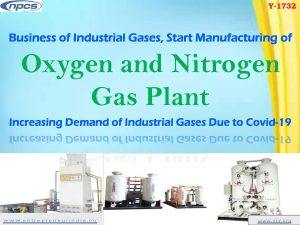
Introduction:
Industrial gases are used in a variety of ways. Its properties allow it to play an important role in a wide range of industries, including steel, chemicals, electronics, and automobiles, as well as glass, shipbuilding, construction equipment, paper manufacturing, food and beverages, medical care, agriculture, and space exploration. Our consumers around the country rely on Air Water for a consistent supply of industrial gases including oxygen, nitrogen, argon, and carbon dioxide. Oxygen plants are large manufacturing systems that produce oxygen. They usually use air as a feedstock and use pressure swing adsorption or membrane separation techniques to distinguish it from other components of air. Cryogenic separation facilities, on the other hand, isolate and collect all of the components of air. Oxygen is used in a wide range of technological processes and in almost every industry.
Related Projects: Oxygen and Nitrogen Gas Plant (Medical and Industrial Grade)
The primary application of oxygen is linked to its ability to withstand the burning process as well as its strong oxidant properties. Nitrogen gas is one of the most common elements present in the atmosphere, and it has a variety of industrial applications. This is due to the fact that one of this gas's most unusual properties is its ability to form numerous bonds with other elements and compounds. As a result, compressed nitrogen gas is extremely flexible and can be used in a variety of applications. As a result, compressed nitrogen gas is extremely flexible, and it can be used in a variety of applications in a wide range of industries. Nitrogen gas is used to maintain an adequate environment for highly sensitive procedures and equipment by controlling oxygen levels, humidity, and temperature. Additionally, nitrogen is needed for purging a variety of laboratory instruments.
Uses of Oxygen and Nitrogen Gas Plant:
Breathing equipment for underwater work, as well as self-contained breathing apparatus for refineries and chemical plants, all use oxygen. Aquaculture, or the raising of fish in ponds, makes use of oxygenated water to ensure that there is always enough oxygen available and that more fish can be raised or stored in a given size of pond or tank. The oxygen is used in the same way as it is in any other gasification phase. The benefit now is that the waste nitrogen can be used for a number of purposes. Injection into the gas turbine to improve performance, refrigeration for the turbine inlet air, and low process nitrogen could be used for chilling applications are some of these applications. Oxygen is used in a number of sectors for a variety of purposes. The use of oxygen in the glass, gasification, and gas-to-liquid industries will be discussed in this section. The use of oxygen in urban solid waste and coal gasification processes, as well as the gas to liquid industry, would be the primary concern. Current metal oxidation studies will also be discussed. Industrial systems designed to produce oxygen are known as oxygen gas plants. They usually use air as a feedstock and use pressure swing adsorption or membrane separation techniques to distinguish it from other components of air. Cryogenic separation facilities, on the other hand, isolate and collect all of the components of air. By lowering the oxygen level below explosive limits, nitrogen is commonly used to avoid fires and explosions in hazardous environments such as chemical plants or manufacturing facilities. When two electronic components form a permanent bond, also known as soldering, nitrogen gas is used in the process of assembling electronics. The gas is used to lower surface tension, allowing for a smoother break away from the electrical bonding site.
Related Project: Oxygen and Nitrogen Gas Plant
Nitrogen gas is also used to avoid overheating in a computer's main processing system. Nitrogen gas, because of its low reactivity, can be used to replace oxygen and other gases that are more vulnerable to spontaneous combustion or oxidation in industrial gas lines and other volatile processes. Nitrogen purging ensures that manufacturing processes remain stable and healthy. Compressed nitrogen is often used by food processing firms to replace oxygen in the packaging of perishable foods. Foods such as meats, fruits, vegetables, and a variety of snack foods may have their shelf life extended by removing oxygen. Nitrogen may also function as a cushion to protect food during transportation.
Related Book: The Complete Book on Industrial Gases (Acetylene, Argon, Butane, Butene, Carbon Dioxide, Carbon Monoxide, Ethane, Ethene, Helium, Hydrogen Chloride, Hydrogen, Krypton, Liquefied Natural Gas (LNG), Methane, Neon, Nitrogen, Nitrogen Trifluoride Gas, Nitrous Oxide, Oxygen, Ozone, Propane, Propene, Refrigerant Gases, Sulphur Dioxide Gas, Sulphur Hexafluoride Gas, Xenon, Gas Mixtures with Machinery Equipment Details and Factory Layout)
Manufacturing of Oxygen and Nitrogen Gas Plant:
Compressed oxygen, liquid oxygen, and nitrogen are the four materials. d) All liquid nitrogen is extracted in the same plant from air. The raw material, air, is cryogenically liquefied, and the liquid oxygen and liquid nitrogen components are separated in a fractional distillation column. Compressors / pumps bottle compressed oxygen and nitrogen gases into cylinders. After vaporisation of the respective liquid fractions, compressed oxygen and nitrogen gases are bottled into cylinders by compressors / pumps. The air is compressed to a pressure of 30kg/cm2 in three steps. Following that, water vapour and carbon dioxide are removed using a battery of molecular sieves. The carbon dioxide and water vapor-free air is compressed still more to a pressure. External refrigeration is used to compress the outgoing carbon dioxide and water vapour free air to a pressure of 100 kg/cm2 and cool it significantly. The outgoing product gases cool the high-pressure air even further in heat exchangers. The majority of the cold air is allowed to expand via an expansion motor, while the remainder is redirected via an expansion valve. The expansion engine's downstream air reaches a pressure of 5 kg/cm2 and a significantly lower temperature. Partially liquefaction of air occurs when the other stream of air passing through the expansion valve is extended to a pressure of 5kg/cm2.
