimulating local bio-economy initiatives. The advantages of using biomass pellets for power production can include reduced emissions; improved waste management techniques; stimulating local bio-economies within communities.
Visit this Page for More Information: Start a Business in Biotechnology Sector
Start-Up Costs for Biomass Pellet Production
Initial Investment
Initial investments to launch a biomass pellet production business can vary widely based on scale and location of operation. Key expenses may include:
· Equipment Costs: These costs encompass purchasing pellet mills, dryers, grinders and conveyors - typically with smaller businesses starting with investments of between $100,000-$1M; larger enterprises could require much larger capital outlays.
· Land and Building: Entrepreneurs should ensure sufficient space is set aside for raw material storage, production lines and finished goods storage in their facility construction or leasing plans to avoid incurring high construction or leasing costs.
· Raw Material: Ensuring a reliable supply of bio waste is of vital importance; costs involved here depend on its type and availability in your region.
· Utilities: Operating heavy machinery and processing systems requires significant energy usage, with water and other utilities adding significant operational expenses.
· Licenses and Permits: Depending on local regulations, various permits may be needed in order to operate, including environmental and safety approvals.
Operational Costs
· Labor: This costs include wages, training and insurance of both skilled and unskilled labor.
· Maintenance: Regular equipment maintenance can prevent downtime and ensure efficient production.
· Transportation expenses: related to transporting raw materials and finished pellets between plants.
· Marketing and Sales expenses: which cover expenses related to marketing pellets to buyers.
Related Business Plan: Biomass Pellets from Bio Waste
Niir Project Consultancy Services (NPCS) specializes in offering project feasibility and support for biomass pellet production from bio waste. Our services include:
· Market Research Reports: At our market research reports services, we conduct in-depth market analyses that reveal industry trends, competition and potential buyers in depth.
· Comprehensive Project Reports: Our expert team offers detailed project reports that cover both technical and financial aspects of biomass pellet production projects, including feasibility analyses, expected ROI calculations, project costs estimations and revenue projections.
Read Similar Articles: Biotechnology and Biotech Sector
Utilize Local and Global Markets
Demand for biomass pellets is strong both domestically and abroad. Many European countries heavily incentivize renewable energy, creating attractive markets for biomass pellets. Startups should investigate export opportunities; although this might require additional certifications to comply with international standards, these opportunities often provide higher profit margins and diversify revenue streams.
Environmental Impact and Compliance
One of the main advantages of starting up a biomass pellet production unit is its positive environmental impact: companies can significantly reduce landfill waste and greenhouse gas emissions by turning bio waste into energy, but startups must navigate through complex environmental regulations successfully in order to be successful.
· Emissions Standards: Ensuring that emissions from production processes meet local and international regulations for emissions. Waste Handling: Proper procedures should be established for handling and disposing of any residual waste created during production processes.
· Sustainable Sourcing: For environmental sustainability purposes, bio waste must be obtained sustainably so as not to deplete natural resources.
Technological Advancements and Efficiency
Advancements in technology play a key role in optimizing biomass pellet production. Making investments in new pelletizing technology can increase production efficiency, decrease energy usage and enhance product quality while automating parts of the production process can cut labor costs while improving safety.
Training and Development
To keep a biomass pellet production facility operating smoothly and efficiently, having a highly trained workforce is of utmost importance. Investing in training programs focusing on machine operation, safety protocols and maintenance can yield substantial long-term advantages by minimizing operational errors and downtime; furthermore, ongoing professional development keeps teams abreast of industry practices and technologies.
Related Feasibility Study Reports: Biotechnology, Bio-Technology, Industrial Biotechnology, Biotech Sector, Industry, Biotech Projects, Enzymes Papain, Phytase, Lipase, Enzyme, Food Biotechnology, Industrial Enzymes, Vermiculture , Vermicompost , Biofertilizer, Organic Farming, Biogas
Before embarking on their biomass pellet production journey, prospective entrepreneurs should carefully consider several key points:
· Site Evaluation: Selecting an ideal location takes careful thought into account factors like raw material suppliers, target markets and regulatory environment.
· Financial Planning: Precise financial planning, such as securing funding, budgeting for unanticipated expenses, and cash flow management is key to the longevity of any business.
· Long-Term Strategy: Formulate an innovative plan that includes expansion, diversification and technological upgrades as a long-term approach in order to stay competitive in the market.