Related Videos: Industrial, Medical and Specialty Gases Manufacturing Project Ideas
Both streams of air are combined and added to the bottom column of the double rectification column as a liquid vapour mixture (fractional Distillation Column). Because of mass and heat transfer at each perforated tray in the column, nitrogen-rich liquid vapour collects at the top trays, while an oxygen-rich liquid-vapor mixture collects at the bottom trays. The liquid nitrogen that has accumulated at the top of the bottom column is drawn out and stored in vacuum-insulated cryogenic tanks as a product. This liquid nitrogen is pumped from the storage tank via vaporizers for gasification and bottling into cylinders to produce nitrogen gas. The oxygen-rich liquid-vapor mixture at the bottom column's sump is redirected to the distillation column's top column, which operates at a lower pressure of 0.5kg/cm2. Further separation of oxygen and nitrogen vapour occurs in this low-pressure column through a mass and heat transfer process at the various trays inside the column.
Related Books: - BOOKS & DATABASES
Due to heat exchange with the cooler liquid nitrogen produced at the top of the bottom column, the separated oxygen vapours settle at the bottom of this column and condense to form liquid oxygen. The liquid oxygen that has accumulated at the bottom of the top column is extracted as a result and stored in vacuum-insulated cryogenic tanks. This liquid oxygen can be vaporised by heat exchange between incoming process airs and compressed by oxygen compressors for bottling into cylinders to produce compressed oxygen. Alternatively, the stored liquid oxygen may be pumped into vaporizers for gasification and cylinder filling. The plant's processing modes can be changed to produce:
1) Liquid nitrogen and compressed oxygen, with in-built vaporizers filling compressed oxygen, or
2) Liquid oxygen only, with external vaporizers filling compressed oxygen, depending on requirements.
Market Outlook:
The most popular gases used in industrial gases are oxygen, hydrogen, nitrogen, and carbon dioxide. Argon, neon, xenon, and krypton are some of the other natural gases. Industrial gases are transported in liquefied form to end-use industries through gas tankers. Cryogenic filtration of air by air separation units is commonly used to produce these gases. The growth of the industrial gases market is fueled by factors such as increased metal manufacturing and processing industries such as oil & gas, food & beverages, and others.
The use of industrial oxygen in a wide variety of applications has boosted demand in the industry. The expansion has been fueled by the use of oxygen in the metalworking industry and urban solid waste gasification. To ensure a consistent supply of industrial oxygen in developing countries, a number of steel producers have teamed up with manufacturers and sellers of the gas. Several end-use industries have attempted to narrow or close the oxygen supply-demand gap. The outlook for the industrial oxygen market has improved as a result of this. The market has also benefited from advances in the chemistry of oxygen production.
Market Research: - Market Research Report
Increasing Demand of Oxygen Gas Due to Covid-19:
The COVID-19 epidemic resulted in a major rise in global demand for medical oxygen. During the COVID-19 pandemic, optimal medical infrastructure use became a top priority for governments all over the world. Medical oxygen gas is being imported and manufactured locally with a focus on ensuring its continuous supply to designated COVID-hospitals identified by the local administration. The paper informs the reader about the administrative and regulatory orders that regulate the supply and transportation of medical oxygen gas. Due to a rise in oxygen demands due to COVID-19, the Center for Global Development (CGD) stressed the importance of striking a balance between immediate needs and long-term cost-effectiveness. Now is the time to put medical oxygen first. Oxygen, like electricity and water, should be considered as a critical utility. It will not be easy for the global community to adopt structural solutions that save lives now and improve oxygen access in the long run.
Key Players:
· Air Liquide India Holding Pvt. Ltd.
· Arrow Oxygen Ltd.
· Bellary Oxygen Co. Pvt. Ltd.
· Bhagawati Oxygen Ltd.
· Bhilai Oxygen Ltd.
· Govind Poy Oxygen Ltd.
· Howrah Gases Ltd.
· Linde India Ltd.
· Madhav Industrial Gases Pvt. Ltd.
· Niket Udyog Ltd.
· Praxair India Pvt. Ltd.
· Pushya Industrial Gases Ltd.
· Rukmani Metals & Gaseous Pvt. Ltd.
· Saraogi Oxygen Ltd.
· Southern Gas Ltd.
· Travancore Oxygen Ltd.
For More Details: https://niir.org/profile-project-reports/profiles/industrial-gases-projects/z,,23,0,a/index.html
#DetailedProjectReport #businessconsultant #BusinessPlan #feasibilityReport #NPCS #entrepreneurindia #startupbusiness #ProjectReport #startup #projectconsultancy #businessopportunity #NewBusinessPlan #BusinessProfessional #BusinessConsulting #NitrogenGasPlant #OxygenGasPlant #IndustrialGases #Gases #GasesPlant #IndustrialPlant #GasesMarket #IndustrialGasesMarket #MedicalGasesMarket #NitrogenGasMarket #IndustrialGasIndustry