Engage NPCS for Your Project Needs
Are You Ready to Establish a Biomass Pellet Production Facility? NPCS Offers Unmatched Expertise and Commitment to Client Success
Ready to move ahead in setting up a biomass pellet production facility? NPCS stands ready with unrivaled expertise, offering project reports and providing deeper insights via their explainer video in order to get an understanding of its full scope and potential as a business venture.
With proper planning and strategic support from NPCS, your venture into biomass pellet production from bio waste can flourish successfully and contribute towards global renewable energy transition. Navigating Challenges and Risks in Biomass Pellet Production.
Supply Chain Management
A successful biomass pellet production business depends on effective supply chain management. Entrepreneurs must establish strong relationships with local farms, forestry operations and waste management facilities as suppliers for bio waste. Furthermore, considering logistics of transporting raw materials directly to their production facility is also vitally important in order to minimize costs and optimize efficiency.
Read our Book Here: Handbook on Small & Medium Scale Industries (Biotechnology Products)
Quality Control
Quality control is vital to the success of biomass pellets on the market. To do this successfully requires rigorous testing of pellets to meet specific density, moisture content, and energy output requirements. Establishing an effective quality control system will help avoid issues like high ash content or inconsistent pellet size which could impede combustion efficiency or market acceptance.
Technological Integration Integrating technology into production processes can yield enormous advantages, from increasing production rates and improving consistency, to real-time monitoring systems that offer real-time data that optimize operations and reduce downtime. Utilizing automation for sorting, drying and pelletizing bio waste can greatly accelerate these processes as well as create market penetration strategies.
Effective market penetration strategies are essential to reaching potential customers and expanding market share. This may involve:
· B2B Marketing: Targeting large industrial consumers of biomass pellets like power plants or heating facilities
· B2C Marketing: Reaching residential customers directly by forming relationships with local energy providers or offering direct-to-consumer sales.
· Promotional Campaigns: By engaging in promotional campaigns through various mediums such as online platforms, industry exhibitions and green energy conferences to spread awareness of biomass pellet benefits, promotional campaigns can raise public awareness.
Innovation and Research
Continuous investments in research and development can give your company an edge in its industry. Examples might include developing more efficient pelletizing processes or pellets with cleaner burning characteristics that last longer. Partnering with academic institutions and research centers can give access to cutting-edge advancements and funding opportunities.
Promoting the environmental benefits of biomass pellets is key to building customer loyalty and improving brand image. Adopting sustainable practices throughout production such as cutting water use and waste generation helps further environmental conservation initiatives.
Watch Video: Biotechnology, Bio-Technology, Industrial Biotechnology, Biotech Sector, Industry, Biotech Projects, Vermicompost , Biofertilizer, Organic Farming
Scaling Up
As your business expands, expanding production capacities may become necessary in order to meet increasing demand. This may involve expanding the current facility or investing in more advanced machinery; or opening additional plants at strategic locations.
Starting a biomass pellet production from bio waste business venture is both financially lucrative and environmentally sustainable. By taking an effective approach with help from experienced consultants like NPCS, entrepreneurs can overcome any hurdles they encounter while capitalizing on opportunities available in this thriving sector.
Are You Ready to Begin Your Journey?
Are you ready to explore the vast opportunities in biomass pellet production? NPCS’s experts are available now to guide and ensure the success of your venture. Visit our project report section and watch our informative video now to begin on your path towards creating sustainable renewable energy solutions that benefit future generations.
Conclusion:
Launching a biomass pellet production business from bio waste not only supports global sustainability initiatives but also presents an attractive economic return. With guidance and assistance from NPCS, entrepreneurs can easily navigate this complex endeavor, guaranteeing both environmental and financial success in one go.
Making an investment in biomass pellets production from bio waste can not only be financially smart but also environmentally responsible. With guidance and advice from NPCS, entrepreneurs can successfully navigate this venture and contribute positively to global sustainability efforts.
With growing demand for sustainable and renewable energy sources like biomass pellets making an eco-friendly business opportunity available to startups, selecting NPCS will grant access to thorough market analyses, financial forecasts, step-by-step guidance on starting your venture successfully and access to our expert guidance in optimizing operations and growth potential of your business.
See More Links:
Youtube Channel
Startup Consulting Services
Start a Business in Middle East Countries
Most Demandable Business Ideas for Startups
Business Ideas with Low, Medium & High Investment